The article is about example of SOP (Standard Operating Procedure) for manufacturing processes. These standards serve various purposes such as quality assurance, auditing, and instructional guidance. Taiichi Ohno, renowned as the architect of the Toyota Production System, famously stated that without standards, there can be no Kaizen (continuous improvement). Thus, SOPs are not only about maintaining consistency but are instrumental in enhancing work methods through kaizen initiatives. An effective SOP must be both practical and of high quality to fulfill its roles in instruction, quality assurance, safety, and continuous improvement.
Table of Contents
ToggleThe Intersection of Utility and Quality in SOP
The most effective SOPs are those that exhibit high utility and quality. A matrix, with utility on one axis and quality on the other, helps visualize this concept. Standards in the upper-right quadrant (Area 1) demonstrate both high utility and quality, making them most effective for various applications in the manufacturing process. This article will showcase an example of such an SOP that exemplifies these characteristics.
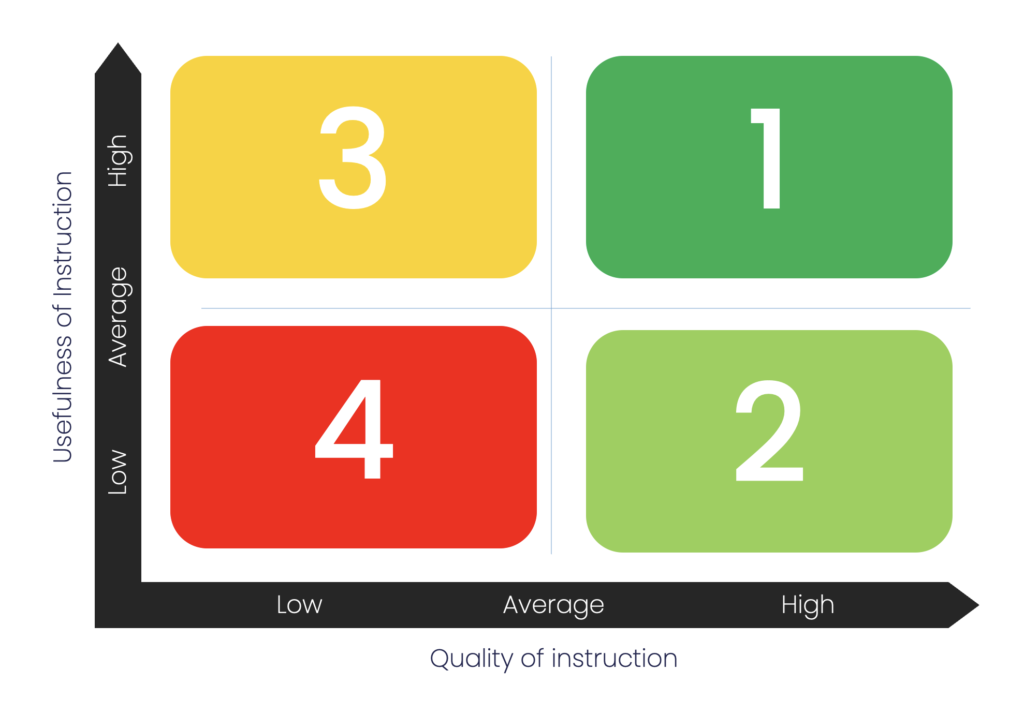
The Intersection of Utility and Quality in SOP
In the matrix presented, the differences between categories are defined by the intersection of ‘Usefulness of Instruction’ and ‘Quality of Instruction’ for Standard Operating Procedures (SOPs):
- Quadrant 1 (Green): High Usefulness and High Quality – SOPs in this quadrant are both highly useful and of high quality. They are considered ideal, effectively guiding users and crafted in a manner that facilitates clear understanding and implementation.
- Quadrant 2 (Light Green): Average Usefulness and High Quality – SOPs here are of high quality in terms of writing but only have average usefulness. They might be well-written but do not fully serve the practical needs of the users or are not as applicable to the processes they aim to standardize.
- Quadrant 3 (Yellow): High Usefulness and Average Quality– These SOPs are very useful in practice but the quality of their writing is average. They fulfill their instructional role but may lack clarity or detail that could enhance their effectiveness.
- Quadrant 4 (Red): Low Usefulness and Low Quality – These are SOPs that perform poorly on both fronts.
