SOP Software – this is our refreshed ranking for 2025, highlighting the best SOP software solutions for manufacturing based on Lean principles, process efficiency, and ease of adoption on the shop floor.
SOP software is fundamental in managing and maintaining efficiency and quality in production companies. They serve as a set of step-by-step instructions defined by an organization to help workers carry out routine operations. Standard Operating Procedures (SOPs) aim for efficiency, quality output, and uniformity of performance while reducing miscommunication and failure to comply with industry regulations.
The implementation of SOP software in an organization paves the way for a more structured and systematic approach to task execution. It facilitates the standardization of processes, making it easier for employees, regardless of their experience level, to understand and follow the necessary procedures.
Table of Contents
ToggleInsights from Toyota, Automotive, and TWI
Renowned manufacturing giants like Toyota and leading sectors like the Automotive industry have set high benchmarks in SOP practices. The Training Within Industry (TWI) program, widely adopted in these industries, emphasizes that the best SOPs clearly outline what to do, how to do it, why it is done, and often include visual aids like photos or diagrams to enhance understanding. Below is an example of an SOP prepared in etwi Software.
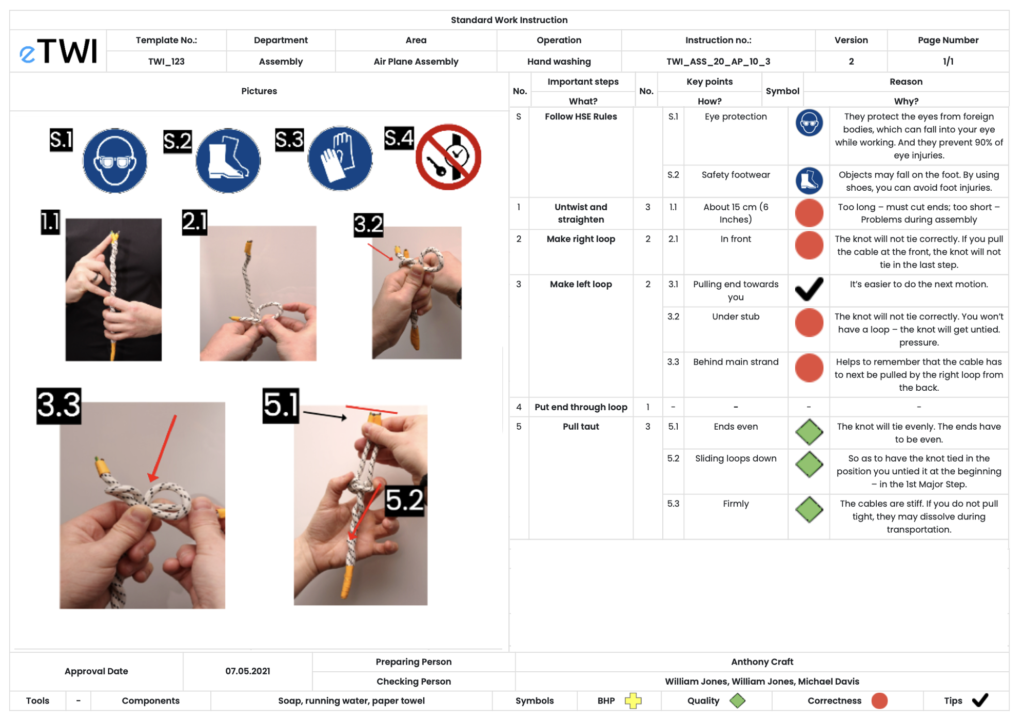
SOP Manufacturing Example prepared in etwi Software
The responsibility for creating and managing SOPs typically falls upon process engineers, quality assurance teams, and HSE managers within an organization. These individuals have a knowledge and understanding of the processes and regulations to develop effective SOPs. In larger organizations, a dedicated SOP team might be established, often working closely with department heads and frontline managers to ensure that SOPs are practical, clear, and comprehensible.
The Importance of Digitized SOPs
In today’s fast-changing manufacturing environment, digitized SOPs offer many advantages over traditional paper-based systems. These include easier access to instructions, improved compliance tracking, and the ability to quickly update procedures in response to process changes or new regulations. Digital SOPs improve operational efficiency, reduce errors, and ensure that best practices are consistently followed. SOP Softwares enhance the potential and opportunities for creating paperless workstations, where a production operator has direct access to digitized work instructions.
Introduction to Criteria for SOP Software
In this ranking, we primarily focused on analyzing software for creating Standard Operating Procedures (SOPs) and Work Instructions that align with the best practices of Lean Management. These practices originate from the automotive industry (notably Toyota and GM) and the Training Within Industry (TWI) program. Our aim was not to examine the technical sophistication of the systems but to assess how practically they can be used by companies for work standardization, employee instruction in line with best practices (e.g., instructor-led employee training), and improvement activities. We paid special attention to whether a given system is merely a task checklist or if it educates employees by illustrating underlying reasons and causes. We also considered how user-friendly each system is and its focus on creating SOPs and Work Instructions.
List of criteria for the Best SOP Software
Criteria considered in our analysis:
- Editability and Personalization of Document Templates: The ability to customize and edit document templates to suit specific needs.
- Version Control and Change History: Managing document revisions and tracking historical changes.
- Access Management and Permissions: Controlling who can view, edit, or share documents.
- Document Lifecycle Management: Overseeing the entire lifecycle of a document, from creation to archiving or deletion.
- Compliance with Industry Norms and Standards (e.g., TWI): Ensuring that the software adheres to recognized industry norms and standards.
- Ease of Communication and Collaboration: Facilitating effective communication and collaboration within the system.
- Integration with External Systems: Capability to integrate seamlessly with other enterprise systems.
