Total Productive Maintenance Explained. TPM and the 8 Pillars of TPM are described in this video?
The history, the 6 big losses, and the type of maintenance are covered, too. This video aims to be a complete TPM to learn how to implement TPM by knowing all the basics and practical tips.
Table of Contents
ToggleWhat is Total Productive Maintenance?
In today’s fast-paced business environment, organizations are constantly striving to optimize their production processes, improve equipment reliability, and maximize overall efficiency. One proven methodology that has gained significant recognition in achieving these goals is Total Productive Maintenance (TPM). TPM focuses on involving all levels of an organization to ensure the effective management and maintenance of equipment, leading to enhanced productivity and reduced downtime.
The Principles of TPM
TPM operates on a set of key principles that promote a holistic approach to equipment maintenance and management. These principles include:
- Equipment Efficiency: TPM aims to improve equipment effectiveness and reduce losses by maximizing availability, performance, and quality. It involves implementing preventive maintenance strategies, conducting regular inspections, and addressing equipment issues promptly.
- Autonomous Maintenance: This principle involves empowering operators to take responsibility for routine equipment maintenance tasks. By training and involving frontline employees in cleaning, inspection, and minor repairs, TPM promotes a sense of ownership and proactive maintenance culture.
- Planned Maintenance: TPM emphasizes planned and systematic maintenance activities to minimize unplanned breakdowns. It includes creating maintenance schedules, conducting predictive maintenance through condition monitoring, and optimizing maintenance tasks to reduce downtime.
- Quality Maintenance: TPM integrates quality management principles, aiming to eliminate defects and improve overall product quality. By addressing the root causes of quality issues and implementing preventive measures, TPM enhances product reliability and customer satisfaction.
- Training and Skill Development: TPM recognizes the importance of equipping employees with the necessary skills and knowledge to perform maintenance tasks effectively. Training programs are conducted to enhance technical expertise, problem-solving abilities, and teamwork, fostering a culture of continuous improvement.
What is Total Productive Maintenance – movie
During my 20 years of experience as a Lean Expert and Trainer, I have seen many Lean Journey … some of them failed but some of them brought people and companies to incredible results. I always liked to teach others and I am happy when they have success.
This is the reason why I started in 2010 with my first website on Lean and by continuous improvement, I decided to found LeanVlog.
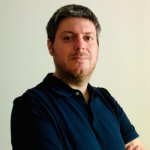
Andrea Manti is CBDO at Lean Community. He has over 15 years of experience in Lean Management. He is an expert in Lean and Quality Management and has held positions working as a Process Engineer, Customer Quality representative, Quality System Manager (IATF standard), and Continuous Improvement Senior Manager. During his career, Andrea has led the implementation of several Lean/6Sigma projects, TPM workshops, and TWI activities. He is also an expert in the World Class Manufacturing (WCM) program