TWI Program (Training Within Industry) is a widely used system that supports the implementation of work standardization in enterprises around the world. The most common is the TWI Job Instruction (TWI JI) method that aids effective on-the-job training. The TWI JI method is the answer to the current problems concerning employee turnover, which are encountered by many companies. Unfortunately, attempts to implement the TWI JI method fail in most companies. Our experience from over 250 manufacturing and service companies that have tried to implement the TWI IP method shows that as many as 92% of them were unable to build a sustainable management system of on-the-job trainings. Of course, the vast majority of these companies have improved their existing systems, but not many were able to fully implement this method as part of their system.
Table of Contents
ToggleWork standardization according to TWI Program
Work standardization is not about posting standards next to workstations, but about providing employees with the best known method of performing activities. This is the basic idea of the TWI program, where the key is employee training based on previously prepared documents that divide work into important steps, key points and the reasons for the key points (Fig. 1)
Fig. 1. TWI Instruction – tying the underwriter’s knot
Source: own work
The TWI Program JI training is based on a 4-step method that works on the basis of the PDCA cycle (Table 1).
Source: Training Within Industry Materials, 1945, War Manpower Commission, Bureau of Training, Training Within Industry Service
Steps of TWI JI methodology | Key points for steps |
1. Prepare the learner |
|
2. Present the operation |
|
3. Try out performance |
|
4. Follow up |
|
The purpose of this method is to standardize the process of on-the-job training carried out by a TWI Instructor (leader or experienced operator). However, TWI instructions standardize the way of working on a given workstation.
The challenge facing the TWI JI method involves the setting of measurable implementation goals – Key Performance Indicators. At first glance, the TWI JI method is a “soft” issue related to employee development. Usually, the companies when implementing the TWI JI method results in making an assumption that is similar to other “soft” methods: let’s train our employees and they will change their attitude. However, the TWI JI method is also a way of standardizing work, which can certainly be referred to the group of “hard” Lean methods. It is therefore a mix of improving employees’ competences and stabilizing production processes, and this causes problems when design the indicators of the method. In addition, the TWI JI method is oriented towards eliminating the root causes of problems in the areas of quality, efficiency or employee turnover, which is why it is difficult to filter out data that shows the actual impact of the methodology on the measured indicators. We present below a set of guidelines that, depending on the chosen vision for the TWI JI method, will help in setting and tracking goals. These guidelines are based on our 12 years of experience in implementing TWI in over 250 companies on 4 continents.
Vision versus goals
Vision is the starting point for the implementation of the TWI JI method. It defines our view on the potential benefits of the methodology. Vision should be based on the organization’s needs that result from long-term goals. Table 2 shows examples of how vision matches the goals and the set KPIs.
Table2. Vision, goals and measures when implementing the TWI method of instructing employees
Source: own work
Vision for implementing the TWI Program JI method | Implementation goal | Example of a KPI measure |
The employees are polyvalent and can work on several operations | Frequent employee turnover between operations (employee polyvalence) | 70% of direct production employees trained on the basis of the TWI JI method on at least 3 production operations by the end of 2020 |
New employees achieve full efficiency of work in the assumed and standardized time | A constant and standardized time of achieving the assumed work efficiency by a new employee | 16 production hours (after TWI instruction) to achieve 85% efficiency in riveting operations |
All production stations have the best possible working method defined | Standardizing production operations using the TWI Instruction | 50% of production operations standardized on the basis of TWI Instructions until the end of 2020 |
Middle-level managers are true leaders – they can teach employees | The number of leaders and managers certified as TWI instructors | 100% of leaders and managers certified as TWI instructors by the end of 2020 |
New projects launched in an effective way | All new projects covered by work standardization according to TWI | 100% of new projects have TWI instructions prepared 60 days before SOP (Start Of Production) At least 2 TWI Instructors certified on one shift 20 days before SOP (Start Of Production) |
Every year we improve work productivity | Improving employee productivity in the existing production area covered by TWI | An increase in productivity inan area by 8% after the implementation of TWI |
Every year we reduce the amount of production scrap | Reduction of scrap in the existing production area covered by TWI | Reduction of scrap in the specific area by 20% after the implementation of TWI |
Summary
The problem with the implementation of the TWI JI method is often associated with the lack of specific implementation goals, although the root cause is the difficulty in determining and measuring them. Unfortunately, without defining the objectives, the implementation and maintenance of system work standardization according to TWI program will probably end in failure. The goals presented above are successfully used in enterprises. The characteristics of the described goals enable their parallel application, because they are not mutually exclusive, but on the contrary – they are complementary. All this means that clearly defined goals and their clear communication to employees lead to the success of the TWI program in enterprises. The basis of the TWI program are people, and standardization of work concerns the way employees perform their duties – not only with regards to production, but also to transferring knowledge and skills.
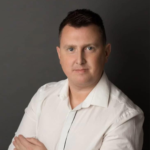
Dr. Bartosz Misiurek is a co-founder of a few start-ups like Leantrix, Lean Community, Leancoin, etwi, Lean Global Consulting, Sallar. He is a CEO at LeanTrix Ltd., Leancoin Ltd, Do Lean IT OU, and a Member of the Board at Astral Hodling OU. Author of the book “Standardized Work with TWI: Eliminating Human Errors in Production and Service Processes.” He works as Sr Manager and TWI Global Coach at Automotive Company.
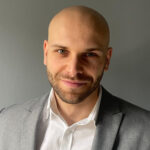
He is a Senior Consultant of the TWI program and Lean Management at LeanTrix. He is also a leader in the startup project - etwi system. He was a member of a global team that implemented the TPM system for several automotive plants in Europe, Asia, South America and North America.