- Automated Notifications and Alerts: Providing automated updates and alerts relevant to the documents or processes.
- Flexibility of Output Formats: Offering a range of formats for exporting or sharing the documentation.
- Intuitive User Interface: Ensuring the software is easy to navigate and use.
- Language Support: Providing multi-language support to cater to diverse user bases.
- System Accessibility: How accessible the system is to various users.
- Installation Methods of the System: How the system can be installed and deployed.
These features are assessed based on the International Automotive Task Force (IATF) practices, ensuring compliance with industry standards.
Ranking of the Best SOP Software in 2025
Below, we present a ranking of SOP software according to the Lean Community. This ranking, conducted by our team, aims to assist manufacturing companies in choosing software that can facilitate the implementation of standardized work and digitalized work instructions.
Update – SOP Software – August 2025
We observe that more and more people are interested in SOP Software for production and services. In response to the question, we have analyzed which of the listed software solutions currently have or are planning to develop a Kaizen and Competency Matrix modules. The modules are included in the ranking below.
etwi.io System
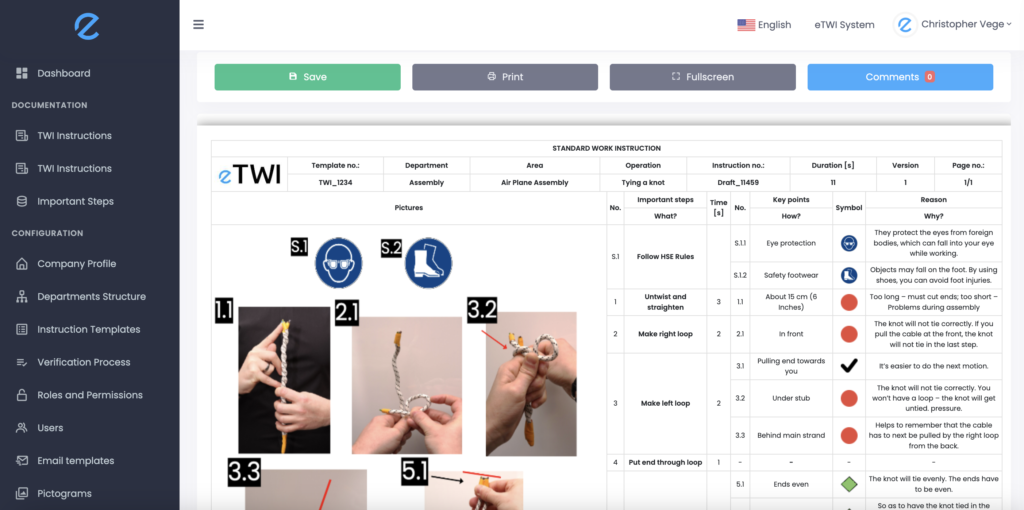
etwi SOP Software
Our rating of SOP Sofware: 4.7/5,0
Overview:
The etwi.io system streamlines the management of Standard Operating Procedures (SOPs) through its digital module in the following ways:
- Create and Update Digital SOPs: It allows for the effortless creation and revision of digital work instructions, ensuring SOPs are always current.
- Display SOPs at Workstations: SOPs can be easily accessed at workstations using QR codes, providing operators with immediate access to the latest instructions.
- Adjustable Instruction Templates: The platform offers customizable templates for SOPs, allowing organizations to tailor them to their specific needs.
- Digitizing Employee Knowledge: etwi.io simplifies converting employee expertise into digital instructions, supporting the quick addition and editing of content and visuals.
- Managing Verification Paths: etwi.io provides tools to establish and manage verification paths for SOPs, ensuring all documents are thoroughly reviewed and validated.
- Communication via Comments: The platform facilitates direct communication between authors and verifiers of SOPs, allowing for real-time feedback and improvements.
etwi.io presents a comprehensive and user-friendly solution for digitizing and managing SOPs efficiently in the workplace.
Pros:
- Fully integrated with TWI best practices for standard creation.
- High-level, user-friendly graphic design.
- Multiple language options.
- TWI consultant support for system users.
- Easy editing of content and images in SOPs.
- Ability to set document approval pathways.
- The possibility of adapting the template to an existing one in the organization eliminates the need to conform the template to the existing standard in the company (even if it is in Excel).
- Possibility to print out SOP in paper form.
Cons:
- No free version of the system is available.
- Currently, only the SOP module is developed; the Training Matrix module is under development and is expected in 2024.
Competency Matrix and Kaizen:
- The Competency Matrix and Kaizen modules are currently under development. The Competency Matrix module allows for managing employee competencies and linking SOPs with individual workers. The Kaizen module enables the generation of documents for Poka Yoke, as well as the submission of improvement ideas. Both solutions are expected to be available by 2025.
