Enhancing Construction Safety with 6S. Workplace organization has a major impact on the level of safety of employees. It is widely believed that the improvement of work organization is driven by companies from the manufacturing industry that commonly use the methods and tools of the Lean Management philosophy. This philosophy is currently the most popular approach to the management and organization of manufacturing processes in the world (Yogesh, Chandra, Mohan and Arrak 2012). The term “Lean Management” was used for the first time by Womack, Jones and Roos (1990). The authors described the Toyota Production System using Lean Management, which is recognized as the world’s leading production system and to date has been the benchmark for many manufacturing companies (Moore 2004). In Lean Management philosophy, the main tool that is used to improve the quality of a workplace, and therefore creating the basis for its improvement, is the 5S system (Spear 2005). It is recognized in manufacturing companies as a primary tool of Lean Management and is often first implemented. The name of the 5S system is derived from the following successive steps (Hirano 1995):
- 1.S – Sorting (Jap. Seiri),
- 2.S – Systematics (Jap. Seiton),
- 3.S – Shine (Jap. Seiso),
- 4.S – Standardization (Jap. Seiketsu),
- 5.S – Self-discipline (Jap. Shitsuke).
The 5S system has been practiced in industry for several decades. Its usage improves the quality of a workplace, and this affects (Hirano 1995; Rubin 1996; Koenigsaecker 2009; Oppenhaim and Fellbur 2015):
- the improvement of occupational safety,
- the improvement of the ergonomics of work,
- the raising of job standards,
- the increase in satisfaction from work,
- the improvement of employee productivity,
- better flow of information and materials.
Due to the fact that for most manufacturing companies occupational safety is a priority, the term “6S system” has been used in the manufacturing industry for some time. The sixth “S” step in this approach is Safety. Oppenheim and Felbur (2015) highlight that the 5S system was naturally replaced by the 6S system, which puts a greater emphasis on occupational safety. Harris and Harris (2007) state that the 6S system works more comprehensively than the 5S system because it draws attention to the need to ensure occupational safety, without which it is difficult to talk about achieving optimum work efficiency. Similarly, Badiru (2014) states that the 6S system not only improves quality and productivity, but also occupational safety. In turn, Koenigsaecker (2009) in his publication uses the term “5S/6S system” and indicates the essence of occupational safety as a complement to the standard approach in the 5S system. Grant and Cheng (2016) note that an approach called 6S is nowadays used more and more. They provide a number of tips on how to implement the 5S system. In the case of the “S-Safety” step, their instructions turn mainly to the statement that a safe working environment should be kept. Based on the literature survey, it can be assumed that the 5S system will be gradually replaced by the 6S system, as the 6S system is much more complex. While the literature survey indicates a more and more frequent use of the 6S system instead of the 5S system, there is no clear path to follow which would answer the question of how to provide the extra “S-Safety” step.
1. Literature survey on the use of the 5S system in the area of the construction industry
It is commonly believed that the optimization and organization of work in the manufacturing industry is more advanced than in the area of the construction industry. This is proved by the number of publications devoted to the implementation of the Lean Management philosophy, which is much greater in the case of the manufacturing industry. An extensive literature survey carried out by Aziz and Hafez (2013) shows that there is a much smaller share of waste in production processes than in construction processes. Figure 1 illustrates a
summary of the share of waste in these two industries. As stated by the authors, this is a result of manufacturing companies using methods and tools aimed at improving the organization of work, mainly including the Lean Management philosophy.
