SOP (Standard Operating Procedure) on The New Projects. The benefits of implementing work standardization and training in accordance with the
TWI Job Instruction methodology are obvious, and a significant number of enterprises are already aware of these benefits. Most often, however, we decide to implement it on existing and well-known projects. I would like to convince everyone that the implementation of TWI in the launch phase is profitable for everyone, and we should start this process from the moment of producing the very first pieces.
The launch phase of a new project largely focuses on the technical sphere of the process. Looking at the process from the operator’s point of view often happens too late. During the production phase, it is already necessary to modify the process, and at this stage the costs of changes are much higher than during the launch phase.
Start with PFMEA
The inclusion of Work Standardization and SOPs from the moment of building PFMEA (Process Failure Mode and Effect Analysis) allows for a better understanding of the most important elements of the process, and when we are unable to protect ourselves against problems with technical solutions, we must act in the human sphere. Full analysis of the operator’s work at the future workplace allows many problems to be spotted and also prevents them from occurring during serial production. A well-developed standardization of work almost enables the process to be secured to the same degree as technical solutions. The graphic below will help you to understand that it is worth bearing the cost of preparing work standardization at an early stage of building the process.
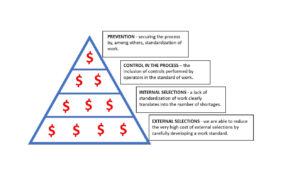
PFMEA
Ok, but how to do it when it is still far from the SOP…. someone may ask. I will base my answer on a specific example of starting a new project. The project is extremely demanding because despite the significant automation, the operators still have a dozen or so manual operations – 16 on one product, and 14 on the other. These are operations related to the application of components. With such an intensity of manual operations, it is not difficult to make a mistake or omission, and the costs of complaints are enormous. Here is where
standardization works perfectly well, and allows us to develop a kind of automation of human work.
How to start?
Work standardization on new projects. We started the standardization process by selecting a production team – experienced operators who at the same time are
TWI Instructors. These people, when making the first pieces, looked at the process in terms of training new employees. However, the most important thing is to look for the optimal solution for each of the smallest activities. The sequence of activities, method of implementation, operation time, and ergonomics at the workplace – all these factors were thoroughly analyzed to finally give a work instruction that will clearly respond to the requirements of the process/customer. The participation of experienced operators, and at the same time TWI Instructors, in the process of building work instructions also arouses enormous conviction and trust in the described process. Instructors who train other people take great care to maintain the standard and are able to defend it in every way. Nobody imposes a standard from above, and it is developed jointly – by using such a scheme, we avoid some resistance to new things.
Develop SOP
To develop the SOP, i.e. a standard for training new operators, production is necessary – pieces on which we can operate. There is a problem with this early phase of developing the process. We prepared 3 training sets that have been used many times. The components were reusable, chemicals such as glue or primer were replaced with water, and the tools were exactly the same as in the target process. Repeating the operations on the training sets allowed for the refinement of workstations in terms of ergonomics, time, and the placement of components. When working on training pieces, operators deal with a real process, but well before the SOP (Start of production). This enables the sequence of actions to be mastered, the time of each operation to be specified, and finally, the place in which potential problems are expected to be identified.
We also put a lot of effort into process visualizations. At each stage of the process, we included clear descriptions of what should be done to help new people in their new jobs. We also prepared the so-called electronic operator’s panel, in which an operator has the opportunity to find all the necessary information, including videos that show the performance of activities.
Conclusion about SOP
Work standardization on new projects. The entire standardization process, from the very beginning to the training of subsequent people in the process, includes elements related to work safety and quality. The final result is a comprehensive and compact form, on the basis of which the operator performs work on his workstation. The SOP can be presented in
digital form through
SOP software.
In the case under discussion, for over 50,000 produced units, which included over 750,000 applied components, an operation was omitted only 8 times. During data analysis, it was found that 6 came from one package – they were a result of problems in the process. The other two were created during the early training phase. All defects were detected internally.
It is not possible to indicate the SOP preparation scheme because we approach each process individually. Today, however, we are sure that a good standard that is prepared early results in a serial process and is also an excellent basis for further development.
A graduate of the Upper Silesian University of Economics in Katowice in the field of Sociology and the University of Technology and Humanities in Bielsko-Biała in the field of Management and Production Engineering. He has been involved in production processes since 2005, Currently TWI / BTO Coordinator and Trainer at Cooper Standard Automotive Polska in Bielsko-Biała.