Google Workspace and MS Office
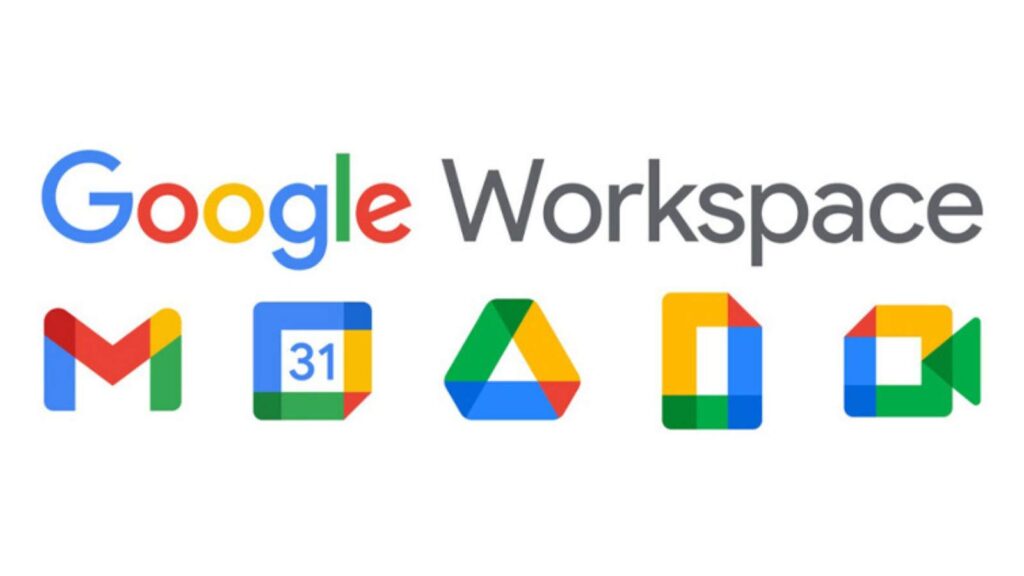
Google Workspace
Our rating of SOP Sofware: 4.5/5,0
Overview:
Google Workspace and MS Office serve as an effective tool for creating and managing Standard Operating Procedures (SOPs) with its user-friendly features:
- Collaborative Editing: Multiple users can simultaneously contribute to and edit SOPs, facilitating teamwork and shared input.
- Cloud-Based Access: Being cloud-based, it provides easy access to SOPs from any location, ensuring global reach for organizations with distributed teams.
- Version History: The platform tracks all changes made to a document, offering a clear history of SOP revisions and updates.
- Interactive Comments: Team members can leave comments and feedback directly on the document, enabling real-time discussions and improvements.
- Customizable Templates: Google Docs offers customizable templates, allowing organizations to create SOPs that align with their specific standards and branding.
- Easy Sharing and Controlled Access: SOPs can be shared with relevant team members, with adjustable access permissions to ensure document security.
Google Docs and MS Office provide a straightforward, accessible, and collaborative platform for efficiently drafting and managing SOPs in a variety of organizational settings.
Pros:
- High brand recognition.
- Capability to use Excel, Word, PowerPoint for instruction creation.
- Version tracking for documents stored on the server.
Cons:
- Not specifically tailored for creating and managing SOPs; more of an adaptation of existing software for a different purpose.
- Difficulty in editing SOPs, such as moving steps in instructions or changing photo numbers.
- The manual adjustment of tools is necessary to meet the requirements related to the creation and management of SOPs.
Competency Matrix and Kaizen:
- There is a possibility to create a Competency Matrix and design a Kaizen submission process, but there is no dedicated functionality for these features.
Poka.io System
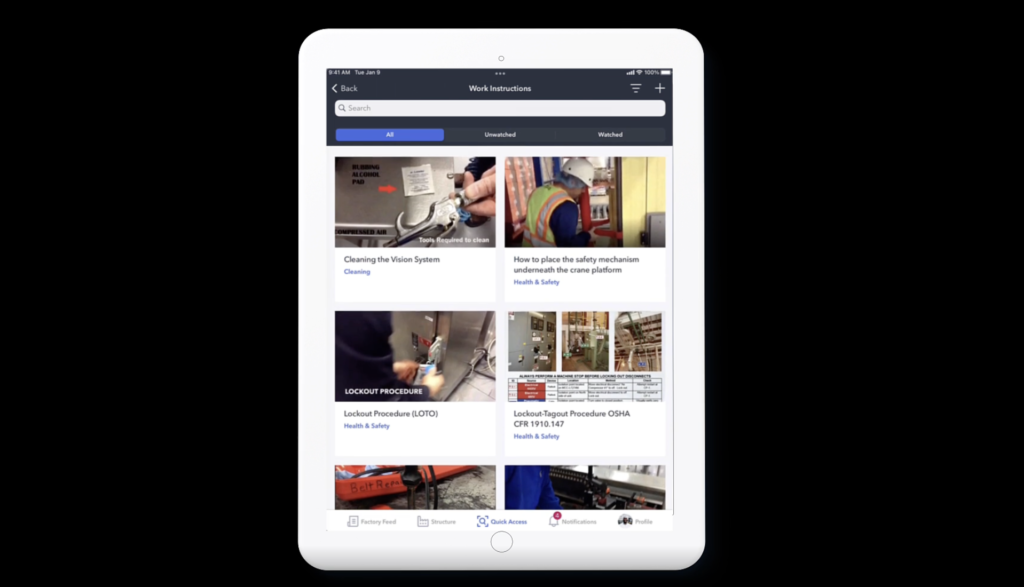
Poka SOP Software
Our rating of SOP Sofware: 4.4/5,0
Overview:
Poka.io is a mobile-first application tailored for frontline workers in manufacturing. It simplifies the access and management of standard operating procedures (SOPs) and task checklists, particularly beneficial for employees who are frequently away from a computer. The app allows team members to communicate and update processes directly from their mobile devices. Key features of Poka include:
- Mobile accessibility for SOPs and task checklists.
- Real-time notifications for updated instructions or new information.
- Document control for compliance demonstration.
- QR codes for quick access to specific instructions.
- Integration of instructional media like short videos and written steps.
Pros:
- Centralized access for frontline workers to job SOPs, troubleshooting documents, and related news.
- Comprehensive dashboard for monitoring employee skills and training progress.
- News feed feature for employees to stay informed about factory floor happenings.
Cons:
- No free version of the system is available.
- Time-consuming setup and maintenance due to the platform’s comprehensiveness.
- Not linked with any best-practice approach like the TWI program
- Limited options for exporting and customizing data from forms and task-tracking activities.
