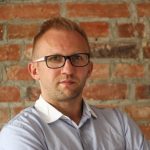
I was lucky that everything I learned about Lean, Kaizen, or production optimization started in a Japanese company. There, under the supervision of Japanese staff and during training in Japan, I learned how to approach the Continuous Improvement process. Over time, I also learned about other practices in other companies.
Library filter
SMED – Initial Setup Selection Strategy
SMED – initial setup selection strategy. Have you decided on SMED Workshops…
Read moreTPM – New Jobs and Duties
New roles in TPM. When implementing TPM and thus improving machine park…
Read moreImplementing Planned Maintenance
Implementing planned maintenance. Can Planned Maintenance be implemented by sheer willpower alone?…
Read moreImproving OEE: 10 Breakdown Insights
Improving OEE: 10 Breakdown Insights. Interested in improving OEE and reducing downtime?…
Read moreCalm down – it’s “ONLY” 5 minutes!
Calm down, it’s “ONLY” 5 minutes! Is 5 minutes of machine downtime…
Read moreBrainstorming Meaning
Brainstorming meaning. How often do you use brainstorming to solve daily production…
Read moreWhat you shouldn’t say?
What shouldn’t you say? Specifically, are there things you should avoid saying…
Read moreImprove OEE – 10 post-failure questions
Improve OEE and reducie failure rates? Ask yourself 10 simple questions and…
Read moreTPM Lean – Use Your 5 Senses
TPM in Lean is the cyclical and preventive replacement of parts and…
Read more