To implement standard work, it is essential to have work instructions. In this video, we explain how to create instructions effectively and efficiently using the basics of training within the industry. Implementing standard work in any industry requires clear and comprehensive work instructions. These instructions serve as a valuable resource for training employees and ensuring consistent, efficient processes. In this article, we will delve into the key aspects of creating effective and efficient work instructions by utilizing the fundamentals of training.
Table of Contents
ToggleImportance of Standard Workd
Standard work instructions provide a foundation for uniformity and consistency in performing tasks. They serve as a reference guide for employees, enabling them to understand the correct sequence of steps, tools to be used, quality standards to meet, and safety precautions to follow. By establishing clear instructions, organizations can streamline their operations, minimize errors, and optimize productivity. Before creating work instructions, it is crucial to identify the training needs of employees. Assess the skills and knowledge required to perform tasks effectively. This analysis helps determine the scope and level of detail needed in the work instructions. Consider the experience level of the trainees, the complexity of the tasks, and any specific requirements or regulations. In the movie below we present how standard work and work instructions are linked with the Training Within Industry program.
Structuring Standard Work
In Training Within Industry (TWI) Job Instruction (JI), preparing a standard involves a meticulous process of breaking down a job into its fundamental elements. This process is integral to TWI’s effectiveness and focuses on three primary components: important steps, key points, and reasons for key points. Below is presented a standard work for the operation of tying the underwriter`s knot. The SOP was prepared in the etwi software for digitalization of SOPs.
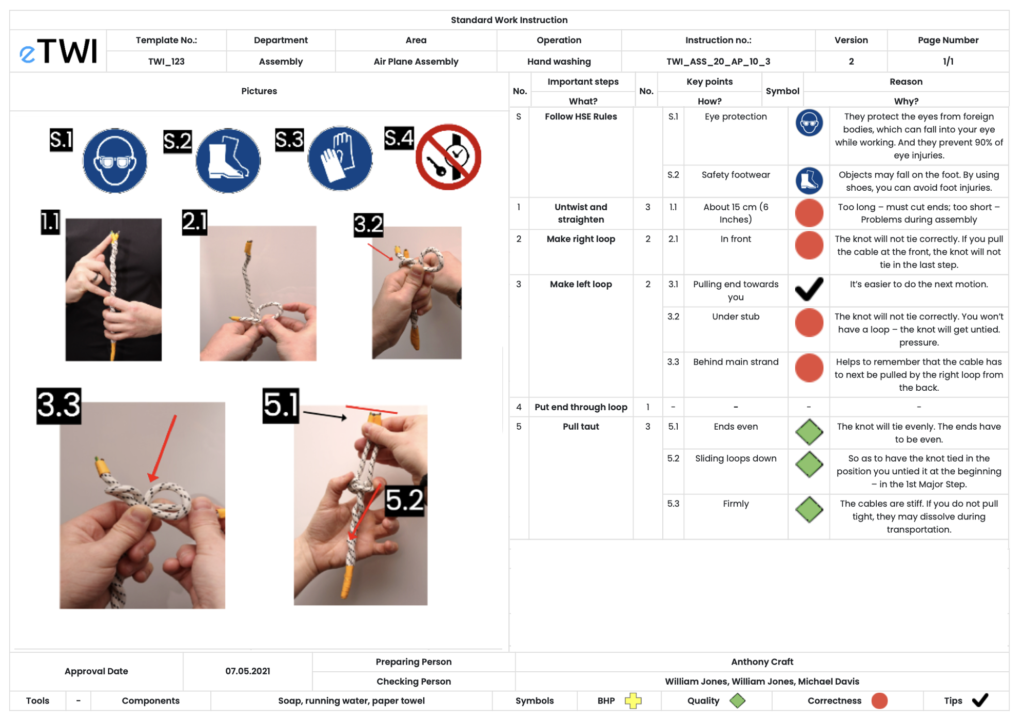
Standard Work – example from https://etwi.io/
Important Steps
Important steps are the backbone of any job standard in TWI JI. These steps represent the core sequence of actions required to complete a task. The preparation of these steps involves:
- Identification: The first step is to observe the job in action and list down all the tasks involved from start to finish. This includes every action the worker must take to complete the job.
- Sequencing: After identifying all the actions, they are arranged in a logical sequence. This sequence should reflect the most efficient and safe order to perform the job.
- Simplification: The steps are then reviewed to eliminate any unnecessary actions or complexities. The goal is to simplify the job as much as possible without compromising on quality or safety.
Key Points
Key points are the critical elements within each important step that make a difference in how the job is done. They are vital for ensuring quality, safety, and efficiency. Identifying key points involves:
- Differentiation: Distinguishing between regular steps and those that require special attention due to their complexity, potential for error, or impact on the outcome.