Competency Matrix and Kaizen:
- Poka’s skills matrix and management capabilities give workers and team leads the power to oversee and stay current with role-specific and factory training. The downside is that it focuses mainly on skills rather than competencies. For Kaizen, there is only a virtual board available.
Dozuki System
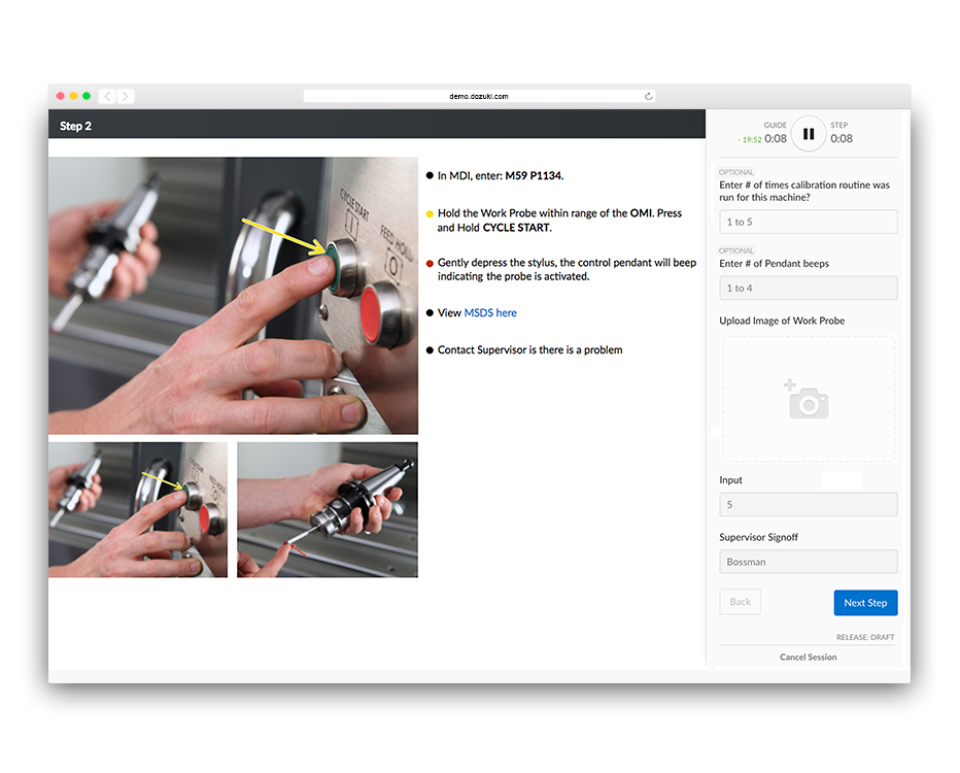
Dozuki System
Our rating of SOP Sofware: 4.3/5,0
Overview:
Dozuki is a comprehensive knowledge, training, and standardization platform specifically designed for industrial companies. It features a mobile-friendly interface that facilitates the easy documentation of processes using images, videos, and more, directly from the field. Dozuki ensures that process changes are synchronized across all devices, maintaining up-to-date and accurate information for the team. Key features of Dozuki include:
- Mobile-friendly for on-the-go documentation.
- Automatic updates of process changes across devices.
- Robust analytics for identifying improvement areas.
- Customizable dashboards for real-time team activity insights.
- Training module tracking to address knowledge gaps.
Pros:
- Simplified organization of documentation into categories like shifts, locations, or job functions.
- Version control that restricts access to outdated content.
- Interactive training guides with operator reporting and response prompts.
Cons:
- No free version of the system is available.
- Limited flexibility in customizing documentation and data collection templates.
- Restrictions on the number of photos and videos per page may limit multimedia integration.
Competency Matrix and Kaizen:
- Now that your operators are organized into Teams and have completed some Courses, how do you keep track of who knows what? Enter the Skills module—a matrix view accessible from multiple locations on the site, displaying a breakdown of job skill proficiencies by operator. However, this module remains quite basic, focusing solely on skills, with no support for competencies. Additionally, the Kaizen functionality is lacking entirely.
OPERATIONS1
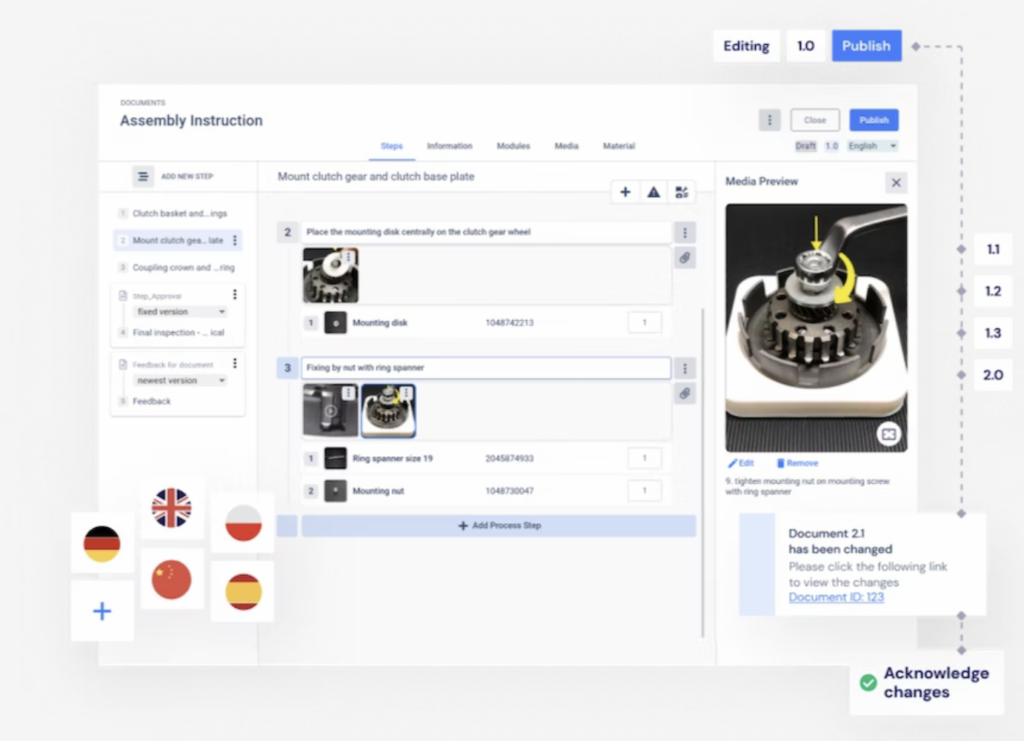
Operations1 – SOP Software
Our rating of SOP Sofware: 4.1/5,0
Overview:
Operations1 is a cloud-based software designed for employee-led production processes in manufacturing companies. It transforms traditional methods by digitizing and simplifying processes, promoting transparency and efficiency. Key features of Operations1 include:
- Centralized Management: Create and manage digital checklists and work instructions in one platform.
