Training Within Industry is a foundation of Lean Management. Imagine that you start implementing Lean Management with highly trained middle management. Leaders, foremen and managers, apart from extensive work experience and knowledge concerning the scope of responsibilities, have extensive skills in developing employees, identifying waste in processes, and engaging and solving interpersonal problems. In addition, they are sensitive to safety hazards in processes. You think that such conscious management is a treasure. On the other hand, you also feel that the assumptions we have presented are not very realistic, only theoretical…. According to the approach promoted by the Toyota Production System, the key people in the field of production management are mid-level superiors – leaders, managers, and foremen. The TWI – Training Within Industry program is responsible for the development of these people. You can implement the TWI program without Lean Management, but you cannot implement Lean Management without the TWI program. Find out why.
Table of Contents
ToggleThe Training Within Industry and Lean Management program – roots
The TWI program was established over 80 years ago in the USA. There are several books, articles, and publications dedicated to its history. Currently, the TWI program is recognizable and used by practitioners of both production management and non-production processes. There are many case studies of implementing TWI in an office environment, logistics, HR, and the construction industry. The universality of the TWI program lies in the fact that this program is not related to the processes that exist in a given company, but instead to the development of the competencies of the superiors who are responsible for these processes. Many of the methods that make up the Lean Management philosophy are only adaptable to selected types of processes, which is why Lean Management scalability is so difficult. Most people who operate in the Lean Management environment are aware that implementation success depends on the competence and awareness of their superiors, and not on copying the methods that are used in the Toyota Production System. That is why the TWI program, which builds management competencies among superiors, is so crucial. An additional feature of the TWI program is its enormous scalability and universality. The TWI program develops the following skills among superiors (Fig. 1):
- ensuring occupational safety (TWI Occupational Safety);
- team building and solving interpersonal problems (TWI Relations with Employees);
- work improvement and the identification of waste (TWI WorkMethods);
- learning and transferring knowledge (TWI Instructing Employees).
Fig. 1. Skills developed within the Training Within Industry program
Source: own elaboration
The order in the list presented above is not accidental. It is necessary to build the awareness of superiors in the field of occupational safety and to teach them to work with subordinates and be sensitive to work efficiency, which will ultimately affect the effectiveness of knowledge transfer. Only such a process can end in an effective transformation of a “superior” into a “leader”. However, knowledge about work, or knowledge concerning responsibilities will always be very specific for a given type of process, but the skills built in the TWI program are universal, regardless of whether we are talking about construction, administration, production, or even IT.
The TWI program – today
Unfortunately, the TWI program is currently mainly simplified to one of its methods: TWI Job Instructions. This is because many people have heard of TWI, but not many people have practiced its methods. A statistical analysis conducted by the Lean Community organization (leancommunity.org) shows that only 11% of Lean management practitioners also practice Training Within Industry methods (Fig. 2). In turn, as many as 81% of Lean practitioners declare that they have heard about the TWI program (Fig. 3). Their knowledge usually comes from articles that they have read, which are often entitled more or less as follows: “A quick method of on-the-job training – TWI”. Failure to understand the intentions of the TWI program is also the reason for the failure of its implementation in many organizations, which assume that the implementation of TWI only involves the training of a group of instructors in the field of transferring knowledge and creating production documentation. The TWI program shapes the competencies of superiors, and its implementation is only possible when an organization makes an effort to undertake this task.
Fig. 2. Percentage of TWI practitioners among Lean practitioners
Source: Lean Community, https://leancommunity.org/
Fig. 3. Percentage of Lean Practitioners who possess knowledge about the TWI program
Source: Lean Community, https://leancommunity.org/
Training Within Industry Program
The Training Within Industry program must be viewed as a complete program for developing supervisors with regard to the skills that are necessary to perform the role of leaders. This was also the original reason for the creation of the TWI program: the transformation of “foremen” -who are responsible for supervising employees – into “leaders” – who manage the work of employees, while at the same time taking care of their development. This is precisely why the TWI program has become the cornerstone of Toyota’s production system. To this day, practitioners from Toyota emphasize its key role in building the organizational culture of their company. It is worth referring to the book called “Toyota Talent” by Jeffrey Liker – a Toyota Practitioner. The book is devoted exclusively to the TWI program and the importance of building leadership competencies. Competent leaders are the guarantee of success when implementing Lean Management methods. Therefore, in the introduction to this article, a rather offensive phrase appeared: “You can implement the TWI program without Lean Management, but you cannot implement Lean Management without the TWI program.” The article briefly describes why the four key skills of supervisors are so important in the context of implementing Lean Management – Training WIthin Industry and Lean Management.
TWI Job Safety
Work safety is the basis and foundation of any advanced work organization system. Nowadays, it seems that the principles of safe work are commonly used in organizations. The fact is that accidents happen every day, and most of these accidents are caused by human error. Of course, mistakes do happen, and accidents at work are inevitable. However, an accident that arises as a result of ordinary human error is different to an accident that occurs as a result of dangerous working conditions or the unsafe behavior of an employee. The TWI JS method was created to develop the skills of superiors in identifying hazards in the workplace and teaching employees in the field of health and safety. The aim is to ensure that there are no unsafe working conditions, as well as to eliminate unsafe behavior among employees. After all, it is the leaders and superiors who are closest to the employees who directly work in the processes. Only they can perceive any dangerous employee behavior. Health and safety services are not responsible for work safety in an organization, but instead, it is the owners of the areas – often leaders, masters or managers. They should have basic knowledge in the field of hazard identification, teaching operators how to work following existing health and safety rules, and how to build an organizational culture based on occupational safety. The TWI JS method provides a simple recipe for how to identify hazards at the workplace and how to approach each hazard individually to develop a solution that will eliminate or reduce this hazard.
