Profitable idea implementation. Every idea generated in the kaizen approach is good, but not every one of them can be implemented. Two criteria help us decide if an idea is a target solution:
- Its difficulty with respect to costs, time, and material availability;
- Implementation effects as related to the company’s possible benefits in profit, quality improvement, accident reduction, and efficiency increase.
The best ideas give high implementation effects and pose minor difficulty in implementation. A great tool for categorizing the ideas generated is a profitability matrix based on a Cost-Benefit Analysis – CBA. An example of a matrix is presented below.
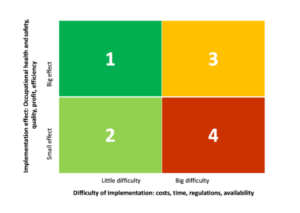
Pic.1
The figures on the matrix reflect groups of ideas. The most desirable ones belong to group no. 1, the least desirable to group no. 4.
Table of Contents
ToggleGroup no. 1. Ideas to implement ASAP – preferably the same day
Ideas in this group bring large benefits and don’t require much implementation effort. They are oriented mostly towards the improvement of: efficiency, quality, or safety. Visual control is often used here. Why is it so effective and profitable? People are visual types. 83% of the information from our surroundings is absorbed by sight. Visual control takes advantage of the most commonly used way of reading surroundings. Moreover, visual control-related solutions are easy to implement, e.g., marking ranges on a manometer. Table below presents the standard for pressure control on a manometer without visual control.
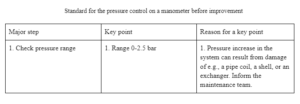
Pic.2
When improving the job by means of the Kaizen and answering the question: how to check the pressure on a manometer instead of learning the range by heart? the idea came out to mark the proper range in green. Therefore, the operator doesn’t have to memorize the correct range, and his job is easier. The idea gives large benefits and doesn’t require any implementation effort at all. The new standard, presented in a table below, still includes one key point.
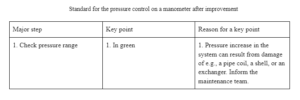
Pic.3
Now, checking the pressure range is lot easier. It’s enough to see if a measurement is in the green field. However, the reason for the key point stays the same; it’s still essential for an operator to be aware of what can lead to an increase or decrease in pressure.
Group no. 2. Ideas without great benefits resulting from the worker’s involvement
This group of ideas is very important, although it’s often neglected by senior management. It covers easily implementable ideas which do not provide huge benefits, e.g., in terms of efficiency, quality, or safety. They concern mostly work improvements and are the effect of problems perceived by workers – inconveniences they often get used to. One example is the idea of moving an intermediate storage area closer to a machine operating in an automatic mode in order to put away products easier. This solution doesn’t affect the work stand efficiency because the machine will still produce a given number of items. However, it will make the operator’s work easier. It means less walking on his shift. I encourage you to promote such ideas. Although they don’t give a company essential benefits, they encourage operators to look for improvements. It is likely that a group-2 improvement will inspire somebody to make up a group-1 improvement.
Group no. 3. Ideas requiring thorough analysis
Ideas belonging to this group need thorough analysis. They can’t be implemented overnight. They are often good ideas requiring a lot of implementation effort. They are related mostly to flow kaizen. Such ideas can be hard to sell to supervisors. The good examples are various technical solutions, such as tools or handles.
Group no. 4. Ideas not suitable for implementation
Believe me, these ideas are also important! Sometimes an unrealistic idea, made up on the spot, can inspire somebody to think of something similar but more workable. That’s how the synergy effect works! I had a situation like this once at a Kaizen workshop. The operation in questions was about taking an element A with the left hand, and an element B with the right hand. Then, both elements had to be put together in a way so that element A was put on element B. A lot of ideas were generated in the brainstorming session to answer the question: how to do it best? The majority of ideas were connected with visual control, instructions, etc. And then one person made up a group-4 idea: Let’s hire a person with a shorter left arm. Then he/she won’t make an error. Their left hand with element A will be always before the right hand holding element B. When the roars of laughter died out, another participant stood up and said: Let’s move the feeder with element A closer to the operator. This way we’ll simulate a shorter left arm. This idea was perfect. You couldn’t make a mistake here. This example shows that a group-4 idea can be an inspiration for a group-1 idea. Therefore, it’s so important to collect all ideas in the second step of the method.
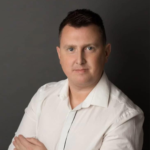
Dr. Bartosz Misiurek is a co-founder of a few start-ups like Leantrix, Lean Community, Leancoin, etwi, Lean Global Consulting, Sallar. He is a CEO at LeanTrix Ltd., Leancoin Ltd, Do Lean IT OU, and a Member of the Board at Astral Hodling OU. Author of the book “Standardized Work with TWI: Eliminating Human Errors in Production and Service Processes.” He works as Sr Manager and TWI Global Coach at Automotive Company.