MTBF, MTTR, and MTTF are TPM indicators. The TPM (Total Productive Maintenance) system is now widely implemented in manufacturing companies. Measuring the effectiveness of the implementation of this system is usually carried out by the following Key Performance Indicators: OEE, MTBF, MTTR, and MTTF. It is difficult to identify a production company that implements the lean management philosophy without a TPM system. The purpose of TPM is the improve the efficiency of the use of a machine park by reducing the so-called Six Big Losses:
- Failures
- Too long changeover times
- Microdowntime in machine operation
- Reduced speed of work
- Qualitative deficiencies
- Reduced performance during machine start-up
The TPM system uses several indicators that support the measuring of progress in the area of improving machine utilization. Among them are the MTTF, MTBF, and MTTR indicators.
Table of Contents
ToggleWhat are the MTTF, MTBF, and MTTR indicators?
Everyone will surely agree that OEE (Overall Equipment Efficiency) is the most frequently used indicator when implementing TPM in any company. The OEE indicator allows the six big losses in machine operation to be assigned to 3 areas: availability, use, and the quality of products that were manufactured on it. Therefore, the OEE indicator measures the efficiency of machine use. Conclusions resulting from the analysis of the OEE indicator are useful for the Production and Maintenance departments. From the point of view of TPM, the key loss in the efficiency of machines is their failures. Their reduction has an impact on the improvement of the availability of machines. The OEE indicator has many applications. It allows, among other things, for the indication of what part of all losses in a machine’s operation are failures. However, this indicator does not analyze the failures themselves in detail. This is the purpose of the three other key indicators, which are associated mainly with the Maintenance departments:
- MTTR –Mean time to repair
- MTTF –Mean time to failure
- MTBF –Mean time between failures
Measuring them, reviewing their trends, and drawing conclusions from them is crucial to minimize downtime and thus improve machine availability.
How to calculate the MTTF, MTBF, and MTTR indicators?
If your company counts OEE, you have all the data to calculate the MTTR, MTTF, and MTBF indicators. Yes, this is because you need the following information to calculate them:
- Available production time (decreased by scheduled interruptions)
- Failure time (downtime)
- Number of remedial events
Available production time is one of the three factors that contribute to the OEE indicator. Failure time is the data that is necessary to calculate availability. The number of remedial events is the data collected by all Maintenance Departments, as it is necessary to calculate the failure time. So how should the MTTF, MTBF, and MTTR indicators be calculated?
- MTTR = failure time/number of remedial events [min]
- MTTF = (available working time – failure time)/number of events [min]
- MTBF = MTTR + MTTF [min]
The analysis of the MTTF, MTBF, and MTTR indicators works best when their trends are followed in the subsequent days/weeks/months. It then becomes apparent whether the TPM activities are bringing the intended results. The key challenge is how deeply the MTTF, MTBF, and MTTR indicators should be analyzed in a company. Do you analyze all machines throughout the entire plant? Do you focus on a selected machine? Or maybe you should choose specific parts or tools on the machine? The answer to all these questions is: YES. The MTTF, MTBF, and MTTR indicators should be tracked for the entire factory (to track the efficiency of Maintenance services), and also for the selected parts of a specific machine (to know when to preventively inspect or replace this part). To effectively select the machines that should be analyzed in detail in terms of measuring the MTTF, MTBF, and MTTR indicators, an approach called Lean Maintenance should be used. This approach identifies priority machines in the process by analyzing their:
- Impact on the production system
- Position in the value stream
- Impact on customers
When a given machine is selected as a priority machine, it is necessary to analyze the failure frequency of its parts (tools, equipment), whilst taking into account:
- The effect of failure of the machine’s parts on the machine’s performance
- The predictability of the occurrence of failure of a given part
- The frequency of the occurrence of failure of a given part
In this way, priority machines can be designated, and on them key parts (tools and equipment) can be specified. This is essential inorder to effectively designate those parts that should be measured by the MTTF, MTBF and MTTR indicators.
Why calculate and measure the MTTF, MTBF, and MTTR indicators?
To schedule the time of inspections or preventive replacements of key parts on priority machines
When key parts are designated on priority machines, a preventative replacement time of a given part can be assumed. This time is most often determined by adopting the following principle: preventive replacement of parts every 85% of MTBF. If the mean time between failures for a part is, e.g. 1000 minutes, then its preventive replacement should take place after 850 minutes. The assumed 85% of MTBF is a generally accepted rule that can be adapted to the needs of each company. However, such preventive replacements must take place on key parts of the machine.
This can be compared to replacing a light bulb in a lamp. At home, a bulb is replaced when it fails –when it burns out. This is a non-essential part, the failure of which does not have a major impact on our lives. We have many other lamps at home and we can replace the bulb after a longer time. In a surgery room in a hospital, a bulb failure can have a huge impact on the quality of surgery. In such a situation, preventive replacement may take place every 85% of MTBF. This means that the bulb is replaced while it is still working! However, the lamp in the surgery room is a priority device and there should never be a situation in which part of it has no light. That is why it is so important before measuring the MTTF, MTBF, and MTTR indicators to prioritize machines and then identify their key parts.
To check the effectiveness of the maintenance services in the plant
Yes, the MTTF, MTBF, and MTTR indicators are excellent KPIs (Key Performance Indicators) for the Maintenance Department – the MTTR indicator in particular. When using the MTTF, MTBF, and MTTR indicators as KPIs for the Maintenance Department, you should first track them about the entire factory (all machines and devices) to capture the general trend. A good trend is when, e.g. the MTTR indicators are decreasing. This means that the average time of removing failure is getting shorter and shorter.
