SMED – initial setup selection strategy. Have you decided on SMED Workshops and optimization of the machine park setup process in your organization? That’s good! After all, machine setups, like breakdowns, are an integral part of your production process. And just like breakdowns, setups can also be optimized. In the coming articles, I would like to share with you my knowledge and observations about SMED. But before we get to that, let me tell you what SMED personally means to me.
Table of Contents
ToggleSMED – or optimal setup
For me personally, SMED is a thoughtful and optimized method of setup. Does it have to be one-minute (Single Minute Exchange of Die) according to the definition? For me, no. I have been on projects where changing molds in an injection molding machine (two molds together 8 tons) took about 1:45h. And that was already a success. For me, the single minutes in setup are a goal. Just as “zero failures” is a goal in TPM. A goal that we may never achieve, but which we must strive for. Can we say that companies that have failures do not have TPM? No. Similarly, we cannot say that companies that set up in more than 9 minutes do not have SMED. They may have it. It’s just such a specificity of work and process. Since you’ve decided to optimize setups in your company (good for you), you might be wondering which area or which machine is best suited for this. There are several options, the choice is yours.
SMED – The Easiest Setup
It’s a good idea to start your SMED journey with small steps. Start where it will be easiest for you. Choose an uncomplicated setup process in which you can clearly and concisely identify the individual steps. Let these be SMED workshops during which you can quickly determine with a group what belongs to internal activities and what to external ones. Time will come for more difficult setups. And necessarily, let it be a setup performed by one person. The idea is to focus on observing the tasks of one person. Time will come for two or three-person setups. Focus on the methodology, you don’t need additional confusion.
The Longest Setup Time
Choosing the “easiest” setup is one of the options. It allows you to practice a bit before more serious SMED workshops. Another option is to analyze the setups we have in the company and choose the machine or process that takes the most time in a certain period. I’m using a bit enigmatic language here speaking of the biggest time loss in a specified period. Why not just say to choose the longest setups? Because perhaps there will be a situation at your place that “Machine A” has a setup that lasts 16 hours. In a month, there are on average 2 such setups. There is also “Machine B” whose setup time is “only” 4 hours. So much better than “Machine A”. However, the number of setups on this machine averages 3 a week. 3 setups a week for 4 hours give us 48 hours of downtime for setup in a month. Assuming a setup time reduction of about 10% (a realistic approach) gives us savings: “Machine A” – 3.2 hours of savings in a month “Machine B” – 4.8 hours of savings in a month
Start with TOC
I am not an expert in TOC (Theory of Constraints) but the perspective that the Theory of Constraints gives us in the context of SMED is professional and conscious. Why specifically TOC / bottlenecks? Because if we have many product families, different batches, references, and machines, it is worth optimizing them in places that constitute limitations of our production process. According to TOC, if we improve the material flow and eliminate limitations and waste (MUDA) from the bottleneck, our entire value stream should improve. The theory is valid and worth considering.
Focus on a Creative TEAM
SMED – initial setup selection strategy. Most of us like to base our decisions on data. Especially in professional life. The same applies to choosing an area for setup optimization. However, apart from data, Gemba is also about people. And here comes the fourth proposal. Start SMED activities where you have the most engaged team. Where at the word “problem,” you hear “solution.” Where “impossible” and “it has always been this way” does not exist, and instead reigns “let’s try, it’s always something forward.”
Above, I have presented you with 4 possibilities where to start activities related to SMED Workshops. From the easiest area through the theory of constraints, focusing on the longest to focusing on a well-coordinated team. Which path you choose depends on you. One thing is certain, it will be a good choice. And maybe you know other methods? If so, share them in the comment.
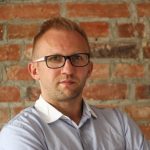
I was lucky that everything I learned about Lean, Kaizen, or production optimization started in a Japanese company. There, under the supervision of Japanese staff and during training in Japan, I learned how to approach the Continuous Improvement process. Over time, I also learned about other practices in other companies.