The Training Within Industry (TWI) program, developed during World War II, was designed to build essential skills for foremen and production leaders. Although much has changed since then, this approach still delivers valuable results in both training and improving production processes. To fully realize the potential of this program, companies need to implement it comprehensively, not just focus on creating work instructions. It’s crucial to understand that this method involves much more than documenting procedures.
Table of Contents
ToggleTWI Program and Work Instructions
Many organizations mistakenly view work instructions as the core aspect of employee development under this framework. This leads to the belief that merely creating documentation ensures successful training. This situation mirrors the common misunderstanding of the 5S method, where employees tend to focus only on tidying workspaces rather than increasing efficiency. Success in both 5S and TWI depends on integrating these practices into daily operations.
Relying solely on documentation without applying it effectively in training often results in suboptimal outcomes. Employees may not understand why instructions need regular updates, which can lead to disengagement. As a result, the overall program loses its value and fails to deliver the expected results.
A Holistic Approach to the TWI Program
This program offers much more than simply creating manuals. It incorporates several important components that, together, provide a foundation for effective training and process management. Initially, the program focused on three key areas:
- TWI Job Instruction – Teaching leaders how to pass on knowledge efficiently and document processes.
- TWI Job Methods – Optimizing workflows by reducing inefficiencies.
- TWI Job Relations – Fostering team engagement and resolving conflicts.
To maximize the program’s benefits, companies need to adopt all of these elements, not just one.
Evolving to Meet Modern Workplace Challenges
Over time, the framework expanded to include two additional areas, which enhanced its effectiveness and scope:
- TWI Job Safety – Ensuring leaders create safe working environments.
- TWI Problem Solving – Addressing issues at their source to prevent recurrence.
These additions transformed the program into a comprehensive leadership tool, helping organizations not only train employees but also improve workplace safety and production processes.
Implementing a Comprehensive Strategy for Success
For the training program to achieve the best results, organizations must adopt a holistic implementation approach. Focusing on just one aspect, such as work instructions, won’t yield long-lasting improvements. A well-rounded strategy that develops leadership skills across all levels of the organization is essential for unlocking the full potential of this system. Engagement from the entire team is key to long-term success.
In conclusion, this program is far more than a tool for documenting procedures. It serves as a comprehensive strategy for developing competencies, streamlining processes, and building teams that are engaged in their work and prepared to tackle challenges effectively.
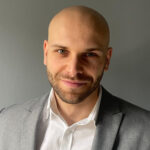
He is a Senior Consultant of the TWI program and Lean Management at LeanTrix. He is also a leader in the startup project - etwi system. He was a member of a global team that implemented the TPM system for several automotive plants in Europe, Asia, South America and North America.