Training Within Industry – Overview. Have You heard about Training Within Industry (TWI)? – yes yes, I know it’s about these instructions! – NOPE!
- Reducing training time by more than 25% in 100% of companies participating in the program,
- Increasing productivity by 25% or more in 86% of companies,
- Reducing the labor intensity per product by 25% or more in 88% of companies,
- Reducing scrap by over 25% in 55% of companies
- TWI Job Instruction
- TWI Job Methods
- TWI Job Relations
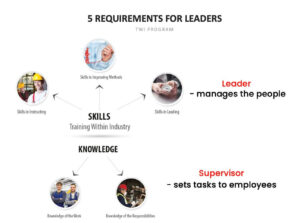
Fig. 5 Requirements for leaders
Training Within Industry (TWI) is a comprehensive program developed during World War II by the United States government to address workforce training and industrial production needs.
TWI consists of several modules, including Job Instruction (JI), Job Relations (JR), and Job Methods (JM), each focusing on different aspects of training, teamwork, and process improvement.
Job Instruction (JI) is aimed at improving the training process by providing supervisors with a structured method to effectively train employees in standard work procedures.
Job Relations (JR) emphasizes the importance of positive employee relations and provides supervisors with skills to build trust, resolve conflicts, and promote cooperation within the workforce.
Job Methods (JM) focuses on process improvement by teaching supervisors how to analyze and streamline work methods to eliminate waste and increase productivity.
TWI is known for its emphasis on developing frontline leaders and empowering them with the skills to train, engage, and motivate their teams.
The TWI methodology is based on the principles of standardization, respect for people, and continuous improvement.
TWI has been widely adopted across various industries, including manufacturing, healthcare, and services, for its effectiveness in enhancing employee performance, teamwork, and process efficiency.
The TWI program emphasizes the importance of creating a culture of continuous learning and improvement within organizations.
In today’s dynamic and competitive business environment, TWI remains relevant as a valuable tool for developing skilled leaders, improving employee engagement, and driving operational excellence.
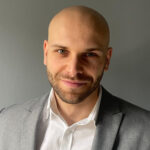
He is a Senior Consultant of the TWI program and Lean Management at LeanTrix. He is also a leader in the startup project - etwi system. He was a member of a global team that implemented the TPM system for several automotive plants in Europe, Asia, South America and North America.