TWI Job Methods is one of the key tools within the Training Within Industry (TWI) program. It focuses on building an organizational culture that drives process improvement and increases efficiency. These methods are crucial for companies aiming to manage change effectively, reduce costs, and engage employees in improvement processes. In this article, we will explain what TWI Job Methods entail, how to implement them, and why they are so important for modern organizations.
Table of Contents
ToggleWhat Are TWI Job Methods?
The TWI MP method is one of the five core methods in the TWI program, developed in the 1940s. Initially, it served as a tool to train workers during wartime. Today, many industries, especially manufacturing, rely on this method to stabilize and improve job processes.
This method focus on systematically analyzing tasks, identifying areas that need improvement, and implementing better solutions. This process involves breaking down each task into steps, analyzing these steps, and generating ideas for improvement.
How to Implement TWI Job Methods?
To implement TWI JM successfully, companies need to start by analyzing their current processes. Managers should divide each process into smaller elements to gain a clearer understanding of what happens at each stage. Asking critical questions helps in identifying potential areas for improvement. For instance, questions like Can this task be simplified? or Is it possible to eliminate unnecessary steps? are useful.
Once the improved method has been developed, the next step is introducing it to the team. Engaging employees is essential, as they have firsthand knowledge of the tasks. By gathering their feedback, companies can optimize the changes and ensure their effectiveness.
Why Are TWI Job Methods Important?
This approach provides multiple benefits for companies. First, they help boost productivity and improve job quality. In addition, better process management helps reduce waste and minimize the risk of accidents, which leads to improved financial results and a safer working environment.
Moreover, this methods foster a culture of continuous improvement. In this environment, every change is seen as an opportunity for enhancement rather than a challenge. Companies using these methods can also respond more effectively to changing market conditions, such as rising raw material costs or increased competition.
Factors Influencing the Implementation of TWI Job Methods
Several factors motivate companies to adopt TWI JM. External factors include high raw material costs, growing competition, and the need to maintain a competitive edge. Internally, companies may be driven by the desire to build a culture of improvement, boost production efficiency, or cut costs.
Goals of Implementing TWI Job Methods
The main goals of TWI Job Methods are clear:
- Increase efficiency: Optimizing processes allows companies to complete customer orders more quickly, thus enhancing their overall effectiveness.
- Reduce losses and accidents: Better organization and minimized risks lead to improved financial results and safer working conditions for employees.
- Build a culture of improvement: Organizations focused on constant process enhancement gain a competitive advantage and adapt more easily to market shifts.
- Standardize job processes: When processes become predictable, companies achieve operational stability and greater efficiency.
Summary
In conclusion, TWI Job Methods are highly effective tools for increasing operational efficiency, reducing costs, and fostering a culture of continuous improvement. They enable companies to enhance their processes systematically, respond to market changes swiftly, and achieve long-term success. By adopting TWI JM, organizations lay the foundation for sustainable growth and competitiveness.
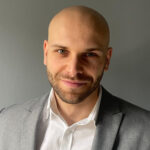
He is a Senior Consultant of the TWI program and Lean Management at LeanTrix. He is also a leader in the startup project - etwi system. He was a member of a global team that implemented the TPM system for several automotive plants in Europe, Asia, South America and North America.