Table of Contents
ToggleImprove OEE and reducie failure rates? Ask yourself 10 simple questions and learn from the last failure.
Improve OEE. Is the end of the failure simultaneous with the end of the activities related to the given failure? In a healthy approach, which is focused on the reliability of the machine park – no. Apart from the analysis of the failure and its causes, today I would like to share with you something that may not be a solution to the problem, but may actually protect you from a similar failure on other similar lines / machines / components. Therefore, when a failure occurs, especially on machines with a criticality of A or B, it is worth answering the following questions. These are just some questions that will take you a few minutes, but which may in the end save you hours. This material is part of the TPM training that I can conduct with your team on your machines. We can improve OEE.
Have there been failures in the past that had the same root cause as the analyzed failure?
This question is intended to make the maintenance services aware of whether there is no “deja vu” in relation to the root cause of a given failure. It is possible that there have already been failures in the past that had similar effects or causes. Such knowledge is very valuable in many aspects, and a reliable answer to the following question will significantly affect the efficiency of the machine park. We are talking about how to improve OEE, as well as MTBF and MTTR.
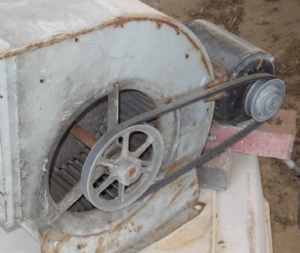
Pic. 1
Does the machine require additional work from the maintenance department?
It is often the case that failures are so called firefighting. As everybody knows, it should be put out as soon as possible. When the fire is extinguished, the machine’s functionality is restored, and production is started, maintenance activities (repair) finish and production begins. This repair is often carried out under the pressure of time. As soon as possible. Due to this rush, but also sometimes due to the lack of appropriate components, certain activities are done “temporarily” using “temporary” solutions (something is welded, glued, or components are “regenerated” in the workshop). It is not uncommon for cables to be arranged “temporarily”, or other makeshift solutions that save the situation to be implemented. It is therefore worth asking yourself whether there is any need to return to this machine in order to close the topic, or replace the components with original ones – thus spending more time so that the condition of the machine is in line with expectations.
Should other machines be checked with regards to this failure?
If you have similar machines/lines in your company, and some components are similar or even the same, it is worth asking yourself whether it is worth checking other machines with regards to a given failure? For example, if the coupling with the insert on one pump has been damaged (natural wear off), maybe it is worth inspecting the remaining pumps? This is especially the case if we do not know what their condition is and we do not have scheduled inspections or replacements for these components. These activities can already be called “prevention through inspection”. This simple procedure will allow you to avoid further similar failures and, after the inspection, will allow you to prepare for replacement with regards to spare parts and the planned downtime of the machine.
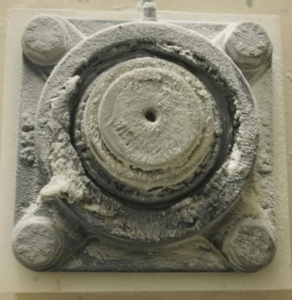
Pic. 2
Are the parts replaced during a breakdown subjected to preventive replacement?
This question is very important in preventing failures in the future. In this case, we can:
- If the replacement of parts or elements was scheduled for preventive replacement – the current time period should be verified in relation to a given failure. Perhaps the replacement period has not been properly and accurately estimated, perhaps the replacement has not been performed, or perhaps the machine’s operating conditions have changed and the previous assumptions no longer apply.
- If there are no plans for preventive replacement – it may be worth considering implementing preventive actions for the future. If we are talking about downtime, the time or effect of which is not acceptable – counteract it. Without an answer to this question, we will miss the opportunity to improve our maintenance processes.
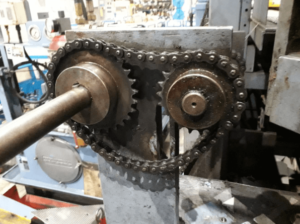
Pic. 3
Are TPM actions defined for a given part or subcomponents? How to improve OEE.
This is another question that should help us develop the scope of planned inspections (Continuous Maintenance). If so far there were no plans defining certain TPM actions for damaged parts/subcomponents, maybe now is the right time to expand these plans to include them. While the previous question referred only to preventive replacement at a specific time interval, we are now looking for answers of whether to use other TPM tools such as inspection, diagnostics and Autonomous Maintenance in relation to a damaged subcomponent.
