What shouldn’t you say? Specifically, are there things you should avoid saying to your boss? And if there are, what are they? It’s not that bosses don’t want to listen to their employees. At least the conscious ones with an open mind who listen to their employees. They listen because they know that amidst the sea of information, they can extract valuable insights that will help them manage and solve daily problems on the Genba.
However, there are things that are worth not saying even to the most open and calm boss under the sun. Here are a few of them:
1. “No. It can’t be done.” – When things are critical, there are many people around the leader who say, “It can’t be done,” “I knew it would be like this,” and so on. The truth is, in such moments, every leader values people who have ideas on how to overcome the situation. No matter how crazy the plan is, it’s still a plan to get out of trouble. In such a situation, the boss wants to hear what the problem is and what the realistic proposed solution is.
CASE: “Boss, with this feed rate, we won’t achieve the specified tolerance on the drawing. We’re producing defects (NOK). I suggest reducing the feed rate to 80%. We’ll produce less, but in accordance with the drawing and without any quality losses.”
2. “I don’t even know how to do it.” – You have the right not to know how to perform a given task, especially if you’re doing it for the first time. Despite your sincere efforts, the trial and error method may not always be the best solution. Instead of seeking justification in your lack of knowledge, it’s much better to escalate the problem to your supervisor, clearly stating the issue. This information should be concise and specific: “I don’t have the tools, equipment, instructions, or appropriate programs.”
CASE: “Tom, at the moment, I have no idea how to attach this. Call Piotrek, maybe we can come up with something together. I’m convinced that together we’ll figure something out.”
3. “It worked better in my previous company.” – Perhaps it did. Instead of openly criticizing the current state of affairs, become an impetus for positive changes. Act according to KAIZEN principles. If you see that certain things or processes could function better and you have an idea of how to approach them, suggest a solution instead of lamenting about how things are currently going wrong.
CASE: “Boss, currently we waste a lot of time transferring tools during changeovers. On average, we lose 10 minutes on that. In my previous company, we used carts for changeovers with pre-prepared tools. Maybe such a solution would make sense for us too? What does the boss think about trying it during the next changeover?”
4. “It’s not my problem.” – I don’t know any production process without problems. They can be big or small, but they alwayshave a tendency to pile up. If “it” is not your problem, and you openly start communicating that, it becomes your supervisor’s problem. By definition, unresolved problems don’t disappear; they accumulate. Therefore, when your employer entrusts you with solving a particular problem, they expect you to show commitment and put in some effort to resolve it. Saying “It’s not my problem” also suggests that you’re not interested in collaboratively solving problems and striving for the department’s or company’s success.
CASE: If someone asks you to work on a specific problem, you have the right to request the necessary support: time to work on it, relevant data, or a team with whom you can tackle the challenge and find a solution together.
5. “Do we really have to do this?” – If someone has assigned you a task, it probably has some purpose. Questioning whether a certain task needs to be done implies that the assigner is allocating tasks that are not justified from the company’s perspective. It might be better to rephrase the question and inquire about the purpose of the task. What does it contribute to the organization, the customer, or the employees?
6. “It has always been done this way, and it was fine.” – Come on. There was a time when cars had two-stroke engines, and that was fine? Change is a natural part of our lives. Cars, phones, and the conditions of our work all change. If people around you want to introduce certain changes in the organization, help them. Your opinion and guidance will certainly be useful and helpful to them. It’s a WIN-WIN situation. You become someone who can share knowledge, and your colleagues gain a leader of change.
7. “Often, a lot, long, always” – Using generic language is something I strongly discourage. We all know that there are many problems on the production floor that require action. However, describing them with generics does not bring anyone closer to solving them, not even one step. During discussions on production, Kaizen workshops, or other meetings, it’s often heard phrases like “a lot,” “many,” “always,” etc. Such information is not informative; rather, it misinforms.
CASE: Instead of using vague descriptions, like a machine often breaking down, try to quantify how much time we lose per month due to that type of failure. And it’s better to provide the number or, ideally, percentages when referring to a high number of quality defects. Such measurable data help decision-makers take appropriate steps to solve the problem.
What you shouldn’t say? The mentioned seven “phrases” certainly don’t cover all communication problems that can arise during the execution of production processes. There are definitely more of them, but these seven occur surprisingly frequently in many organizations. What would you add to the list of seven things you shouldn’t say to your boss?
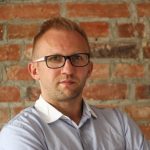
I was lucky that everything I learned about Lean, Kaizen, or production optimization started in a Japanese company. There, under the supervision of Japanese staff and during training in Japan, I learned how to approach the Continuous Improvement process. Over time, I also learned about other practices in other companies.