Human Resource Management and Lean HR. Lean philosophy is the key to a company’s success. Its implementation requires the involvement of all employees in the enterprise – from an operator to the CEO of the company. It is a difficult challenge because it is associated with building awareness at every level of the organization. How can we arouse the employees’ willingness to change? How can we make them want to use Lean tools and methods? How can we manage their competencies in Lean? Learn to develop people, and in return, they will improve your company’s competitiveness!
Table of Contents
ToggleWhat is Lean Management
The Lean Management philosophy is currently the most popular approach to enterprise management in the world. The term Lean was used for the first time in the early 1990s. The Toyota Production System (TPS) was then described as Lean Manufacturing. TPS is recognized as the world’s leading enterprise management system. To this day, it is a model that many companies strive to achieve – not only in the production sector but also in the service sector. This is not without reason – when applying Lean philosophy you can gain many benefits related to:
- improvement of quality,
- cost minimization,
- minimization of lead time,
- improvement of safety,
- improvement of work ergonomics
Lean is a management philosophy in which the key is the maximum use of currently available resources and the elimination of all the waste (Japanese: Muda) from processes. The effective application of Lean requires the implementation of individual methods and tools that belong to this philosophy. The choice of individual methods depends on the problems that are faced by a given organization. For example, when a company has problems with the delayed execution of sales orders, it is appropriate to use A3 Reports as a problem-solving method. In turn, if a manufacturing company has a problem with machine changeover times that are too long, it will be helpful to implement the SMED (Single-Minute Exchange of Die) method, which aims to shorten this time. The strength of the Lean philosophy lies in the fact that it has a prepared answer for every problem of the organization in the form of methods and tools, which together create the company’s management system. The biggest challenge when implementing Lean philosophy is the commitment of all the employees in the company to act according to it. Without this, successful implementation will simply not happen. The richest man in human history, John Davison Rockefeller, once said – “Knowing how to deal with people is as much a commercial commodity as sugar or coffee. And I will pay more for this skill than for any other skill in the world.” This skill is related to engaging and motivating employees, which is further strengthened by building their awareness.
What is Awareness in Human Resource Management?
Awareness is the optimal state of arousal of the central nervous system, in which the nervous and learning processes retain their creative character. This definition is very complicated. In practice, awareness means that a person knows why he is doing something. When you tell a young child not to touch a hot oven, you are not building awareness in him at all. Why? Because the child will anyway go and touch the oven. The child will then find out why this should not be done. People learn through experiences and through understanding the causes. So instead of telling people how to do something, tell them why to do it. When they understand why they should do something, they will come and ask how to do it. This principle works exactly in the case of training employees about tools and methods from the Lean philosophy. When you finish checking training offers and finally send an employee for training in a given method, you want him to learn something new during the training in order for him to use it in his work environment. Unfortunately, this won’t happen. It will fail. During training, people only learn how to do something, and then, due to the lack of time and awareness, they forget the acquired knowledge. Because, unfortunately, training most often ends when you leave the training room, and it is the application of the acquired knowledge in practice under the watchful eye of the trainer that is the key to success. Therefore, before training, a given person should have specified why he or she should go to such training. This can be achieved by stating such a person’s goal, which is based on their needs for the skills that he/she is developing. For example, the goal for an employee may be to reduce the machine setup time from 40 minutes to 30 minutes in a month. When coming to SMED training with such a goal, a given employee will be focused on learning the method that is meant to help him achieve this goal. It seems simple and logical. However, it is not! Our experience of training over 10 thousand people shows that only about 5 percent of them came to the training with a set goal. Nearly half of all the people we trained did not know what it was going to be about, or they only knew what was in the description of the training! In such a situation, building commitment among employees is impossible. Moreover, people are the key to implementing Lean philosophy (see graphic: “People as a key element for the implementation of Lean philosophy”). It is a foundation of Human Resource Management.
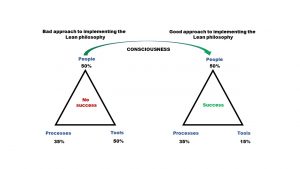
Source: M. Piątkowski, Training recommendations when implementing Lean, 10th Lean Management Conference, Wroclaw 2010.
The correct approach to the implementation of Lean philosophy comes down to engaging people, and not implementing individual tools separately. However, the top management in companies often imposes on their employees the implementation of specific tools and methods (telling them how to do it), and people do not want to use them (they do not know why they should do it). When you focus on building awareness in your employees by setting them clear goals and then justifying them (telling them why it is important), they will choose the appropriate Lean tools and methods that will help them achieve these goals (they will find a solution of how to do it). It is what we call Human Resource Management. Remember that turning tables in this situation is the key to building employee engagement. Never send employees to training when they do not have clear goals. As Napoleon Hill [1] once said: “The goal you set is the foundation of all achievement, big and small. Even a strong man can be defeated by a child who strives for the goal.”