TWI Job Relations
Most production problems result from communication errors between superiors and subordinates. This communication involves the method of conducting on-the-job training, and also the way tasks and responsibilities are defined. Many production managers expect their middle managers to “deliver” the results they require. The problem, or maybe the challenge, is that supervisors achieve results through their subordinates. That is why teamwork is so important in every job. Yes, it sounds quite obvious, but teamwork has a huge impact on how e.g. a production cell works. A supervisor is responsible for building an employee’s commitment, through relationships, to work for the team. In addition, the role of the supervisor is to constantly solve interpersonal problems. There are more such problems than production problems, but unfortunately, they are not so visible. It is easier to see that a machine is malfunctioning than to see that one operator is blaming another for putting away some components incorrectly. When we buy a machine, we get several documents, training on how to use it, and external support. When we get a new man for the process, the supervisor knows nothing about him – tabula rasa. A leader must have skills in working with people for his team to achieve above-average results. These skills can be trained, among others, thanks to the TWI JR method. The TWI JR method is focused on both preventive actions – building relationships and commitment, as well as reactionary actions – solving existing interpersonal problems. It teaches leaders how to conduct a complete analysis of the situation and to make decisions based on facts, without jumping to solutions. The term “Leader” comes from the English verb “to lead”. A leader is a person who leads others. Think if your organization’s supervisors are prepared to be leaders.
TWI Job Methods
The term Kaizen comes from Japanese and means “change for the better”. Kaizen is derived directly from the Toyota Production System, but was inspired by the TWI program, and more precisely by the TWI JM method. This method aims to practice (among leaders) the ability to divide work into small elements and then generate improvement ideas for each of these elements. The goal is to “connect the dots” and work out the target work method. The TWI JM method is focused on improving the way people work, and therefore it is a universal method that can be used in all types of processes where human work occurs. The ability to improve is a key skill for supervisors because it is supervisors who should be able to see the waste in the work of their employees. However, it is not all about waste in processes. If we look at the eight types of waste, we can see that according to the Toyota Production System, the worst of them is the waste called “lost creativity”. This is nothing more than a waste of an opportunity to build a creative team that is not only focused on achieving operational goals but also on development.
TWI Job Instructions
TWI JI is the last of the four key leadership skills according to the TWI program, which is currently the most common TWI method. It was intentionally presented in fourth place because the process of instructing employees should apply to processes that are safe and standardized. Leaders who train other employees in these processes should already have leadership skills. The TWI JI method should be implemented as the last one in a comprehensive approach to the development of management competencies. The ability to share knowledge, the ability to teach others, is the highest level of “initiation”. You cannot just say “Go and learn.” In such a situation, instruction can do more harm than good. A leader must have adequate preparation to transfer knowledge effectively and efficiently. A leader must first be “built” to expect him to lead his subordinates.
The TWI JI method is an effective way for experienced employees to share knowledge about safe, correct and conscious work. In the TWI method of Instructing Employees, it is necessary to create a TWI JI that divides the work into main steps, key points, and reasons for key points. On-the-job training is based on the division of work according to the TWI instructions or SOP Standard. Thanks to this, we are sure that employees will know WHAT to do, HOW to do it, and, most of all, WHY they do it in this way – and this builds their awareness and sensitizes them to mistakes. It is a very big challenge to conduct on-the-job training by the TWI JI method. A leader must encourage a learner to not only show the work in his presentation but also repeat the steps, key points, and reasons for the key points. Correct on-the-job training requires all a leader’s competencies, and it is therefore very important not to reduce it to just the 4-step method.
Summary – Training Within Industry and Lean Management
There is a Chinese proverb that says: “Tell me and I will forget, show me and maybe I will remember, involve me and I will understand.” This proverb perfectly describes the intentions of the Training Within Industry program. This program was created to engage middle management to be open to proactive activities. Lean Management is nothing more than engaging people to improve the processes existing in their organization. That is why it is so difficult to imagine the implementation of Lean Management without the development of leaders in the organization. It is therefore very difficult to imagine the implementation of Lean Management without the TWI program. Training Within Industry and Lean Management work together.
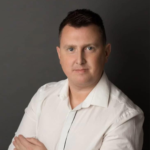
Dr. Bartosz Misiurek is a co-founder of a few start-ups like Leantrix, Lean Community, Leancoin, etwi, Lean Global Consulting, Sallar. He is a CEO at LeanTrix Ltd., Leancoin Ltd, Do Lean IT OU, and a Member of the Board at Astral Hodling OU. Author of the book “Standardized Work with TWI: Eliminating Human Errors in Production and Service Processes.” He works as Sr Manager and TWI Global Coach at Automotive Company.