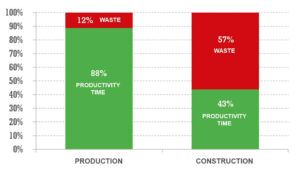
Fig. 1. The share of waste in production processes and construction processes Source: Aziz and Hafez 2013
One of the reasons why Lean Management philosophy is more commonly used in manufacturing processes than in construction processes is its origin. It derives directly from the manufacturing industry, and specifically from the automotive industry. This does not mean that Lean Management tools and methods are not used in non-productive areas. Womack and Jones (2003) emphasize that Lean Management philosophy is universal enough to be used wherever there are people who carry out operations in processes. There are no objections to also using it in the field of construction. The essence of using the 5S system in the construction industry is indicated by Rowlinson (2004), who believes that “5S is the mother of safety”. He emphasizes that within the framework of improving safety, construction companies should use, among others, visual control, the tracking of results in the area of hazards that are potentially accidental, or the marking of dangerous places. However, he does not treat occupational safety as part of the 5S system. He points out that in the area of the construction industry there should be a greater emphasis on occupational safety. He also states that the 5S system is not as widely used in the construction industry as it is in the manufacturing industry. Similarly Salem, Solomon, Genaidy and Luegring (2005) and also Abdelhamid and Salem (2005) state that there is a concept of Lean Construction that describes the use of Lean Management in the area of the construction industry. However, it is not widely used. The authors point out that the basic Lean Management tools, such as the 5S system, are not used by construction companies as much as by manufacturing companies. Aziz and Hafez (2013) in their publication demonstrate that the tools and methods of Lean Management can be applied in construction processes while delivering measurable benefits. According to the authors, every construction company that starts their Lean journey should use, among others, the 5S system in the early stages, which improves quality and occupational safety. The current research of Oakland and Marossy (2017) shows that in recent years many case studies on the implementation of the 5S system in the area of the construction industry have been developed. The results achieved by the construction companies are characterized, among others, by improved occupational safety. This proves that the 5S system is a universal tool for improving the quality of a workplace and is used more and more often in the construction industry. However, literature studies have not shown that any of the authors suggested using the 6S approach in the area of the construction industry. The reason for this is probably due to this approach being a new element in the development of the 5S system, which is used at this moment exclusively in the production area. The next chapter will provide guidelines for the implementation of 6.S – Safety as a complement to the implementation of the 5S system in the construction industry.
2. The 6S system in the construction industry – methodology of operation
The use of the 6S system has one main objective: to improve the quality of a workplace and the safety of the employees working there. The 5S system is primarily orientated towards improving the quality of a workplace, which of course can also contribute to improved safety. Adding the “S-Safety” step to the 5S system is more about recognizing the importance of occupational safety and emphasizing its essence (Fig. 2).
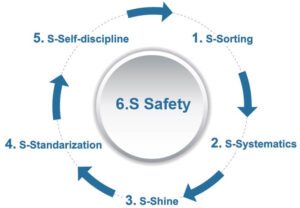
Fig. 2. The role of 6.S – Safety in the 5S system Source: Own work
When creating the 6S system, it is crucial to allocate a serial number to the “S-Safety” step. Occupational safety should be recorded as 0.S – the foundation and starting point before taking any actions to improve the quality of organization in a workplace. This makes it possible to use the 6S system, which consists of the 0.S-Safety step and the 5 remaining steps of the traditional 5S system. As demonstrated in the introduction, there are many publications describing how to implement the subsequent steps of the 5S system. The scheme of action is presented in Table 1. However, the problem is that in publications on the use of the 6S system in manufacturing processes, and thus in the construction industry, there is no indication on how the “S-Safety” step should be implemented. The “S-Safety” step most often comes down to two elements (Badir 2014; Harris and Harris 2007):
- passwords informing that one should work safely,
- orders demanding the use of personal protective equipment.
These two points are definitely important and should be promoted. However, they are related to reactive rather than preventive action. As shown by Heinrich (1959) and also Balestracci and Barlow (1996), an assurance of occupational safety must be carried out in a preventive way and be associated with an identification and elimination of hazards before they become accidents. According to the authors, it is essential to first focus on improving processes rather than blaming employees. Therefore, it is important to define how to
implement the “S-Safety” step while creating the 6S system in an organization, and thus in the area of the construction industry. TWI Job Safety (JS) (Dinero 2005, Wrona and Graupp 2006) is a method that focuses on building a safe workplace. This method was created after World War II as a complement to the Training Within Industry (TWI) program. The TWI JS method focuses on identifying hazards before they become accidents. The main advantage of the TWI JS method is that it allows a workplace to be analysed with regards to the identification of potential hazards. When all hazards are listed, improvement analysis should be performed. The next step should be the implementation of preventive actions and the verification of results. Due to this approach to occupational safety, the TWI JS method works preventively. It can become a way to implement the “S – Safety” step when implementing the 6S system in the area of the construction industry. During implementation, the steps described in the 5S system should only be executed after carrying out actions that ensure the creation of a safe workplace. There is then the assurance that a workplace is safe – free from unidentified hazards.
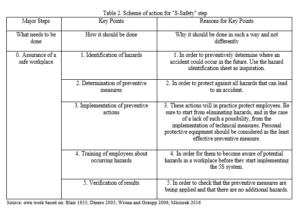
The scheme of action when ensuring occupational safety in the “S-Safety” step of the 6S system is described in detail below.
2.1. Identification of hazards
The first step in the process of ensuring occupational safety in the area of the construction industry is a thorough identification of hazards at the place of their occurrence. The purpose of this stage is to gain knowledge about the current conditions in a workplace. After obtaining a history picture, supervision with regards to the rules and standards of work should be carried out. Every current standard should be strictly verified. It is required to find out if the observed standard of work is actually obeyed by employees. In order to identify hazards, the prepared hazard identification sheet (Table 3) should be used. This sheet should be adapted to the specificity of a process so that it takes into account any existing hazards.
