5W1H and Kaizen. Have You ever heard about 5W1H (first letters of the questions asked)? The 5W1H approach was fully adopted by Toyota and incorporated into the Toyota Production System as the major kaizen-building method (read more about 10 principles of Kaizen). Asking the questions aims at getting the largest number of ideas for work method improvements. It is important not to reject any idea, even if it seems to be unrealistic at the beginning. The first five questions of 5W1H are oriented toward seeking improvements in a work method. Their meaning is described below, one by one.
Table of Contents
Toggle5W1H Questions and Kaizen
The 5W1H questions are a set of inquiry tools that dive into the essential aspects of any situation or problem. “Who” identifies the people involved or affected, understanding roles and responsibilities. “What” focuses on the subject matter, asking for specifics about what is happening or needs to be done. “Where” locates the situation geographically or contextually, pinpointing where an event is taking place or where a task should be executed. “When” deals with the timing, determining the time frame or deadline relevant to the subject. “Why” digs into the reasons or causes behind the situation, seeking the underlying purpose or rationale. Lastly, “How” explores the method or process, looking into how something should be done or how an event has occurred. Together, these questions provide a comprehensive framework for thorough analysis and problem-solving.
Question #1 / #2 WHY is it necessary? / WHAT is its purpose?
They are always asked first to consider if a given element is necessary at all. Elements without any logical explanation don’t need improvement. Such unnecessary elements are performed in many companies because workers got used to doing them. WHY is this work element necessary? is asked of an operator who will give us the reason of doing this element in a given way. WHAT is its purpose? serves as a control question we ask ourselves to consider if a given element shouldn’t be treated as a waste (Muda in Japanese). Waste is every non-value-added action in the process. There are 7 major waste types commonly distinguished:
- Inventory,
- Overproduction,
- Unnecessary transportation,
- Waiting,
- Defects,
- Unnecessary motion,
- Overprocessing.
5W1H and Kaizen. One should also note the eighth type of waste: unused employee creativity. It is visible in the worker’s reluctance to change and eliminate of the remaining types of waste. If, in the course of questions, you have an idea to eliminate a given element, write it down. Don’t analyze such work further, according to the golden rule by Peter F. Drucker: There is nothing as useless as doing efficiently that which should not be done at all! Well, it’s pointless to improve an element that shouldn’t be performed at all. If you are certain that a given element is needed, go further with the 5W1H questions.
Questions #3 / #4 / #5 – WHERE should it be done? / WHEN should it be done? / WHO is best qualified to do it?
The group of questions to consider if there is a better place, time, or person who could do a given element. One should take into consideration all limitations that require a given work element to be performed at a given time, place or by a given person. It is hard to imagine producing of surgery tools in conditions different than sterile or a forklift operated by a person without qualifications. The first 5 questions in 5W1H are about determining of a need of a given work element and, possibly, a work sequence. The last question means to improve a given work done by an operator.
Questions #6 – HOW is the best way to do it?
It is food for thought about better ways of performing of a given element. At this stage, we are sure that a given work element should be performed; plus we determined the best place, time, and person responsible for this element. Now, it’s time to consider better ways of application of existing: materials, machines, equipment, tools, and project solutions, to find the best method of doing a given element. This stage consists in generating ideas requiring financial expenditures. All ideas should be treated as workable and implementable. According to the spirit of kaizen, work should be improved using all resources available for a given company.
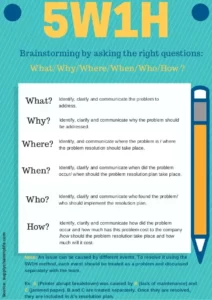
Source: SupplyChainMyLife.com
Method and Human
HOW is the best way to do it? doesn’t mean to get the best work sequence but to stimulate ideas on work and human work improvement, in particular concerning safety and ergonomy. Therefore, the 5W1H approach – the basis of kaizen – should be treated as an improvement in two areas:
- Method – by determining if a given element is necessary and developing the best work sequence (the 5W questions) which can written down in the Standard Operating Procedure.
- Human – by simplifying of an operator’s work in the areas of safety and ergonomy (the 1H questions).
Asking the questions in this sequence acts as a brainstorming stimulator. Contrary to brainstorming, 5W1H is excellent even in individual work analysis because it requires investigating every element one by one. Answers for the questions should be treated as ideas verified later, and finally implemented.
Conclusion for 5W1H and Kaizen
the 5W1H and Kaizen approach is a powerful tool for continuous improvement in the workplace. It not only helps in identifying and eliminating wasteful practices but also encourages innovation and optimization of work processes, considering both the method and the human aspects. This structured approach is effective for both team and individual work analyses, stimulating brainstorming and leading to practical, implementable solutions.
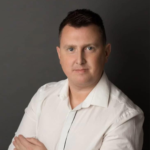
Dr. Bartosz Misiurek is a co-founder of a few start-ups like Leantrix, Lean Community, Leancoin, etwi, Lean Global Consulting, Sallar. He is a CEO at LeanTrix Ltd., Leancoin Ltd, Do Lean IT OU, and a Member of the Board at Astral Hodling OU. Author of the book “Standardized Work with TWI: Eliminating Human Errors in Production and Service Processes.” He works as Sr Manager and TWI Global Coach at Automotive Company.