- Document Organization: Offers functionalities for managing digital work instructions, and checklists, and implementing global standards.
- Multilingual Support: Create or translate digital work instructions in multiple languages, including media and material descriptions.
- Document Organization Tools: Utilize structural classes and classifiers for organizing documents, media, and materials.
- Modularity: Reduce effort in document creation and updates by using existing documents as modules.
- Release Process: Manage document publishing with an automated approval process for versioning and change history.
- Multilingual Interface: The user interface supports various languages including English, Czech, German, Polish, Lithuanian, Slovak, Chinese, Spanish, and Russian.
- Qualification Module: Enhance process reliability and safety through qualification-based processes.
Pros:
- Centralized platform for creating and managing digital work instructions and checklists.
- Multilingual capabilities for both content and user interface.
- Advanced tools for organizing and classifying documents and materials.
- The modular approach to document creation and updates, enhancing efficiency.
Cons:
- Highly engineering-focused approach to SOP creation, which may not align with the perspective that SOPs should be created by production teams rather than engineering departments.
- SOPs are primarily presented as a process tool rather than as instructional guides for improvement or training.
- The system is mainly oriented towards the digitization of checklists and documents, potentially limiting its scope for broader SOP applications.
Competency Matrix and Kaizen:
- The system lacks a Competency Matrix and Kaizen module. While the Skills module provides a basic matrix view of job skill proficiencies by operator, it does not support the tracking of competencies, and there is no dedicated Kaizen functionality.
VKS App
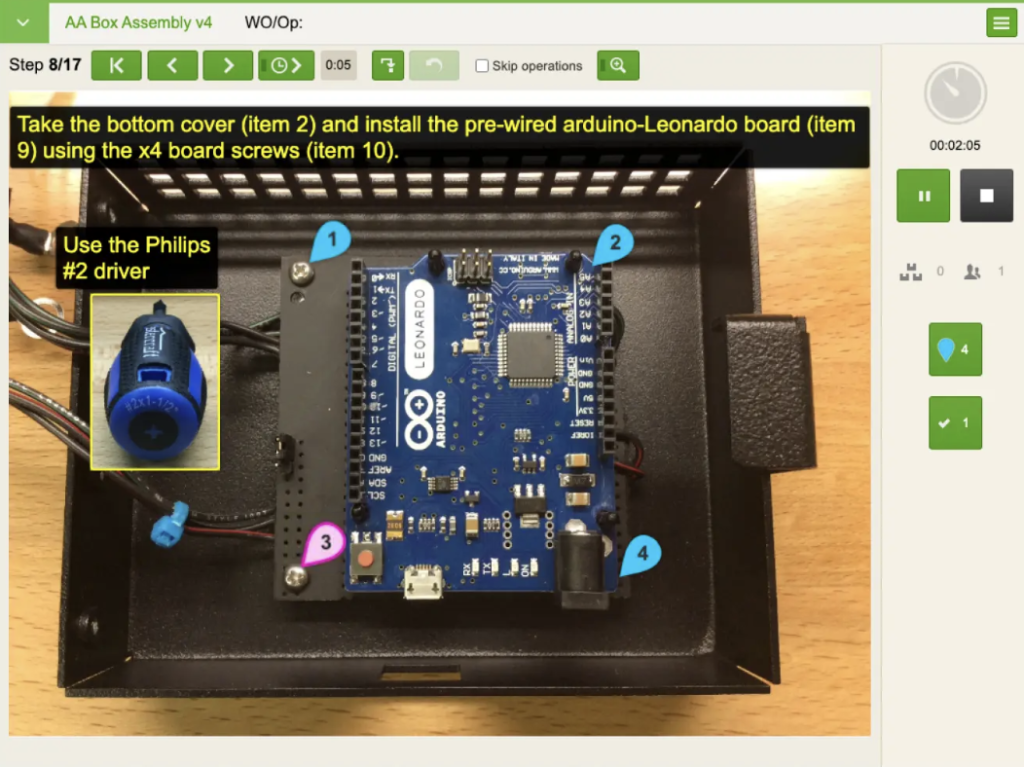
VKS APP
Our rating of SOP Sofware: 3.9/5,0
Overview
VKS is a dynamic work instruction software designed to digitize operations and facilitate the transformation into a Smart Factory. It focuses on enhancing workforce efficiency, accuracy, and compliance through digital work instructions. Key features of VKS include:
- No-Code Work Instruction Software: Enables centralized operational knowledge with step-by-step digital instructions.