2.2. Determination of preventive measures
The main goal of this step is to match the identified hazards with appropriate preventive measures. The analysis should be conducted with the participation of employees who are familiar with the aspects of their workplace. The effectiveness of the preventive measures was described by Heinrich (1959). Their ranking, starting with the most effective, is presented below:
- elimination of a hazard,
- implementation of technical measures that reduce the chance of an impact of a hazard on an accidental event,
- preparation of visible warnings informing about hazards,
- training of employees about hazards,
- usage of personal protective equipment to protect against hazards.
All of the actions presented by Heinrich (1959) are relevant and should be applied. However, the most effective is the elimination of a hazard. The analysis of the identified hazards should therefore start from the determination of the possibility of eliminating them, and then implementation of technical measures, warnings, staff training and the use of personal protective equipment.
2.3. Implementation of preventive actions
This step can be accomplished through immediate or long-term actions. Immediate actions are those that need to be implemented straight away due to there being a hazard at a workplace that must be controlled. Long-term actions usually require in-depth analysis and are mainly related to financial inputs that should lead to the elimination of hazards or the implementation of technical measures.
2.4. Training of employees about occurring hazards
When developing a new method of working, the training of employees is necessary. For this purpose, the TWI Job Instruction (JI) method is recommended, which is considered to be the most effective method for imparting practical skills (Dniero 2005, Wrona and Graupp 2006: Misiurek 2016, Dooley 2017). It is based on providing knowledge to a learner in clearly divided stages – the major steps. In each major step there are key points that answer the question: how to do the specific major step. The principle in the TWI JI method is (Wrona and Graupp 2006): safety should always be treated as a key point. Each key point must have a reason in which there is an explanation of why the acquired method of working is so important. This approach not only makes an employee work correctly, but first of all consciously – understanding what he does. As Perezgonzalez (2005) states, employee awareness has a huge impact on occupational safety. For this reason, the TWI JI method should be used as a way to educate employees in the area of safe work practices at a workplace, and it is a complement to the implementation of the 6S system.
2.5. Verification of results
This methodological step is related to keeping a safe working environment. Unfortunately, it is often neglected or overlooked in companies, either from the manufacturing industry or from the construction industry. Audits, responding to deviations, constant work with people and engaging employees in cyclical checks of the safety state should never stop. The more hazards, near-miss accidents and incidents are identified and eliminated, the lower the probability of the occurrence of major accidents and unfortunate events will be (Heinrich 1957). Therefore, an important element of keeping the system is to audit the level of safety at a workplace where the 6S system is being implemented. The proposed audit sheet is presented in Table 4. Any non-compliance with the standard should be recorded on the audit sheet and changes should be preferably implemented until the end of an employee’s work on a given day. Such an auditing process is called co-shift auditing (Harris and Rother 2001).

Conclusions
As indicated in the article, the 5S system is one of the most popular approaches to the improvement of work organization at a selected workplace. This method can be used in any process that involves people, including in the area of the construction industry. Safety, which is added to the 5S system, enriches it and not only focuses on improving the quality of a workplace, but also on what is the most important – occupational safety. Therefore, the 6S system is a comprehensive approach for providing a high quality workplace, while maintaining safety as a key and fundamental element. The plan of action within the “S-Safety” step in the 6S system can be presented on the basis of the Plan-Do-Check-Act (PDCA) cycle, which is the basic method of the effective implementation of any task (Shook and Marchwinski 2014). Figure 3 shows the correlation between the PDCA cycle and the method of implementation of the “S-Safety” step in the 6S system.
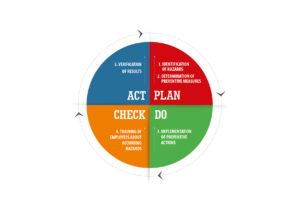
Fig.3. Correlation between the plan of action in the “S-Safety” step and the PDCA cycle Source: Own work
The presented approach can be applied in every area where the 6S system is implemented. It can therefore be successfully used in the construction industry.
References
Abdelhamid T., Salem S., 2005, Lean Construction: A New Paradigm For Managing Construction Projects, Innovations in Materials and Design of Civil Infrastructure, Egypt
Amaro V.A. Jr., 2006, Evolver – A Practitioner’s Guide to Lean Manufacturing – 5S Edition, Lean Manufacturing Consulting, Inc.