- Highlighting: Highlighting these key points so that they stand out in the job instruction. This ensures that the worker pays extra attention to these critical aspects of the job.
- Detailing: Providing detailed descriptions of each key point. This includes specific actions, positions, tools, or techniques that are necessary to execute the step correctly.
Reasons for Key Points
The reasons for key points are explanations as to why these aspects of the job are crucial. They provide the worker with an understanding of the importance of each key point, which is essential for ensuring compliance and quality. The process includes:
- Rationale Explanation: For each key point, a clear rationale is provided. This could be related to safety (to prevent injury), quality (to ensure the product is made correctly), or efficiency (to save time or resources).
- Contextualization: The reasons are contextualized within the broader scope of the job or the final product. This helps workers understand the impact of their actions on the overall process or product.
- Reinforcement: Regular reinforcement of these reasons during training and in practice. Understanding the ‘why’ behind actions ensures deeper engagement and adherence to the standards.
Incorporating Training Techniques – TWI Job Instructions
The Training Within Industry (TWI) program, particularly its Job Instructions component, provides a structured approach to training that can significantly enhance the effectiveness of work instructions. To fully leverage this approach, it is crucial to incorporate varied training techniques that cater to different learning styles. This chapter delves into how training according to TWI Job Instructions can be optimized by integrating diverse learning methods.
Understanding TWI Job Instructions and Standard Work
TWI Job Instructions is focused on delivering effective on-the-job training. It emphasizes breaking down a job into precise steps, explaining each step clearly, demonstrating it, and then letting the trainee perform the step. This method ensures that the trainee not only understands each step but also gets hands-on experience under close supervision. Important is to catering to different learning styles.
Visual Learners
For employees who learn best through visual means, incorporating diagrams, flowcharts, and visual aids into work instructions is beneficial. Demonstrations, videos, and illustrated step-by-step guides can significantly enhance their understanding and retention of the job instructions.
Auditory Learners
For those who absorb information better through listening, oral explanations and discussions are key. During training, the trainer should focus on explaining the rationale behind each step, and encourage questions and interactions. Audio recordings of instructions can also be an effective tool for auditory learners.
Kinesthetic Learners
Employees who are kinesthetic learners benefit most from hands-on experience. In line with TWI’s emphasis on demonstrating and performing job steps, these learners should be given ample opportunities to practice the tasks under supervision. Interactive simulations and real-life practice scenarios are particularly effective for this group.
Practical Exercises and Interactive Elements
Incorporating practical exercises is a cornerstone of the TWI Job Instructions approach. Trainees should be given tasks that mimic real job situations. These exercises not only reinforce learning but also build confidence. Interactive elements like role-playing, group discussions, and problem-solving exercises can further engage trainees, making the learning process more dynamic and effective.
Regular Reviews and Updates of Standard Work
To maintain the relevance and effectiveness of work instructions, regular reviews and updates are essential. Feedback from trainees and trainers should be actively sought and used to refine the training materials. This process ensures that the work instructions stay current with evolving best practices and technological advancements. It also allows for continuous improvement in the training methodology itself.
Emphasizing Safety and Quality in Work Standard
Work instructions and work standards should place a strong emphasis on safety protocols and quality standards. Clearly outline any potential hazards or risks associated with the task and provide step-by-step instructions on how to mitigate them. Specify quality checkpoints and indicators to ensure that employees produce consistent and high-quality outputs. Reinforce the importance of following safety guidelines and meeting quality requirements throughout the work instructions.
Standard work instructions are invaluable tools for training employees and establishing efficient processes within an organization. By creating clear and comprehensive instructions, organizations can ensure consistency, minimize errors, and optimize productivity. Incorporating training techniques, emphasizing safety, and addressing quality standards are crucial elements to consider while developing these instructions. By embracing the fundamentals of training, businesses can empower their employees and foster a culture of continuous improvement.
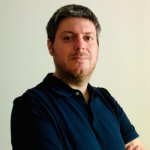
Andrea Manti is CBDO at Lean Community. He has over 15 years of experience in Lean Management. He is an expert in Lean and Quality Management and has held positions working as a Process Engineer, Customer Quality representative, Quality System Manager (IATF standard), and Continuous Improvement Senior Manager. During his career, Andrea has led the implementation of several Lean/6Sigma projects, TPM workshops, and TWI activities. He is also an expert in the World Class Manufacturing (WCM) program
During my 20 years of experience as a Lean Expert and Trainer, I have seen many Lean Journey … some of them failed but some of them brought people and companies to incredible results. I always liked to teach others and I am happy when they have success.
This is the reason why I started in 2010 with my first website on Lean and by continuous improvement, I decided to found LeanVlog.