- Real-Time Worker Guidance: Provides operators with timely and relevant information, moving beyond traditional paper instructions.
- Visual Workflow: Emphasizes visual learning, processing information much faster than text alone.
- Interactive Visual Tools: Allows integration of pictures, videos, and annotations for clear and effective guidance.
- Pictures: Step-by-step imagery for quick and accurate task comprehension.
- Video: Embedded videos to demonstrate complex operations.
- Annotations: Textual annotations to highlight specific actions and provide context.
Prons
- Empowers real-time, guided instruction for frontline workers.
- Utilizes a visual approach for faster information processing and retention.
- Offers a no-code platform for easy creation and sharing of work instructions.
- Enhances the capture and dissemination of knowledge, especially valuable for training new hires.
Cons:
- SOPs are more focused on demonstrating the process rather than establishing work standards.
- Greater emphasis on procedural steps, with limited scope for explaining underlying reasons that build employee awareness.
- SOPs are presented more in the form of checklists rather than comprehensive work instructions.
Competency Matrix and Kaizen:
- The system lacks a Competency Matrix and Kaizen module. While the Skills module provides a basic matrix view of job skill proficiencies by operator, it does not support the tracking of competencies, and there is no dedicated Kaizen functionality.
Paligo System
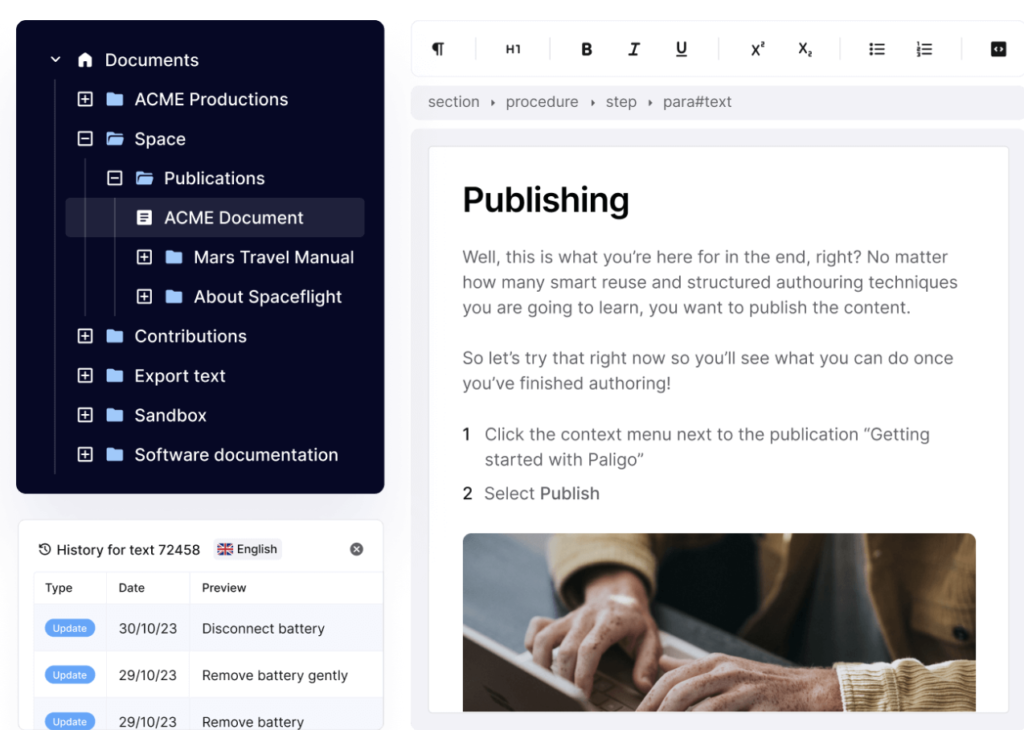
Paligo
Our rating of SOP Sofware: 3.7/5,0
Overview
Paligo is a comprehensive Component Content Management System (CCMS) solution, catering primarily to the needs of technical documentation, policy and procedure management, knowledge management, and more in the context of modern manufacturing and industrial settings. Key features of Paligo include:
- Modern Technical Documentation Platform: Designed to meet the demands of the rapidly evolving manufacturing industry, particularly in the context of Industry 4.0.
- Structured Content for Consistency and Accuracy: Offers structured authoring with a rich semantic content model, supporting complex product documentation and compliance with regulations like ANSI Z535.
- Content Reuse Across Product Lines: Features like modular topic components, conditional profiling, and reusable text snippets facilitate the creation of documentation for multiple product lines from a single source.
- SaaS-based CCMS: Provides an all-in-one platform solution that is accessible and scalable.
Pros:
- Advanced capabilities for creating and managing technical documentation.
- Ensures consistency and accuracy in documentation with structured content and customizable templates.
- Powerful content reuse features, saving time and resources in documentation for similar product lines.
- Aligns with modern industrial standards and supports comprehensive compliance requirements.
Cons:
- Primarily oriented towards technical documentation, potentially limiting its use for broader SOP creation.
- Lacks intuitive tools specifically designed for creating SOPs; more focused on managing and storing work instructions.
Competency Matrix and Kaizen:
- The system does not include a dedicated Competency Matrix or Kaizen module. Although the Skills module offers a basic matrix view of operator job skill levels, it lacks the ability to track broader competencies. Additionally, there is no specific functionality to support Kaizen initiatives.
