The Kaizen Meaning and TWI Methods. Kaizen meaning video will show you how to use the Kaizen method to improve your work instruction and quality. The relation with the TWI Job method is explained, too.
In today’s competitive business landscape, organizations are constantly seeking ways to improve productivity, enhance quality, and foster a culture of continuous improvement. Two powerful methodologies that contribute to achieving these goals are Kaizen and Training Within Industry (TWI). In this article, we will explore the meaning of Kaizen and delve into the impact of TWI methods on driving organizational excellence.
Kaizen Meaning:
Kaizen, a Japanese term meaning “change for the better” or “continuous improvement,” is a philosophy rooted in the belief that small, incremental changes can lead to significant improvements over time. It emphasizes a proactive approach to problem-solving and encourages every individual within an organization to contribute to the improvement process. Kaizen fosters a culture of empowerment, teamwork, and relentless pursuit of excellence.
TWI Methods:
Training Within Industry (TWI) is a set of proven methods developed during World War II to address workforce training needs. TWI consists of three key modules: Job Instruction (JI), Job Relations (JR), and Job Methods (JM).
Job Instruction (JI):
JI focuses on effective training methods to ensure standardized work procedures. It provides supervisors with a structured approach to train employees by breaking down tasks into key steps, emphasizing hands-on learning, and promoting active participation. JI aims to reduce variability and ensure consistent performance across the workforce.
Job Relations (JR):
JR focuses on building positive relationships between supervisors and employees. It provides supervisors with skills to address conflicts, improve communication, and foster a supportive work environment. By nurturing strong relationships, JR enhances teamwork, morale, and overall employee engagement.
Job Methods (JM):
JM aims to improve processes and eliminate waste through systematic analysis and improvement. It trains supervisors to analyze work methods, identify inefficiencies, and develop more efficient and effective processes. JM promotes the use of data-driven decision-making, encourages employee involvement in process improvement, and drives continuous improvement efforts.
Impact of TWI on Kaizen:
TWI methods provide a solid foundation for implementing Kaizen principles within an organization. By training supervisors in effective instruction, communication, and problem-solving techniques, TWI empowers them to become effective change agents and champions of continuous improvement. TWI methods support the Kaizen mindset by promoting standardized work, fostering positive relationships, and enabling process improvement.
When TWI and Kaizen are integrated, organizations experience numerous benefits, including increased productivity, enhanced quality, reduced waste, improved employee engagement, and a culture of continuous improvement. By combining the power of TWI methods with the philosophy of Kaizen, organizations create a framework that drives sustainable growth and competitive advantage.
Conclusion:
Kaizen and TWI methods are powerful tools that can transform organizations by fostering a culture of continuous improvement, empowering employees, and driving operational excellence. Kaizen encourages individuals to embrace the mindset of continuous improvement, while TWI provides the practical methods and skills necessary to implement change effectively. By combining these methodologies, organizations can unlock their full potential, adapt to changing market dynamics, and stay ahead in today’s dynamic business environment.
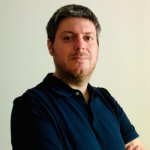
Andrea Manti is CBDO at Lean Community. He has over 15 years of experience in Lean Management. He is an expert in Lean and Quality Management and has held positions working as a Process Engineer, Customer Quality representative, Quality System Manager (IATF standard), and Continuous Improvement Senior Manager. During his career, Andrea has led the implementation of several Lean/6Sigma projects, TPM workshops, and TWI activities. He is also an expert in the World Class Manufacturing (WCM) program
During my 20 years of experience as a Lean Expert and Trainer, I have seen many Lean Journey … some of them failed but some of them brought people and companies to incredible results. I always liked to teach others and I am happy when they have success.
This is the reason why I started in 2010 with my first website on Lean and by continuous improvement, I decided to found LeanVlog.