TPM AM means Total Productive Maintenance – Autonomous Maintenance. Currently, most manufacturing companies use machines in the production processes that are often automated more often than not. In such processes, a worker hardly ever performs applied operations. It may seem that in such a situation, Standard Operating Procedures cannot be applied. Well, you couldn’t be more wrong. When operating machines are working in an automated mode, operators are responsible for:
- Actions related to Autonomous Maintenance (TPM)
- Machine retooling (SMED).
- Responding to problems/failures during machine operation
- The setting of machine parameters
- Quality control
- Etc.
Table of Contents
ToggleStandardization of TPM AM
Every one of these tasks can be standardized using SOPs. However, in rare cases, you will need to one should adjust the instruction standard to the type of process subject to standardization. And, as you can imagine an SWI for the setting machine parameters or quality control will look different from one for TPM, SMED, or response to failure. You may, you can have some doubts about what instructions should look like for these operations related to TPM, SMED, or response to failure in general. I’ll demonstrate some introduction on how to apply SOPs in TPM AM. Please notice that SOPs for TPM Am can be prepared in Software that supports the training process.
TPM AM – Autonomous Maintenance
Autonomous maintenance is understood as the performance of everyday cleaning and maintenance actions on a machine by an operator who exploits and uses it. It is one of the pillars of Total Productive Maintenance (TPM) pillars. The basis for preparing SOPs for autonomous maintenance actions on a machine is to work out a list of cleaning and maintenance operations. Such a table should include the following points:
- What to check and how to check it
- How to perform a given key point (tools)
- How often a given element should be checked
- Who is responsible for it
- How much time it consumes
- When a specific given task should be performed
- WhetherShould an autonomous maintenance action should be performed with the machine on or off
Based on these distinguished specified actions, you will be able to prepare an SOP for automated maintenance operations. To prepare the instructions, you will need to include task visualization because people more easily absorb information demonstrated using symbols and colors. For autonomous maintenance actions, it is necessary to visually present crucial elements dedicated only to these processes. The table below presents the way to visualize the autonomous maintenance actions visualization.
Autonomous maintenance action visualization
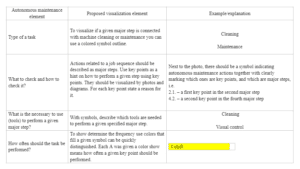
TPM AM SOPs – Example
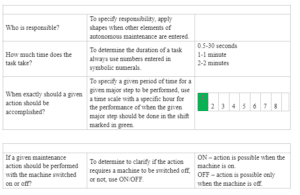
Legend of SOP TPM
TWI Trainings in TPM AM
An essential component of TPM AM is effective training, where the Training Within Industry (TWI) Job Instructions model plays a crucial role.
Understanding TWI Job Instructions
TWI Job Instructions is a structured method designed to help supervisors and team leaders in effectively training new or less experienced employees. This methodology is particularly relevant in TPM AM as it ensures that the workforce is proficient in carrying out maintenance tasks correctly and safely. The TWI method is built around a four-step process:
- Prepare the Worker: This involves setting the stage for learning by putting the worker at ease, explaining the importance of the job, and ensuring they are ready and willing to learn.
- Present the Operation: The trainer demonstrates the task, breaking it down into manageable steps, while clearly explaining each part of the process. This step focuses on the key points and reasons for each part of the job.
- Try Out Performance: Here, the learner performs the task under supervision, mimicking the steps shown by the trainer. This step is crucial for hands-on learning and reinforcing the training.
- Follow-Up: This final step involves the trainer providing feedback, correcting mistakes, and gradually allowing the learner to perform the task independently.
Applying TWI Job Instructions in TPM AM
- Developing Skills for Autonomous Maintenance: Use TWI Job Instructions actively to train operators in routine maintenance tasks. This approach empowers them with essential skills for autonomous maintenance, aligning with the core principles of TPM.
- Standardizing Maintenance Procedures: Implement TWI to ensure that organizations perform maintenance tasks consistently and in line with best practices. This standardization improves machine reliability and extends equipment lifespan.
- Enhancing Safety and Efficiency: Through proper TWI training, create a safer working environment by equipping workers with the necessary skills to handle machinery and equipment effectively. This initiative not only enhances safety but also boosts overall efficiency and productivity.
- Fostering Continuous Improvement: Leverage TWI’s structured training approach to lay the groundwork for continuous improvement in maintenance processes. Encourage skilled workers to actively identify and suggest improvements in their daily tasks.
Conclusion
The implementation of Standardized Work Instructions (SWIs) or Standard Operating Procedures (SOPs) in TPM AM is a critical element for enhancing productivity and efficiency in production processes. The significance of SWIs lies in their detailed description of operational methods, guiding operators in performing specific tasks effectively. These instructions are universally applicable across various production environments, provided they involve human labor.
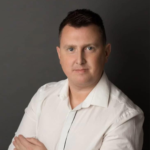
Dr. Bartosz Misiurek is a co-founder of a few start-ups like Leantrix, Lean Community, Leancoin, etwi, Lean Global Consulting, Sallar. He is a CEO at LeanTrix Ltd., Leancoin Ltd, Do Lean IT OU, and a Member of the Board at Astral Hodling OU. Author of the book “Standardized Work with TWI: Eliminating Human Errors in Production and Service Processes.” He works as Sr Manager and TWI Global Coach at Automotive Company.