The Importance of KPIs. It is well known the importance of choosing good KPIs to track both effectiveness and efficiency of a process. In a lean manufacturing business, tracking numbers is as much as important as the results itself, while in different businesses (such as service providers), organizations are still struggling to pick up the way to monitor how good (or bad) they are performing. But, is tracking some numbers enough to understand how we are performing?
Let’s take a deep dive into the world of KPIs!
Table of Contents
ToggleHistory of Key Performance Indicators
William Edwards Deming said; “If you can’t measure it, you can’t manage it”. This is probably the moment when the idea of measuring and tracking numbers became something real. Deming is as well the father of the Deming Cycle, with its basic but fundamental idea that all our efforts must be “checked” to be sure we were effective. Deming’s job in Japan, the PDCA cycle and TWI are all linked together by the fact that the check phase is as important as the do job.
Later on, many organizations developed their own system to track production efficiency or financial results, but thanks to Peter Drucker (a professor, writer and business consultant) the KPI Dashboard started to be popular in the 90’. The idea of having a complete set of indicators that are covering all company’s areas was defined.
Management by Objectives
A key principle of this management style (learn more here: https://leancommunity.org/everybody-lies-management-by-objectives/) is the idea that all our actions and efforts must be deployed in a number we can easily visualize and measure; all targets should be clearly visible and spread at all employee levels. But can we really cover the complexity of an organization with just a few numbers?
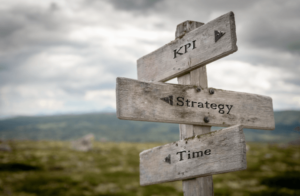
- Output = the past: KPI are, per definitions, numbers that are measuring an output. And here we have the first problem: there are some areas where just measuring the output (= something already happened in the past) is not enough.
- Input = Actions: many KPIs are focusing on just on results, but are not tracking the actions and efforts to get a results
- Short Terms: as KPI are tracking mainly output we want them to be as much as possible up to date and close to the event, that means with limited visibility to the future (but with lot of historical data to rely on)
- Cost Structure: the way we are elaborating production costs can deliver “wrong” message through the KPIs.
KPIs in Lean Production
Two items from the list above are critical when talking about lean manufacturing: Input/actions and cost structure.
Input/Actions
Lean (and in general Toyota approach) is mainly about people’s engagement to improve the daily job. This engagement is made of hundreds of small actions and details (kaizen) that are hard to track, and thus ignored by management. On top, all these actions include failures, trials, and learning events that are not producing a real output. The activity above is fundamental for the organization to grow and improve, but is rarely measured as input: at best, we could find some records such as “how many improvements ideas from operators”, “kaizen suggestions” or “kaizen events”, always with numeric defined goals and an output. Some companies developed a different way to approach this problem, using KAI (Key Actions Indicators), with the idea to measure actions from employees and how much people are active.
But the good (and difficult) solution could be to really measure the trigger events that may generate the expected output.
- How much time an employee can dedicate to improve or to coach somebody else?
- How many coaches or trainers do we have in our department?
- How many events started from operators and not from supervisors pushing for them?
- How many training hours were dedicated to a specific topic?
These above are examples of data that can be tracked (even without setting a goal), to measure the temperature of people’s engagement in our departments, and are all related to the actions that are the input of the hard KPI.
Cost Structure
KPIs (especially production indicators) are showing just one side of the story. Standard costing, the most used approach, is focused on prioritizing (thus reducing) labor and time, optimizing assets’ utilization (that is load machine to the maximum), in other words.. accelerate! OEE (Overall Equipment Efficiency) is one most famous indicator that is leading organizations in trying to speed up processes, machines and people in order to be close to 100%. If this may be correct from a certain point of view, it may be misleading too.
OEE can make us think, for example, to reduce numbers of changeovers or increase the batch size as this will give an immediate win, instead of making us think how we should improve to reduce and optimize the management of changeovers (that is the long road to get to the same result).
The Importance of KPIs. In terms of labor cost, the focus will be to reduce the operator’s time by doing the job faster instead of doing it better by rebalancing the operators’ workload (again is the shortcut vs the long term result).
Generally, classic indicators in combination with standard costing will make us think to move in the direction of working faster than what we really need, spreading our cost in other directions or departments instead of really working to reduce that costs. Remember also that accelerating will improve some KPIs but may also increase lead time, generating hidden costs and wastes that are not covered by our numbers.
Does it mean that OEE and Labor efficiency are wrong? Of course not, but we must be aware (and ready to prove) that our classic KPIs are not the only thing we need to look to proceed in the good direction of a real improvement.
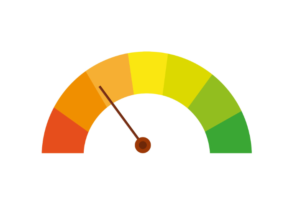
10 golden rules for Lean KPIs
I can try to summarize with some tips you can look for in your organization that may help to understand how to make better decisions and organize finally your dashboard of numbers!
- Don’t stop at classic KPIs, be creative!
- Focus both on input and output
- KPIs are not forever – change them according organization’s culture and improvements
- Remember to track actions and activities, not only results!
- Don’t be slave of KPIs – culture’s shift is slower than numbers
- Learn to read beyond numbers
- Think in long-term
- Look at whole trend
- Measure things that are worth
- Don’t focus on money only – there are things that have no value!
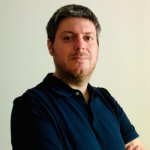
Andrea Manti is CBDO at Lean Community. He has over 15 years of experience in Lean Management. He is an expert in Lean and Quality Management and has held positions working as a Process Engineer, Customer Quality representative, Quality System Manager (IATF standard), and Continuous Improvement Senior Manager. During his career, Andrea has led the implementation of several Lean/6Sigma projects, TPM workshops, and TWI activities. He is also an expert in the World Class Manufacturing (WCM) program