Lean leadership in quality improvement. Elimination of Waste and Improvement in the Quality Department. Everyone is a LEAN Leader. For over seven years, I have been working in the quality department and have had the pleasure of managing a team responsible for a large group of clients, a huge number of suppliers, laboratories, and system-related matters.
Table of Contents
ToggleThe Role of Quality Department and Lean Leadership
The quality department alone does not create quality in a company, so we collaborate with everyone daily. It’s a very interesting and absorbing job: to be on the front line of battle. However, before becoming the Director of Quality, I was incredibly fortunate to manage projects, lead the production department, and be responsible for developing and implementing LEAN strategies. This experience has been immensely valuable. I am certain that without this gradual development, I would not view quality the way I do now.
Understanding Customer Needs and Expectations
Firstly: Identifying the customer and what is important for the customer. It is not always as we think. A good understanding of the problem, the process, and the customer’s expectations allows us to optimally organize our process – not everyone in organizations remembers this.
Emphasizing Business and Customer Value
Secondly: Focus on value. In our actions, we cannot forget what is important. Very often, we try to please the customer at all costs. If we do this without a good understanding of their needs and forget about the BUSINESS in the process, we achieve our short-term goals (complaint resolved, quality problem solved), but the important thing (BUSINESS) suffers – in my opinion, this is a common mistake made by quality departments.
Adopting a Lean Leadership Approach Beyond Production
Thirdly: Lean approach to work. Yes, yes – LEAN is not just for production. Let’s not forget about the three basic types of waste: Muda, Mura, Muri. Improving our organizations is a continuous process. Also, and I emphasize this especially based on my experience, in processes that to this day think: “Lean is for those in production”. Every day I see how many unused opportunities lie in non-production processes. And not just small ones. Ones bringing hundreds of thousands in savings: finance, logistics, HR, IT – these are the low-hanging fruits. Let’s remember to ensure our teams know the company’s goals, its Mission Vision, and our jointly developed strategy on a daily basis. So that we don’t lose sight of the fundamental objectives of our actions.
Fostering Team Development and Excellence
Fourthly: Development and improvement of the team. Our strength is our team. We must focus our activities on them. It is thanks to our people that we will achieve our set goals – of course, if we give them enough attention to understand what we are aiming for, to identify with the goals set/worked out, for their knowledge and competencies to constantly grow, for the roles they play in our processes to match their abilities, and for their motivation to always be at the highest possible level. Each of us is a LEAN Leader – each of us should be a LEAN leader.
Conclusions
Lean leadership in quality improvement is a holistic approach that transcends departmental boundaries. It requires a deep understanding of customer needs, a balanced perspective on business and customer value, a commitment to Lean principles throughout the organization, and a relentless focus on team development. Each of us has the potential to be a Lean leader, and by embracing these principles, we can drive lasting improvement and excellence in our organizations.
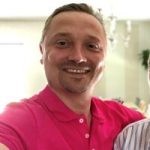
Boguslaw is certified Lean Six Sigma Black Belt. Responsible for implementing Lean Culture in the organizations, starting from 5S program, changes in the Operating System, and growth in Problem Solving Tools. He is a Lean Practitioner with over 20 years of experience in different industries.