SOP Example for Manufacturing Industry
Best practices dictate that an SOP should break down work into three components:
- major steps (what is done),
- key points (how it is done),
- reasons for these key points (why it is done in that specific way).
This “what, how, and why” framework is crucial. Additionally, SOPs should incorporate photographs focusing on key points to illustrate the process, not just the outcome. Symbols categorize key points into areas such as work correctness, impact on quality, safety, and work facilitation. An example SOP in manufacturing, specifically for yying the Underwriter`s Knot, is prepared in the etwi.io system, demonstrating these principles.
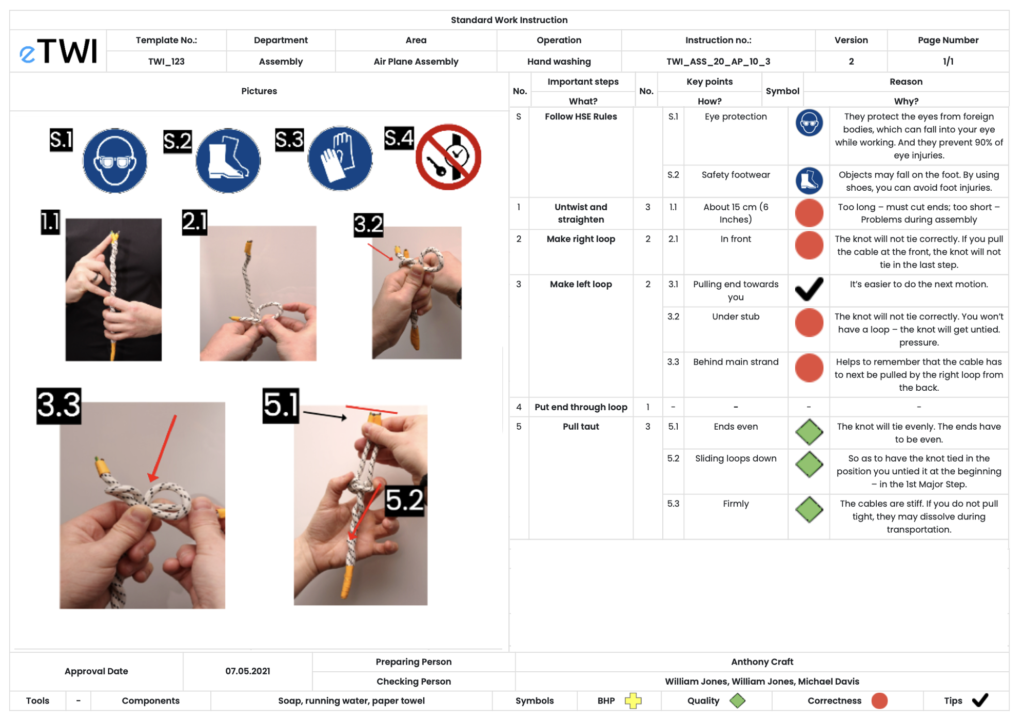
SOP Example Manufacturing – Tying the Underwriter`s Knot
Toyota, a leading automotive manufacturer, employs SOPs that adhere to this structured approach. The company’s standards are based on the “what, how, and why” division, drawing inspiration from the Training Within Industry (TWI) Job Instructions method. This approach focuses on instructing employees by clearly communicating the steps, key points, and reasons for key points, forming the foundation for work standardization at Toyota.
We prepared a ranking for best TWI Job Instruction Certification courses where You can practice working on the SOP Example for Manufacting.
SOP as a Training Tool and Idea Generator
The essence of an SOP lies in its ability to clarify expectations and requirements for workers. In training scenarios, instructors primarily focus on steps and key points, using SOPs as a reference. This method aligns with the TWI Job Instructions technique, ensuring that employees not only follow the standards but also understand and adhere to them. Photographs in SOPs serve as post-training visual aids rather than during the instruction. Additionally, SOP can support in generating ideas through the tool: Poka Yoke Generator Sheet.
SOP and TWI Job Instructions
The TWI (Training Within Industry) Job Instruction method structures on-the-job training to consistently and correctly teach a job. The picture presents the TWI Job Instructions method.