Aziz R.F., Hafez S.M., 2013, Applying lean thinking in construction and performance improvement, Alexandria Engineering Journal, vol. 52, p: 679-695
Badiru A.B., 2014, Handbook of Industrial and Systems Engineering, CRC Press, New York
Balestracci, D. Jr.; Barlow, J.L. 1996. Quality Improvement: Practical Applications for Medical Group Practice, Center for Reasearch in Ambulatory Health Care Administration: 25.
Blair C.M., 1955, Training of hourly employees, Plant Management, IEC Production Forum, 47 (12), 79A-80A
Dinero, D. 2005. Training Within Industry: The Foundation Of Lean, Productivity Press: 229, 238, 244-250.
Dooley C.R., 2017, Training Within Industry: Job Instruction, Productivity Press, New York
Fabrizio T., Tapping D., 2006, 5S for the Office: Organizing the Workplace to Eliminate Waste, Productivity Press, New York
Grant V.J., Cheng A., 2016, Comprehensive Healthcare Simulation: Pediatrics, Springer International Publishing, Switzerland
Harris C., Harris R., 2007, Developing a Lean Workforce: A Guide for Human Resources, Plant Managers and Lean Coordinators, Productivity Press, New York
Heinrich. H. W. 1959. Industrial Accidents Prevention, Mc Graw Hill Book Company, Inc.: 7-21.
Hirano H., 1995, 5 Pilars of the Visual Workplace, New York: Productivity Press, s. x-xv, s.1-18, s.257-270
Koenigsaecker G., 2009, Leading the Lean Enterprise Transformation, Productivity Press, New York
Marasinghe U., 2012, Road to Excellence Incredible 5S for Productivity Improvement, Friesen Press
Misiurek B., 2016, Standardized Work with TWI: Eliminating Human Errors in Production and Sevice Processes, Productivity Press, New York
Moore R., 2004, Making Common Sense Common Practice: Models for Manufacturing Excellence, Elsevier Science, s. 180-182
Moore R., 2004, Selecting the Right Manufacturing Improvement Tools: What Tool? When?, Elsevier Ltd., s.7-13, s.XVIII
Moulding E., 2010, 5S: A Visual Control System for the Workplace AuthorHouse 3/29/2010
Moulding E., 2012, 5s: A Visual Control System for the Workplace, Author House, UK, s. 15-57
Oakland J.S., Marosszeky M., 2017, Total Construction Management: Lean Quality in Construction Project Delivery, Routledge
Oppenheim B.W., Felbur M., 2015, Lean for Banks: Improving Quality, Productivity, and Morale in Financial Offices, CRC Press, New York
Perezgonzalez J.D., 2005, Construction Safety Management, A Systems Approach, Knowledge Management Edition
Rother M., Harris R., 2001, Creating Continuous Flow, Lean Enterprise Institute, Inc.
Rowlinson S., 2004, Construction Safety Management Systems, Spon Press, London
Rubin M., 1996, 5S for operators, New York: Productivity Press, s. 115-121
Salem O., Solomon J., Genaidy A., Luegring M., 2005, Site Implementation and Assessment of Lean Construction Techniques, Lean Construction Journal, January
Shook J., Marchwinski C., 2014, Lean Lexicon: A Graphical Glossary for Lean Thinkers, Lean Enterprise Institute, Inc
Spear S.J., 2005, How Toyota brings up managers, Harvard Business Review Polska, No. 23, January 2005, pp. 92-102.
Womack J., Jones D., Roos D., 1990, The Machine That Changed the World: The Story of Lean Production, A Division of Simon & Schuster, Inc., s.10
Womack J.P., Jones D.T., 2003, Lean Thinking: Banish Waste And Create Wealth In Your Corporation, Simon & Schuster UK Ltd
Wrona, B.; Graupp, P. 2006. The Twi Workbook: Essential Skills for Supervisors, Productivity Press. New York.
Yogesh M., Chandramohan G., Arraka R., 2012, Application of Lean in a Small and Medium Enterprise (SME) Segment- A Case Study of Electronics and Electrical Manufacturing Industry in India, International Journal of Scientific & Engineering Research Volume 3, Issue 8, s.1
I am Assistant Professor at Wroclaw University of Science and Technology and Vice President of the Board at LeanTrix. Responsible for the development of the TWI program and Lean Management methods for the construction industry. Deals with the use of 5S and Kaizen methods in the organization of construction works in order to improve and ensure occupational safety. Defended her PhD thesis in the construction discipline at Wroclaw University of Science and Technology. The author of several articles in English devoted to the use of Lean Management and TWI methods in the field of the construction industry. Has advised many companies regarding Lean Management.