New roles in TPM. When implementing TPM and thus improving machine park efficiency, we also decide to change existing duties for many people. It’s important to be aware that both the operator and the mechanic will have new tasks, duties, responsibilities, and rights. Lack of awareness about new roles and not properly introducing them to the TPM team will lead to conflicts between teams. We will waste energy and time solving team problems instead of working as a team. So, what are these new roles? Let’s start with the Maintenance Department:
Table of Contents
ToggleEnhancing Maintenance Strategies
- Failure analysis and improvement actions. No more “from failure to failure” approach. After a failure, a simple analysis of the incident must be done and lessons learned for the future. A failure is now an opportunity for improvement, a trigger for Kaizen actions.
- Developing a Maintenance Action Plan (Preventive + Reactive). If we don’t want to operate from failure to failure, tasks like component replacements, reviews, and lubrication management must be regularly planned and implemented.
- Role of production in Preventive Maintenance. Its role is not just cleaning machines. It includes INSPECTION through cleaning and detecting anomalies.
- Creating One Point Lesson (OPL). This is knowledge transfer from Maintenance to Production. Initially, Maintenance should create instructions for simple tasks with lots of pictures and easy language.
- Teacher role. Creating OPL is just the first step in knowledge transfer. Proper training in practical implementation is essential, followed by knowledge transfer within the Production Department. Maintenance technicians should ensure standards are maintained and provide support.
In TPM, not only Maintenance but also operators have new roles:
- Conducting INSPECTIONS. A key task in TPM, allowing operators to detect most damages and malfunctions.
- Minor adjustments and repairs based on OPL. Operators expand their knowledge about machine functioning. Any adjustments and repairs should be based on verified OPLs.
- Participation in dealing with failures. This helps operators understand machine construction, functioning, and failure causes.
- Initiating corrective actions. Awareness of failure causes and effects, and simple communication, lead to the development of Improvement Maintenance.
Quality Enhancement through TPM
For the Quality Department, new tasks include:
- Indicating key points for machine quality. Sharing knowledge about machine-quality relationships, like FMEA analysis findings.
- Responding to current quality issues. Initiating TPM actions for both Maintenance and Production when quality issues arise.
- Improvement Maintenance for quality. Quality engineers should initiate Kaizen actions to prevent defects.
Fostering Team Collaboration
A new role for all parties: Collaboration and communication. When there is a “problem”, it’s important to communicate and cooperate to solve it together. TPM is not just about improving the efficiency of the Maintenance Department; it’s about improving the efficiency of the entire organization.
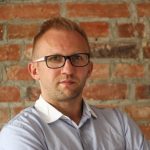
I was lucky that everything I learned about Lean, Kaizen, or production optimization started in a Japanese company. There, under the supervision of Japanese staff and during training in Japan, I learned how to approach the Continuous Improvement process. Over time, I also learned about other practices in other companies.