To measure progress in the reduction of breakdown times at the plant
An article concerning the mapping of the failure removal process was published in one of the earlier issues of MS. Mapping the process of removing failure helps to analyze this process and to separate operations that add value from those that are wasteful. Practice shows that over 50% of actions taken in the process of removing failures are wasted! These include. the operator’s attempt to find a mechanic, mechanics looking for parts, the lack of tools and materials, and many others. These are common organizational problems. The longer the time of removing failures, the lower the availability of the machine. Analysis of the failure removal process, and looking for improvement solutions in terms of improving the organization of this process, translate into a reduction of the MTTR indicator.
To measure progress in the implementation of Autonomous Maintenance activities
Autonomous Maintenance (AM) is one of the pillars of the TPM system. Most production plants begin their adventure with TPM with the implementation of AM. And rightly so! Thanks to AM, the awareness of operators in the technical area increases. Operators begin to care for their machine as if it were their private car. They begin to spot faults before they turn into failures. Thanks to AM, the value of the MTBF indicator is improving – simply, breakdowns occur less frequently because their causes (defects) are removed before they turn into a serious problem on the machine.
OEE Indicator within TPM
The OEE (Overall Equipment Effectiveness) indicator stands as a pivotal metric in the landscape of Total Productive Maintenance (TPM), serving as a comprehensive gauge of manufacturing efficiency. As TPM systems gain widespread adoption across production companies, the importance of accurately measuring and interpreting the OEE indicator cannot be overstated. This chapter delves into the intricacies of the OEE indicator, its calculation, implications, and its synergistic role alongside MTBF, MTTR, and MTTF within the TPM framework.
The Essence of OEE
At its core, the OEE indicator encapsulates the effectiveness of machinery in the production process, breaking down the analysis into three critical areas: availability, performance, and quality. By offering a granular view into how effectively equipment is utilized, OEE not only highlights the potential for improvement in machine operation but also serves as a linchpin for informed decision-making in both the Production and Maintenance departments.
Calculation of OEE
Calculating OEE necessitates a holistic approach, considering factors that contribute to equipment inefficiencies:
- Availability takes into account the planned production time versus downtime, offering insights into machine reliability.
- Performance assesses whether the machinery operates at its optimal speed, taking into consideration the impacts of minor stoppages and slow cycles.
- Quality measures the rate of good parts produced as opposed to the total output, highlighting the equipment’s effectiveness in maintaining production standards.
The formula for OEE is thus a product of these three factors, represented as:
OEE=(Actual Output / Maximum Capacity)×(Operating Time / Planned Production Time)×(Quality Products / Total Products Produced)
OEE=(Maximum Capacity/Actual Output)×(Planned Production Time / Operating Time)×(Total Products Produced / Quality Products)
Strategic Implementation of OEE
Understanding OEE within the context of TPM is pivotal for identifying and mitigating the Six Big Losses that directly impact manufacturing efficiency. By categorizing losses into availability, performance, and quality, OEE provides a structured approach to enhance machine utilization. The strategic implementation of OEE involves:
- Detailed Analysis and Benchmarking: Leveraging OEE to pinpoint specific areas of improvement, setting realistic benchmarks for progress.
- Cross-Departmental Collaboration: Facilitating a collaborative environment between Production and Maintenance teams to address inefficiencies identified through OEE metrics.
- Continuous Improvement: Employing OEE as a continuous monitoring tool to guide the TPM initiatives, fostering a culture of perpetual enhancement and lean management.
OEE in Action: A Case Study
To illustrate the impact of OEE, consider a manufacturing plant that implemented TPM to address frequent downtime and quality issues. By analyzing OEE, the company identified that the primary cause of downtime was equipment failures (affecting availability), and the main quality issue was product defects (impacting the quality metric). Through targeted maintenance strategies and quality improvement processes, the company was able to significantly reduce downtime and improve product quality, thereby increasing the OEE score from 65% to 85% over a year. This improvement not only enhanced production efficiency but also resulted in cost savings and increased customer satisfaction.
Summary: MTTF, MTBF, and MTTR
Measuring the MTTF, MTBF, and MTTR indicators is not just for seeing the overall trends in the operation of the maintenance services in the plant. Thanks to these indicators, the preventive maintenance and replacements of parts on priority machines can be planned. They also provide an opportunity to analyze the effectiveness of the implementation of actions related to the reduction of failure removal time. They are an excellent measure of the implementation of Autonomous Maintenance activities, which are the basis for implementing a TPM system. These indicators are closely related to the analysis of the failure rate, and therefore they are a great support for Maintenance Departments in production plants. It is worth using these indicators, not only to measure them but also to draw conclusions and implement actions that aim to reduce the failure rate of machines and shorten the time of removing failures. All this will translate into an increased availability of machines and the improvement of the OEE indicator.
Buy the article in PDF version on Lean Global Marketplace
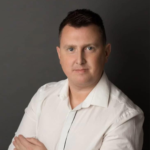
Dr. Bartosz Misiurek is a co-founder of a few start-ups like Leantrix, Lean Community, Leancoin, etwi, Lean Global Consulting, Sallar. He is a CEO at LeanTrix Ltd., Leancoin Ltd, Do Lean IT OU, and a Member of the Board at Astral Hodling OU. Author of the book “Standardized Work with TWI: Eliminating Human Errors in Production and Service Processes.” He works as Sr Manager and TWI Global Coach at Automotive Company.