Effective supervisor and challenges. In an era of rapid technological progress and constant change, many organizations equate development with the need for transformation. However, not everything new is better—and some proven solutions from the past still hold significant value and relevance. One such solution is the Training Within Industry (TWI) program, which has helped organizations build true operational leadership for nearly 100 years.
It is this very program that forms the foundation of the Effective First-Line Supervisor model—a role with a tangible impact on the performance of production, service, and logistics teams.
Table of Contents
ToggleWhy Is an Effective Supervisor Key to Organizational Success?
First-line supervisors make up the largest group of leaders in any organization. They manage daily operations, make dozens of decisions each day, influence employee motivation, and directly impact the quality of work performed.
Yet the role of an effective supervisor is often undervalued—especially in organizations that focus primarily on high-level tools and strategies, forgetting that success starts with strong foundations. And that foundation is operational leadership: daily, conscious, and competent.
The Effective Supervisor in the Context of TWI
Training Within Industry (TWI) is a program developed during World War II in the United States to rapidly increase industrial workforce efficiency. Although nearly a century has passed since its creation, its methodology remains unchanged—because it still works.
TWI develops three critical areas:
1. Knowledge of Work and Responsibilities
An effective supervisor must not only understand their duties but also grasp the goals, processes, and standards within their scope. This knowledge is the starting point for decision-making, training employees, and driving results.
2. Practical and Interpersonal Skills
The TWI program places strong emphasis on the ability to:
-
deliver instructions clearly and consistently,
-
improve work methods,
-
build strong team relationships,
-
ensure workplace safety,
-
solve problems based on facts and data.
An effective supervisor is not just a technical expert—they are a person who can teach, support, and energize a team.
3. Leadership Attitudes and Responsibility for People
The most difficult yet most important element of leadership is attitude. An effective supervisor understands that their role is not only task management, but more importantly, the development of people and responsibility for the team. They are a leader who serves, inspires, and leads by example.
TWI as a Foundation for Work Standardization
One of the key outcomes of TWI implementation is the creation of standardized work. This very element is the foundation of the Toyota Production System—a framework that revolutionized global manufacturing.
It’s worth noting that post-war Toyota relied heavily on TWI principles to build its work culture. It was through this approach that the company learned how to transfer knowledge, teach effectively, and create consistency in operational actions.
Should We Combine TWI with Modern Technologies?
Absolutely—provided it is done with respect for the original methodology. In our team, we implement digital tools like KaizenUp that support leaders in their daily work. For example, we use artificial intelligence to generate ideas for improving work methods.
However, we always rely on the proven structure of TWI. We don’t change what works—technology is there to serve people, not replace fundamental leadership competencies.
How to Develop an Effective Supervisor in Practice?
To meet organizational needs, we’ve created a course titled Effective First-Line Supervisor. This program is designed specifically for operational leaders—those responsible for production, logistics, and service teams on a daily basis.
For organizations ready to go further, we also offer two levels of certified courses:
-
Certified TWI Instructor (Level 1) – focused on effective on-the-job training based on the TWI methodology.
-
Certified TWI Trainer (Level 2) – focused on developing coaching skills and building a long-term talent development system within the organization.
Real-World Examples of TWI Implementation
TWI is not a theory—it’s a proven system. You’ll find examples of successful implementations in companies like LEGO, where their entire talent development strategy was built on the TWI framework.
Similarly, at Cooper Standard, the Building a Talented Organization program was essentially a comprehensive TWI deployment. The results were measurable—greater operational stability, improved team engagement, enhanced safety, and increased efficiency.
Don’t Start Lean Management Without TWI
This is one of the most important lessons from manufacturing companies around the world: do not begin your Lean journey without first implementing TWI.
Without work standardization, you won’t build a stable system, achieve continuous improvement, or create a culture of accountability. And standardization is precisely the result of a well-implemented TWI program.
Conclusion: An Effective Supervisor Is an Investment in the Foundation
Developing effective first-line supervisors isn’t a trend—it’s a strategic decision. TWI proves that true leadership isn’t about catchy slogans; it’s about daily work, knowledge, skills, and attitude.
Technology can support this development—but it cannot replace the human element. And that’s why some things are simply better left unchanged.
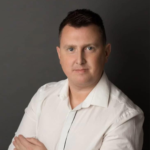
Dr. Bartosz Misiurek is a co-founder of a few start-ups like Leantrix, Lean Community, Leancoin, etwi, Lean Global Consulting, Sallar. He is a CEO at LeanTrix Ltd., Leancoin Ltd, Do Lean IT OU, and a Member of the Board at Astral Hodling OU. Author of the book “Standardized Work with TWI: Eliminating Human Errors in Production and Service Processes.” He works as Sr Manager and TWI Global Coach at Automotive Company.