Layered Process Audit (LPA) is a systematic approach commonly used in industries to ensure quality and consistency in manufacturing processes. However, the principles of LPA can extend beyond the manufacturing floor and find application in our daily lives. In this article, I will explore how the concept of LPA can be adapted and applied to various aspects of our everyday routines, ultimately helping us achieve greater efficiency, reliability, and overall quality in our personal and professional endeavors. I dislike it when I can’t find something at home. I know it should be here, but it’s not! You know how it is; I normally put something down and then can’t find it.
Table of Contents
ToggleExample: Searching for a Nail Clipper
It was the same today when it was time to clip the nails of my daughter’s favorite, a Chihuahua dog. Those who know understand that he doesn’t have big teeth, but rather big nails. And so, the search for the nail clipper began. A drama… all the usual places were checked and nothing. Vanished like a stone in water. Standardization failed. Then, an epiphany! I’ll use others’ strengths. I invited my older daughter to join the search. She found it! Instantly. They were right there, I just didn’t see them.
Layered Process Audit in Everyday Life and Organizational Contexts
How often do we, in our daily activities, fail to notice what we should see right away? How often does an outsider asking a question or pointing something out that we pass by every day lead us to make improvements?” In organizations, it’s important to engage everyone, utilize their skills, and stimulate improvement.
Key Components for Effective LPA Implementation
For seven years, I have been observing, improving, and successfully implementing LPA in the production area. What is important for this process to work effectively in organizations:
- A clearly defined owner – a leader responsible for the implementation of LPA.
- Defining the process: list of questions, a form of the audit, defining the levels of auditors, responsibilities, a form of the plan, areas covered by LPA, form, and frequency of reviews of remarks and actions.
- A quarterly plan.
- Monitoring of the plan and its implementation.
- Defining process indicators and monitoring them: plan and implementation, number of remarks from definitions, number of actions closed on time, number of delayed actions, and number of postponed actions.
The Value of Layered Process Audit
By breaking down complex tasks into manageable steps and regularly evaluating their efficiency, we can identify areas for improvement and enhance our daily activities. Layered Process Audit principles encourage a proactive mindset, fostering personal growth and success.
For instance, in time management, a Layered Process Audit helps us analyze how we spend our time, enabling us to optimize our daily schedules. Moreover, LPA can be adapted to personal goals, guiding us in monitoring progress and staying disciplined.
LPA’s transparency, accountability, and continuous improvement aspects can improve efficiency, productivity, and overall quality in our daily lives, making it a valuable tool for personal and professional development. Don`t forget that LPA should check the process which is standardized and described in the Standard Operating Procedures.
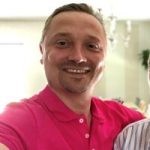
Boguslaw is certified Lean Six Sigma Black Belt. Responsible for implementing Lean Culture in the organizations, starting from 5S program, changes in the Operating System, and growth in Problem Solving Tools. He is a Lean Practitioner with over 20 years of experience in different industries.