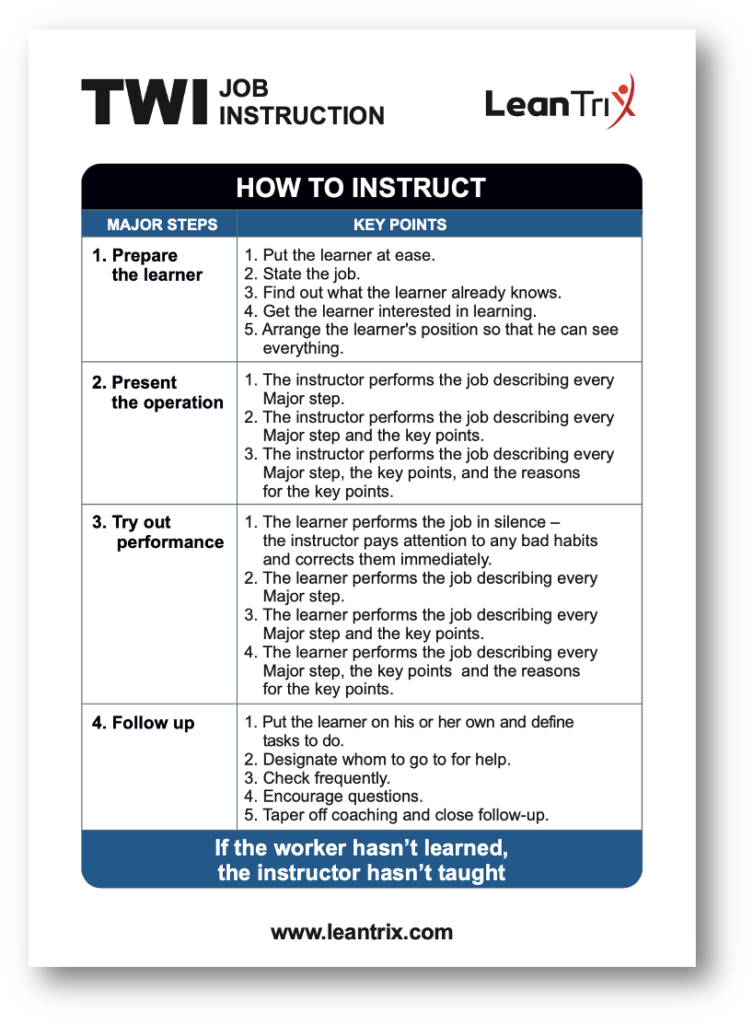
TWI Job Instructions method – picture taken from LeanTrix
Here’s how the method unfolds in a training scenario:
- Prepare the Learner
- Begin by putting the learner at ease to foster a conducive learning environment. State the job at hand clearly, ascertain the learner’s existing knowledge, pique their interest in learning, and position them so they can see all aspects of the job you are performing.
- Present the Operation
- The instructor demonstrates the job, first by describing each major step. Then, they repeat the process, this time detailing both the major steps and the key points, which are the crucial aspects of the job that ensure quality, safety, and productivity. Finally, the instructor demonstrates again, including the reasons for each key point, providing a rationale that helps the learner understand the importance of each key point and action.
- Try Out Performance
- The learner now attempts the job, initially in silence, to internalize the steps and key points. The instructor observes, ready to correct any mistakes immediately. The learner then repeats the process, this time articulating each step, key point, and the reasoning behind them, ensuring they have comprehended the entire operation.
- Follow Up
- Once the learner is performing the job on their own, the instructor sets tasks for them to reinforce the learning, designates resources or individuals they can approach for help, and checks in frequently.
The motto of TWI Job Instructions
The motto of TWI JI philosophy is: “If the worker hasn’t learned, the instructor hasn’t taught.” This emphasizes the responsibility of the instructor in the learning process. This method ensures that each new worker is provided with consistent instructions which are vital for maintaining the standards of quality and efficiency in the workplace.
SOP and Kaizen
SOPs can drive continuous improvement by integrating with the 5W1H approach. This is exemplified in the “Poka Yoke Generator Sheet” from the book “Standardized Work with TWI“, which prompts questions for each key point, sparking brainstorming sessions to refine existing work standards.
The 5W1H method is integral to kaizen, Toyota’s philosophy of continuous improvement. This approach begins by asking “Why?” to understand the necessity of a task, and “What?” to clarify its purpose. These questions aim to identify and remove waste, or muda, such as needless steps like overproduction or unnecessary movement.
