The 4M method is a simple problem-solving tool that allows us to brainstorm, identify, and group potential factors that cause problems. To be more effective during the implementation of 4M method (Ishikawa), we could use an additional Checklist. The 4M Checklist is an essential part of completing the perfect implementation of the 4M method. There is a standard set of questions that you should ask and review during the brainstorming phase. These questions have a goal to help you identify potential causes, but also to drive you systematically through the problem-solving process. Usage of the checklist is prevention to not forgetting some of the hidden or not-so-obvious causes.
Table of Contents
ToggleThe 4M Checklist
The checklist should cover questions from each 4M section:
- MEN – Set of questions related to direct & indirect labor and their responsibilities, knowledge & experiences, training, hiring, compensation, benefits, motivation, etc.
- METHOD – Set of questions related to working methods – standards, instructions, specifications, guidelines, control plans, etc.
- MATERIAL – Set of questions to discover the status, quality, quantity, conditions, flow, and handling of both direct & indirect materials.
- MACHINE – Set of questions related to equipment, jigs, gauges, fixtures, calibrations, tables, racks, trolleys, tools, etc.
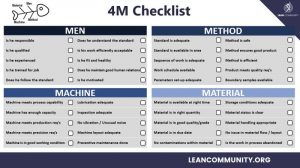
4M Checklist
Benefits of Using the Checklist
- Problem-Solving: By categorizing potential problem areas, it becomes easier to systematically analyze and address issues.
- Process Improvement: Helps in identifying inefficiencies and areas for improvement in the process.
- Quality Control: Enhances the ability to maintain consistent quality by identifying and mitigating variables that could affect the output.
- Risk Management: Proactively identifies areas where risks could emerge, allowing for preemptive action.
Conclusion
The 4M checklist is a testament to the timeless principles of thoroughness, systematic analysis, and continuous improvement in business operations. In a rapidly evolving corporate landscape, the relevance of this checklist transcends its initial quality management application, permeating various aspects of organizational strategy and operational excellence.
- Adaptability to Diverse Sectors: The universality of the 4M framework allows it to be adapted across diverse industries, from manufacturing to services, healthcare to information technology.
- Promoting a Holistic View: The framework encourages managers and teams to look beyond the surface-level symptoms of problems, urging a more holistic examination of underlying causes.
- Facilitating Collaborative Problem-Solving: The 4M checklist fosters a culture of collaborative problem-solving.
- Educational and Training Utility: The checklist serves as an excellent educational tool, grounding employees in the fundamentals of systematic analysis and quality management.
- Aligning with Modern Technologies and Data Analytics: In an age dominated by big data and advanced analytics, the 4M checklist provides a structured framework for data interpretation.
The 4M checklist, a cornerstone of quality management and process analysis, continues to hold significant relevance in today’s complex business environment. Its ability to adapt, drive collaboration, foster continuous improvement, and integrate with modern technologies underscores its enduring value. As businesses navigate the challenges of the 21st century, the principles embedded in the 4M checklist remain as crucial as ever, guiding organizations toward operational excellence and sustained success.
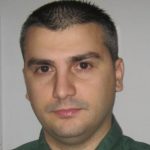
Nenad Marcetic is CIO at Lean Community. He has over 15 years of experience in Lean Management. He is a graduate of Quality Management. He has conducted more than 250 management system audits in various companies and industries (manufacturing, food and beverage, agriculture, IT services, finance, retail, mining). Since 2015 in a global automotive company, where he is responsible for process standardization and the implementation of the IATF standard.