TWI in Mixed Production. The Training Within Industry (TWI) program is one of the most popular approaches to developing the skills of experienced operators and leaders in instructing, improving and problem-solving. One TWI method is TWI Job Instruction (JI), which is focused on conducting on-the-job training. This method is aimed at reducing the root causes of human errors, which include the following:
- Poor or no operator training
- Poorly prepared work standards that are not observed by operators
- A lack of control and audit systems for operators after trainings
Table of Contents
ToggleTWI JI as a method to improve the processes
Many companies use TWI JI to standardize their processes. For example, according to data presented at the Conference, at the European division of Cooper Standard Automotive, all the plants that took part in the implementation of the TWI program in the first wave increased productivity by an average of 17.55 percent and reduced the level of deficiencies by an average of 35.83 percent.
The TWI JI method was mainly created to train employees in repetitive operations. However, the nature of production has changed, and there is a growing number of mixed model productions where the operator performs a number of different operations during his or her shift. The question now is how to standardize operations when there are, for example, 150 different references.
The answer is to list several leading product groups. For example, when we prepare a warm beverage, there may be two types of product groups: coffee and tea. These product groups can be prepared in many ways; these preparation methods are called references:
In the case of multi-variant production, a job breakdown sheet (JBS) should be prepared for each product group. A JBS is a tool for an instructor to use during on-the-job training and contributes to TWI work instructions. The JBS divides work into three categories:
- Major steps: logical segments of the operation in which something happens to advance the work
- Key points: anything that might make or break the job, injure the worker, or make the job easier to do
- Reasons for each key point
This table presents the JBS for the operation of preparing coffee:
TWI in Mixed Production. Instructors should use a JBS for the specific product group when discussing the work during instruction. When they explain the major steps and key points, they should have the work instructions in hand. In the third major step of preparing a weak coffee with milk, for example, they should specify, based on the work instructions, that one flat teaspoon of coffee should be added. Similarly, when discussing the fifth major step, they should refer to the work instructions and tell learners that they should add milk to about 1 centimeter from the top of the cup. Each reference for a JBS should be accompanied by work instructions; in fact, the automotive industry requires them. Some of these instructions are very similar (e.g., preparing weak coffee with milk and preparing medium-strong coffee with milk).
Sumarry
This approach can be used in any process where multi-variant production exists. Many companies implement a lean management approach to reduce one of the most dangerous wastes: overproduction. The TWI approach to work standardization will translate into the elimination of human errors, which will in turn affect all key performance indicators.
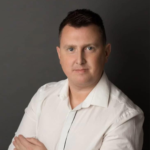
Dr. Bartosz Misiurek is a co-founder of a few start-ups like Leantrix, Lean Community, Leancoin, etwi, Lean Global Consulting, Sallar. He is a CEO at LeanTrix Ltd., Leancoin Ltd, Do Lean IT OU, and a Member of the Board at Astral Hodling OU. Author of the book “Standardized Work with TWI: Eliminating Human Errors in Production and Service Processes.” He works as Sr Manager and TWI Global Coach at Automotive Company.