The role of Leader in Lean. A common response to the question, “Who is responsible for continuous improvement?” is: everyone. Theoretically, all employees should contribute to process improvements, just as they should contribute to workplace safety. However, in reality, continuous improvement often falls under the responsibility of a dedicated Lean Specialist or Lean Manager, much like safety is handled by a Health & Safety Coordinator.
When improvement opportunities arise, the typical reaction is:
- Operators expect supervisors to take care of it.
- Supervisors delegate it to the Lean department.
- The Lean department attempts to drive improvements, often encountering resistance.
While Lean is meant to be a shared responsibility, in practice, it functions as a separate department, leading to organizational silos instead of full integration.
Table of Contents
ToggleA Typical Plant Structure and the Lean Specialist’s Role
In most manufacturing plants, the leadership structure follows a common hierarchy.
At the top is Tomek, the Plant Manager. Reporting to him are:
- Monika , HR Director, responsible for talent management and workforce development.
- Marek, Production Manager, focused on production efficiency and output.
- Tomek, Lean Specialist, responsible for leading process optimization initiatives.
HR and production teams have additional staff to support their operations. HR includes recruitment and training specialists, while production managers oversee coordinators and team leaders.
The Lean Specialist, however, operates alone. Unlike other managers who have supporting teams, Wojtek is expected to “deliver Lean” across the plant without a dedicated workforce.
The Responsibilities of a Lean Specialist
Wojtek’s role is clearly defined with measurable targets:
- Conduct three KAIZEN workshops per month.
- Report the results of 5S audits and drive corrective actions.
- Track and analyze employee participation in KAIZEN initiatives.
- Report Lean savings to CORTIM and ensure annual cost-reduction targets are met.
While these goals appear structured, they become challenging to implement due to operational realities.
The Reality – How Silos Are Created
When Wojtek attempts to execute improvement initiatives, he faces obstacles.
- The Production Manager, Marek, says:
“I can’t free up my team for KAIZEN workshops right now. We need to focus on production.” - The Production Coordinator says:
“If you want to implement 5S improvements, do it yourself – we don’t have time.” - The HR Director, Monika, requests reports but adds:
“Operators are frustrated because they submit many improvement ideas, but only a few are implemented, which affects their bonuses.” - The Plant Manager, Tomek, pressures for results:
“We are 20% behind our Lean savings target. Speed up KAIZEN and collect more improvement ideas from operators.”
In this system, the Lean Specialist becomes isolated.
Everyone expects improvement results, yet no one wants to dedicate the necessary time or resources.
Two Organizational Silos
This structure unintentionally leads to two disconnected silos:
- The Lean Silo, where Wojtek is responsible for process improvement.
- The Production Silo, where Marek is focused on maximizing output.
The challenge is clear – production teams prioritize efficiency and delivery, while Lean struggles to integrate its initiatives.
A Historical Perspective – The Role of Leader
This separation of responsibilities was not always the norm.
In the 1940s, when large-scale manufacturing was expanding in the United States, leaders were naturally responsible for process improvements.
The Training Within Industry (TWI) program was developed to build leadership skills in four critical areas:
- Job Instruction (TWI JI) – Training employees on standardized work methods.
- Job Methods (TWI JM) – Improving work processes for efficiency.
- Job Relations (TWI JR) – Managing team dynamics and collaboration.
- Job Safety (TWI JS) – Ensuring workplace safety.
At the time, frontline leaders owned the responsibility for:
- Training their employees effectively.
- Continuously improving work processes in their areas.
- Resolving workplace conflicts to maintain productivity.
- Enforcing safety standards to protect workers.
Over time, however, organizations began centralizing these responsibilities and creating specialized roles:
- Instead of training multiple leaders in Lean, a single Lean Specialist was appointed.
- Instead of making safety a shared responsibility, a dedicated Safety Coordinator was assigned.
The reasoning was simple – training one expert seemed easier than developing multiple frontline leaders in Lean methodology.
But was it more effective?
Reversing the Model – Lean as a Leadership Responsibility
A more effective approach would be to shift responsibility for Lean back to frontline leaders, with the Lean Specialist acting as a mentor rather than an implementer.
Imagine a scenario where leaders are responsible for their own Lean objectives, such as:
- Analyzing and improving a process using TWI Job Methods.
- Investigating performance drops using an A3 report.
- Encouraging and implementing KAIZEN suggestions from their teams.
- Creating standardized work instructions with TWI Job Instruction.
- Following up on 5S audit findings and corrective actions.
- Addressing safety compliance issues directly on the shop floor.
In this model, Lean is no longer a top-down initiative, but an integrated part of daily operations.
Leaders would proactively seek Lean support rather than waiting for the Lean Specialist to push initiatives.
Instead of Lean requesting production’s involvement, production requests Lean’s guidance.
The Game Changer – How AI Can Support The Role of Leader
In the past, this leadership-driven Lean model was difficult to sustain due to time constraints and knowledge gaps.
Today, however, Artificial Intelligence (AI) is changing the equation.
AI can support leaders by addressing three key challenges:
- Process Improvement – AI can analyze current workflows and suggest improvements, allowing leaders to focus on execution.
- Problem-Solving – AI can generate A3 reports, requiring only minimal input from leaders.
- Standardized Work Instructions – AI can draft TWI job instructions based on recorded steps and best practices.
With AI-driven insights, leaders can spend more time on execution rather than analysis.
The role of the leader is to capture the current state, while the role of AI is to analyze and generate improvement opportunities.
Conclusion – The Role of Leader
- Should Lean be the responsibility of just one person? No.
- Should leaders regain ownership of continuous improvement? Yes.
- Can AI help leaders become Lean experts? It already is.
At Leantrix, we are developing AI-driven tools that empower leaders to take ownership of Lean initiatives.
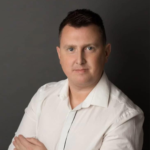
Dr. Bartosz Misiurek is a co-founder of a few start-ups like Leantrix, Lean Community, Leancoin, etwi, Lean Global Consulting, Sallar. He is a CEO at LeanTrix Ltd., Leancoin Ltd, Do Lean IT OU, and a Member of the Board at Astral Hodling OU. Author of the book “Standardized Work with TWI: Eliminating Human Errors in Production and Service Processes.” He works as Sr Manager and TWI Global Coach at Automotive Company.