Then, the questions “Where?” and “When?” determine the optimal location and timing for a task, ensuring efficiency. “Who?” identifies the right person for the job, considering qualifications and expertise.
Finally, “How?” encourages finding the best way to perform the task. This means looking at the use of materials, tools, and methods to optimize the work process. In this stage, the team considers all ideas, even those requiring investment, because kaizen is about leveraging all available resources to improve operations. This approach not only streamlines processes but also fosters a culture where every employee contributes to problem-solving and process improvement.
Digitalization of SOP for Manufacturing
Digitalization of Standard Operating Procedures is transforming the manufacturing landscape by enhancing efficiency, consistency, and accessibility. Transitioning from paper-based to digital formats allows for real-time updates, improved collaboration, and better data tracking.
Benefits of Digital SOPs:
- Accessibility: Employees can access SOPs anytime and anywhere, ensuring they have the latest information on hand.
- Real-Time Updates: Changes can be made instantly, keeping procedures current and compliant.
- Collaboration: Teams can comment and suggest improvements directly within the SOP, fostering a culture of continuous enhancement.
- Data Analytics: Integration with tracking systems provides valuable insights for decision-making and process optimization.
- Multimedia Integration: Digital SOPs can include videos and diagrams, catering to various learning styles.
To assist manufacturers in this transition, we have prepared a ranking of the top IT solutions for creating effective SOPs. These tools are designed to streamline the process of developing, updating, and managing SOPs, ultimately driving operational excellence in the manufacturing sector.
Conclusion
SOPs in manufacturing are pivotal for ensuring quality, safety, and efficiency. More than just a set of instructions, they are dynamic tools for continuous improvement, aligning with the principles of Kaizen. SOPs are indispensable tools that drive consistency, mitigate risks, and optimize performance. As the landscape of manufacturing grows ever more complex and interconnected, the role of SOPs in fostering a culture of excellence and innovation becomes increasingly significant. They are not just about maintaining the status quo but about challenging it, pushing the boundaries of what is possible, and setting new standards of excellence. In conclusion, SOPs are the lifeblood of a dynamic manufacturing process, essential for quality, safety, efficiency, and the continuous pursuit of excellence that marks a world-class manufacturing operation.
SOP Example Manufacturing – FAQs
FAQ 1: What is a Standard Operating Procedure (SOP) in manufacturing?
Answer: A Standard Operating Procedure (SOP) in manufacturing is a set of written instructions that outlines the steps necessary to perform a specific task or process. SOPs ensure consistency, quality assurance, safety, and serve as instructional guidance for employees.
FAQ 2: Why are SOPs important in the manufacturing process?
Answer: SOPs are crucial in manufacturing as they help maintain quality and safety standards, provide clear instructions for employees, facilitate training, and promote continuous improvement initiatives, such as Kaizen. They ensure that tasks are performed correctly and consistently.
FAQ 3: How should an effective SOP be structured?
Answer: An effective SOP should be structured around the “what, how, and why” framework. It should outline the major steps of the task, detail key points that ensure quality and safety, and explain the reasons behind these key points. Visual aids, such as photographs and symbols, can enhance understanding.
FAQ 4: What role do SOPs play in training and development?
Answer: SOPs serve as essential training tools by providing a clear reference for instructors and learners. They outline the steps, key points, and rationale, ensuring that new employees understand not only how to perform tasks but also why certain methods are used, thus reinforcing effective practices.
FAQ 5: How can SOPs contribute to continuous improvement?
Answer: SOPs can drive continuous improvement by integrating methodologies like 5W1H and Poka Yoke. These approaches encourage questioning and refining existing processes, helping to identify waste and optimize efficiency. By fostering a culture of improvement, SOPs empower employees to contribute to process enhancements.
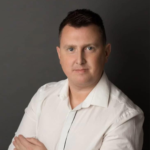
Dr. Bartosz Misiurek is a co-founder of a few start-ups like Leantrix, Lean Community, Leancoin, etwi, Lean Global Consulting, Sallar. He is a CEO at LeanTrix Ltd., Leancoin Ltd, Do Lean IT OU, and a Member of the Board at Astral Hodling OU. Author of the book “Standardized Work with TWI: Eliminating Human Errors in Production and Service Processes.” He works as Sr Manager and TWI Global Coach at Automotive Company.