TWI History Steps Examples. What is Training Within Industry (TWI), the history and the steps are explained in this video. The example and the results of the B17 are treated too. Industry-leading companies like GE, Boeing, and Toyota use TWI to train their employees. But what is it? In this video, you’ll see how TWI can be used in your company to improve productivity and reduce training time and quality.
Table of Contents
ToggleWhat is TWI Training Within Industry – Movie
Training Within Industry (TWI) is a powerful methodology that has garnered significant attention from industry leaders worldwide. In this article, we will delve into the essence of TWI, its historical background, the fundamental steps involved, and showcase an exemplary case study of its impact, particularly with the B17 aircraft production. Moreover, we will explore how industry giants like GE, Boeing, and Toyota have embraced TWI to enhance employee training and development. Discover how this approach can drive productivity improvements, streamline training processes, and elevate the overall quality within your organization by watching the accompanying video.
TWI History: Understanding its Origins and Importance
TWI emerged during World War II as a response to the need for rapid training and skill development in the industrial sector. It was introduced to standardize training methods, reduce training time, and enhance overall productivity within factories and manufacturing facilities.
Key Components of TWI
TWI comprises three core components: Job Instructions, Job Methods, and Job Relations. Job Instructions focuses on providing effective training to employees and writing SOPs (Standard Operating Procedures) that can be used for training purposes. SOPs should be split into important steps, key points, and reasons for the key points. Job Methods aims to improve work methods and processes for increased efficiency, while Job Relations emphasizes fostering positive workplace relationships and effective communication.
The B17 Example: Unleashing the Potential of TWI
The B17 aircraft production serves as an iconic example of the effectiveness of TWI. Through the implementation of TWI methodologies, the training time for workers was drastically reduced, enabling mass production of high-quality aircraft within record timeframes. This success story has become a testament to the transformative impact of TWI.
TWI in Industry-Leading Companies
Renowned organizations such as GE, Boeing, and Toyota have embraced TWI as a means to enhance their training programs and optimize operational efficiency. By implementing TWI principles, these companies have successfully standardized processes, reduced waste, improved product quality, and increased overall productivity in their respective industries.
TWI History and Future
The impact of TWI has been profound and enduring, extending far beyond its initial wartime context. Its principles laid the groundwork for what would later evolve into modern human resources training and development practices. Furthermore, the TWI’s emphasis on standardized work, continuous improvement, and effective leadership directly influenced the development of the Toyota Production System and lean manufacturing, which have become cornerstones of modern operational excellence. T
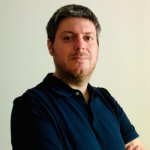
Andrea Manti is CBDO at Lean Community. He has over 15 years of experience in Lean Management. He is an expert in Lean and Quality Management and has held positions working as a Process Engineer, Customer Quality representative, Quality System Manager (IATF standard), and Continuous Improvement Senior Manager. During his career, Andrea has led the implementation of several Lean/6Sigma projects, TPM workshops, and TWI activities. He is also an expert in the World Class Manufacturing (WCM) program
During my 20 years of experience as a Lean Expert and Trainer, I have seen many Lean Journey … some of them failed but some of them brought people and companies to incredible results. I always liked to teach others and I am happy when they have success.
This is the reason why I started in 2010 with my first website on Lean and by continuous improvement, I decided to found LeanVlog.