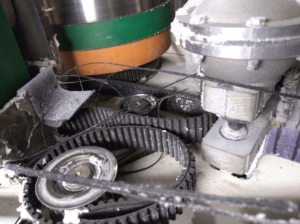
Pic. 4
Is it possible to upgrade damaged components to prevent failure in the future?
Perhaps there is another way to reduce the failure rate of a given subcomponent/machine. Perhaps it is not necessary to replace preventively, or to use tools related to prediction. Perhaps you can enter the Kaizen path and modernize the machine/subcomponent, and implement improvements that will reduce the failure rate. Sometimes the best way to get rid of a problem is simply to eliminate the possibility of it happening again in the future. There are many interesting solutions on the market that will certainly reduce or even eliminate the risk of failure in the future. Kaizen, small steps forward.
Can the failure result from previous maintenance activities?
Let’s agree that during works or inspections, we can always (unknowingly) put something together wrong, set it up badly, or simply damage it. And of course, there is “half trouble” if the effect of this mistake is visible immediately during the failure. This gives us the opportunity to react immediately and fix unintended, but also undesirable, consequences in the form of the failure. The problem becomes a bit more serious and more difficult to grasp if the effect of previous errors or mistakes is only visible after some time in the form of an unplanned failure. Sorry, it happens. This question is not intended to find and crucify the guilty party. This question is intended to get to the root of the problem, and improve the performance of maintenance services. Perhaps there is a lack of knowledge, perhaps a lack of tools, or perhaps the standard or method of work simply needs improvement. If the answer to this question is “YES”, there is always room for improvement.
Can the failure result from the earlier actions of other departments?
Since we are looking for opportunities to improve, which result from previous actions of maintenance services on the machine, we must ask the same question towards other departments. It will not be anything revealing if I say that some of the failures that take place may result from the actions of other departments. Wrong settings, exceeded parameters and improper adjustments are just some of examples. Improperly made retooling – a classic of the genre. These things happen. It is important that when they occur, the appropriate initiative is taken and, for example, awareness is trained and raised.
Is it necessary to introduce spare parts to the warehouse of the maintenance department?
Well, ask yourself how many times there has been a situation that something was regenerated quickly (although it was barely alive), someone was driving somewhere for parts, or the parts in question had to be obtained immediately in order to end the failure as soon as possible and to start production. Exactly. Therefore, this question is intended to provoke some reflection. Shouldn’t the part or subcomponent that was damaged in the analyzed failure be in the maintenance department warehouse? Of course, there will be different answers for critical machines, different answers for low-critical machines, different answers if we have several of the same machines, or different if we only have one. Classic of the genre – “It depends.”
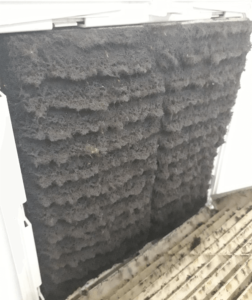
Pic. 5
Do you propose any actions to be conducted by other (post-emergency) departments, e.g.: TPM/PROD/PE/QA?
As part of TPM, we know that failures are not just a “problem” of the maintenance department. The effect of failure affects every department: Production (lack of workmanship and pieces), Quality (defective pieces), Engineering (loss of process settings), OHS (increased risk at work). Every department. Even Sales (no products for the customer). Therefore, bearing in mind the common interest, we all ask ourselves this question. Are any actions of other departments suggested in the case of this failure? Maybe additional cleaning, maybe specifying some machine parameters, or maybe improving the condition of machine equipment and tools. It’s worth asking, especially if it can help us. I gave you 10 questions above. Simple but effective – in my opinion. Perhaps passing the above-mentioned questions through the sieve of only some failures will help you in your daily work to reduce the failure rate and improve your KPI.
What’s all this for?
The task of the Maintenance Department is not to remove failures. It is to prevent them. Improve OEE with TPM.
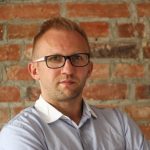
I was lucky that everything I learned about Lean, Kaizen, or production optimization started in a Japanese company. There, under the supervision of Japanese staff and during training in Japan, I learned how to approach the Continuous Improvement process. Over time, I also learned about other practices in other companies.