Fault reporting system – is it worth it? In the previous article, I described my experiences related to implementing autonomous maintenance of machines and equipment. I also referred to the fault reporting system. In this short article, I would like to explain in more detail what a fault is for me, and what a failure is. I will try to convince you to implement, and earlier to create, your own fault reporting system.
Table of Contents
ToggleFault or Failure – Definitions
The definitions describe a fault in a clear way. A fault is damage to a machine or device that does not stop its operation, but over time leads to a stoppage, i.e., a failure. A very important, breakthrough moment are the first TPM/AM workshops.
Mechanical Faults – These are visible mechanical damages to equipment. These could be damages to the insulation of wires, visible cracks in machine components that do not stop the machine. Cracked operator display screens of machine controls, but still functioning. Mechanical faults include visible wear of wedges in multi-groove belts or leaks from transmissions.
Unusual Device Operation – In this category, any audible air leaks, louder operation of transmissions, motors, or bearings can be classified. Belts slipping on gear wheels still work, but the effect is slower machine operation, or defects in products. Any vibrations of machine components are also a fault.
Short Stops – also called micro downtimes. They are not yet classified in many companies as failures, but effectively lower the technical availability of the machinery park. Short stops, which must be eliminated by a “quick reset”, result in many minutes of unregistered stops per day. Slower pump operation is also a fault. Weaker compressor operation is also a fault.
Other – In the category of “other”, I have experience where production workers reported in the fault reporting system all risks related to the safety of machine or equipment operation. Within this category of faults, we often also noted improperly functioning assembly stations or workstations in terms of broadly defined ergonomics.
A failure, on the other hand, is a state of machine stoppage. The machine does not perform its functions and is not capable of producing good quality products. A failure is also a state of the machine that endangers safety at work.
Fault Reporting System – Does It Make Sense
In many organizations where the presence of faults is not yet recognized, such stoppages and damages are not paid attention to. In monitored results, they are most often visible as a loss of performance. The unaware management team looking for reasons in the slower work of the team operating the machines or production line. As a result, there is demotivation of the team, as they are aware that the machines are not operating according to the set parameters and efficiency. Here it is very important to implement the TPM/AM and also implement a fault reporting system.
If we are not yet ready to start implementing TPM, I encourage you to use a fault reporting system. The value will be in recording faults, marking them on the machine or board and assigning responsibility for their removal – of course, I recommend monitoring with the PDCA cycle.
Below is a photo of the fault reporting system developed in cooperation between production and maintenance departments. I particularly emphasize the importance of involving machine and production line workers as well as reactive and preventive maintenance in creating the system. A system invented by engineers or lean specialists and “delivered” to production will not be adopted.
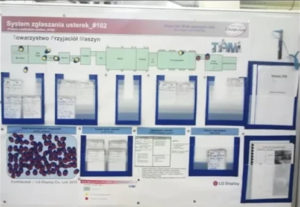
Pic.1
Types of Fault Reporting Systems
There are many ready-made IT solutions on the market to support maintenance and production departments. Of course, you can buy and run such a system. However, I recommend starting by creating a system with the team, on paper, and then moving the plan onto a board and beyond the value of using the system, there is also a lot of “fun” and joy. IT systems such as CMMS also have their advantages. Especially if faults, failures, and preventive maintenance of machines and equipment are managed in one program. In CMMS-type programs, you can quickly and easily report a fault and mark its priority or the person to remove it. You can also monitor the state of the spare parts warehouse in one system.
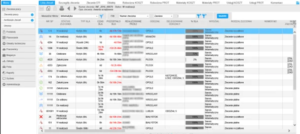
Pic.2
Summary
Fault reporting system – is it worth it? The choice of system depends on you and the current situation in the organization. One thing is certain, reporting faults is fundamental to proper PM, to reducing the number of failures and, in my opinion, most importantly, is the basis for building relationships between production workers and the machine or equipment. This system will reduce the indifference of production workers to the symptoms of faults or upcoming failures. Over time, the number of reported faults will decrease, and the failure rate will also decrease.
Senior Production Manager | Zgodniezprocesem.pl | Lean Consultant | Lean Enthusiast