Practice is the key to the conscious use of Lean methods and tools
- Training is an important part of building awareness. Unfortunately, completing the training itself is not associated with the practical ability to use Lean methods and tools. Practice is needed for this. The constant support of a trainer in the process of implementing the acquired knowledge in practice, based on the joint exchange of experiences and audits, becomes the key. Training companies usually certify employees at three levels:
Training completion certificate – a document confirming that the person has learned what a given method is, and is able to take practical actions. - License – specifies that a person has skills in applying specific Lean methods and tools.
- Diploma – certifies that the recipient is able to conduct Lean training and is able to help all employees (Sensei).
In the figure “Certification Levels and the Deming Cycle”, three levels of certification of skills in the application of Lean tools and methods are presented using the Deming Cycle.

Key: the red line shows the moment when it can be concluded that the participants of Lean methodology trainings develop the ability to consciously apply the chosen Lean method. This does not happen until completing the three and four quarters of the circle. Source: Own elaboration.
Certifying and licensing are the areas of practicing the methods. When training companies are asked to conduct training, they are often given, from the top management, the goal of building employee awareness and commitment. This goal is impossible to achieve! People’s awareness is only built from the moment of licensing. After the training, only euphoria and willingness to use Lean methods and tools can arise among people. But awareness comes when we practice something. That is why the Lean philosophy most often dies in companies during the practicing phase. And this is usually because people do not have set goals before training and they do not have a set time frame to achieve these goals. Moreover, contact with their trainer is usually difficult. The hardest moment when engaging employees is practicing. Do not give up at this stage, because all the euphoria after the training will then simply die.
Human Resource Management in the Use of Lean Methods and Tools
Managing employees is the setting of goals for them, and then verifying their achievement. It is similar with competences. It is no coincidence that a thick red line was added in the figure “Certification levels and the Deming cycle”. It separates the 1st and 2nd quarters from the 3rd and 4th quarters. After training, and during the practicing of Lean methods, a person is not yet able to use any method consciously. They just learn how to do it. Obtaining a certificate or diploma means that a given person knows how to consciously apply the chosen Lean method. This division is key in managing employee competencies and planning the best-suited training. A perfect tool to support this process is the skill matrix. The table “Competency matrix for managing skills in the application of Lean methods and tools” presents an example of such matrices in a selected area.
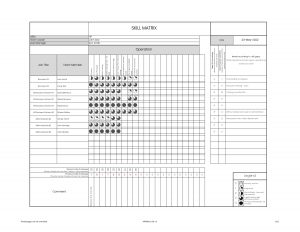
Key: green means that in a certain method an intended goal was achieved, and red means that the goal has not yet been achieved. Source: Misiurek B., Methodology of standardization of autonomous operating processes, which is oriented at improving the efficiency of automated machines, Wroclaw 2014, p. 284.
The competency matrix includes the defined and required competencies in the field of Lean methods, and also the employees who work in a given area. It is a part of the Human Resource Management process. The Deming cycle shows their skills in applying particular methods. It is not required that all the employees know all the methods. What is important in the competency matrix is the determination of the required number of trained employees (goal). For example, the SMED system has a specific goal of six employees who should be able to use this method consciously. Currently, however, one employee – Dominika Adamska, has the skills in this method. Therefore, the target was not achieved in June, and it is thus marked in red.
It is the juxtaposition of the current competencies of employees with the set goal for a given method, which should in turn be the basis for planning employee training. The training goals for each of them are set in a separate column. The deadline for the full achievement of these goals is set for December 2015. It is worth remembering that people’s awareness of the use of Lean tools and methods is only achieved when they become practitioners and trainers (Sensei). As Albert Einstein said: “Any fool can know. It’s essential to understand.”
Golden Rules when Building Human Resource Management
Lean philosophy can certainly not be implemented without employee involvement. Therefore, you should focus on people. Develop them. This is at the heart of the Toyota Production System. You should follow the three golden rules.
The golden rules of engagement when implementing Lean methods:
- Train people in Lean tools and methods – this is the foundation for building commitment.
- Involve employees in the daily practice of Lean methods – this is the basis of building awareness.
- Audit progress at work – this is the key to maintaining change. Remember, however, that auditing is not a control! It is an opportunity to spot problems and improve processes.
The key is managing employee competencies. It is essential to have clear goals for them before training. The selection of the best training companies on the market, which will provide employees with knowledge in a practical way, is also an important aspect. However, the most important thing is to enable the practice of Lean methods and tools in everyday duties at work for the Lean culture to be built into the organization. The guru in management, Peter Drucker, once said: “Give people freedom and the ability to act, and they will surprise you with their ingenuity.” Lean philosophy supports the creativity of employees, and the “only” thing that the company must do is give them time for it.
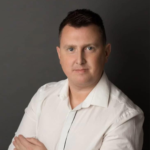
Dr. Bartosz Misiurek is a co-founder of a few start-ups like Leantrix, Lean Community, Leancoin, etwi, Lean Global Consulting, Sallar. He is a CEO at LeanTrix Ltd., Leancoin Ltd, Do Lean IT OU, and a Member of the Board at Astral Hodling OU. Author of the book “Standardized Work with TWI: Eliminating Human Errors in Production and Service Processes.” He works as Sr Manager and TWI Global Coach at Automotive Company.