Swipe Guide Software
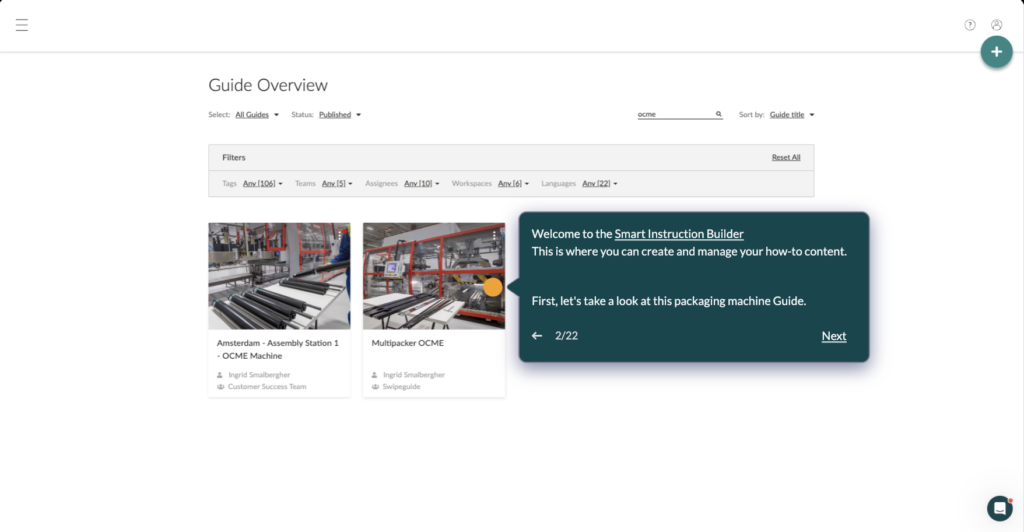
Swipe Guide SOP Software
Our rating of SOP Sofware: 3.6/5,0
Overview
SwipeGuide presents itself as a digital library for smooth operations, aimed at standardizing operating procedures and ensuring consistent performance across teams. Key features of Swipe Guide include:
- Standardization of Operating Procedures: Facilitates the standardization of procedures without complexity.
- QR Code Access to Work Instructions.
- Continuous Process Improvement: Encourages team input for ongoing process enhancements.
- Crowdsourced Knowledge Capture: Allows the collection of expertise from frontline workers through digital work instructions and SOPs, supported by checklists and approval workflows for compliance and quality.
- Knowledge Sharing Across Sites: Promotes the sharing of best practices across different locations and sites.
- Content Reusability and Localization: Offers the ability to reuse and localize instructions, SOPs, and checklists according to team-specific requirements.
- AI-Assisted Content Creation: Utilizes AI to aid in the creation of content, making the process more efficient and effective.
Pros:
- Easy access to work instructions via QR codes.
- Includes checklists and approval workflows.
- AI-assisted content creation.
- Enables content reusability and localization.
Cons:
- Oriented towards task checklists, possibly more suited for maintenance departments.
- Lacks specific focus on the reasons behind procedures.
- Standards are presented as a sequence of process steps, not ideal for instructional training.
Competency Matrix and Kaizen:
- The system provides a dynamic overview of the skill development status for team members, allowing you to compare past and current levels for each skill set. However, the focus is heavily on individual skills, without offering a clear visualization of broader competencies.
MaintanX
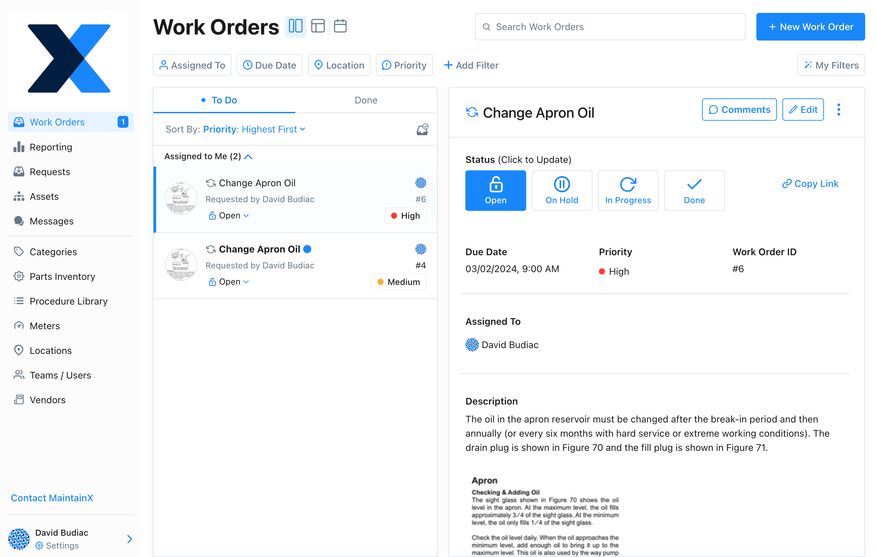
MaintanX
Our rating of SOP Sofware: 3.5/5,0
Overview
MaintainX is a mobile-first platform specifically designed for non-desk employees, including those in industrial and frontline work environments. It offers a comprehensive solution for on-the-go access to various operational needs. Key features of MaintanX include:
- Mobile Accessibility: Facilitates easy access to work orders, procedures, and checklists for employees on the move.
- Cloud-Based Platform: Ensures scattered employees can stay connected and updated on tasks and project statuses.
- Beyond SOP Management: Includes features for inventory management, inspections, and work order management, centralizing essential information in one place.
- Unified Application: Eliminates the need for multiple third-party tools or systems, streamlining operations.
Pros:
- Robust Reporting
- Automated Triggers
- Collaboration Tools
Cons:
- Mainly focused on Maintenance activities.
- Learning Curve: Setting up and familiarizing with the product can be time-consuming.
- Limited Customization: While it provides essential functionalities, there may be restrictions in tailoring tasks and boards to specific organizational needs.
Competency Matrix and Kaizen:
- The system is missing dedicated modules for both the Competency Matrix and Kaizen. While it offers a dynamic overview of individual skill development, it does not provide tools to visualize or manage competencies, nor does it support Kaizen-related functions.
Best SOP Software – Comparison
The ratings for various SOP software systems, based on their practical application aligned with the best practices of Lean Management and the Training Within Industry (TWI) program, are as follows:
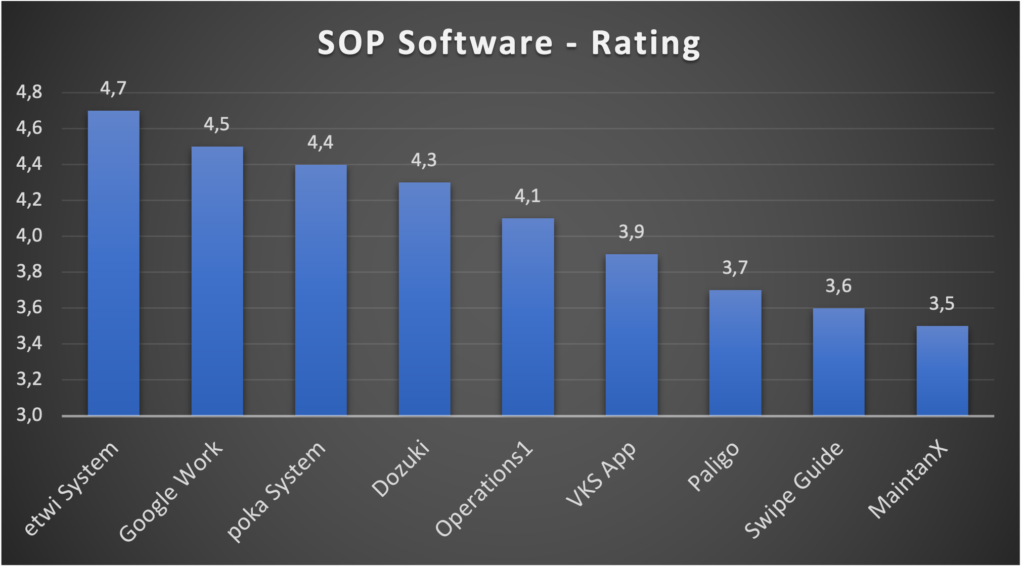
SOP Software – Ranking
In this evaluation, the primary focus was on the practical use of the systems in conjunction with Lean Management principles and TWI methodologies. While some systems are technically advanced, they sometimes miss the core essence of Lean, which prioritizes simplicity and efficiency. The top-rated systems, like etwi.io, stood out due to their user-friendly nature, suitability for everyday activities, aesthetic design, and lack of superfluous features. These attributes make a system more viable and beneficial for actual use by employees in various work environments. The ratings reflect not just the technical capabilities of the software but also their alignment with Lean principles, ensuring that they add real value to the daily operations of organizations.
SOP Software – Conlusions
In this chapter, we will provide a comprehensive summary of SOPs, answering the most crucial questions, as well as sharing our final thoughts. This article is relevant to the developments and best practices of the year 2024.
Frequently Asked Question
In our FAQs, we explore a vast array of topics, ranging from grasping the essential features of SOP software to tackling the challenges of user adoption. Our objective is to furnish you with the necessary knowledge and confidence for making informed decisions and effectively integrating SOP software into your daily operations.
How to use SOP Software in Health, Safety, and Environment (HSE)
In the context of Health, Safety, and Environment (HSE), SOPs play a crucial role. They ensure that operations are performed safely, minimizing the risk of accidents and ensuring compliance with environmental regulations. This is particularly important in manufacturing, where workers often interact with hazardous materials and complex machinery. SOPs in this area might include procedures for handling chemicals, operating machinery, or responding to emergencies, all aimed at safeguarding the health and safety of employees and the environment.
How to use SOP Software in Quality Assurance
Quality assurance is another critical area where SOPs are extensively utilized. In manufacturing, the quality of the product is paramount, and SOPs help in maintaining consistent quality and compliance with industry standards and regulations. SOPs related to quality might include detailed instructions on production processes, quality checks, and handling of non-conformance issues. This ensures that every product meets the required standards and specifications.
How to use SOP Software for Employee Instruction
SOPs play a crucial role in training and instructing employees, acting as reference points for the correct execution of tasks and aligning all staff with the company’s standards and practices. They guide new employees through the work processes and set clear expectations. For existing employees, SOPs provide a reliable reference to ensure correct and consistent task completion, particularly in complex or infrequent processes. In TWI Job Instructions training, instructors should employ a 4-step method, using SOPs as a foundational tool for effective training.
Where Digital SOPs can be used
Digital Standard Operating Procedures (SOPs) revolutionize the management of manufacturing processes, providing greater flexibility, accessibility, and efficiency compared to traditional paper-based SOPs. You can effectively utilize digital SOPs in various areas such as Production Line Operations, Quality Control and Assurance, Maintenance and Troubleshooting, Health, Safety, and Environment (HSE) Compliance, Training and Onboarding, Process Optimization and Kaizen, Documentation and Record Keeping, Supply Chain Management, Customer Support and Service, as well as Remote Management and Collaboration.
How does SOP software work?
SOP software functions as a comprehensive platform that consolidates various aspects of process documentation. It enables teams to create, manage, and update documents seamlessly. Initially, teams utilize the built-in editor provided by the SOP software to craft their documentation, incorporating appropriate formatting and visual aids for clarity.
How easy is SOP software to use?
Most SOP software provides a user-friendly experience, offering an intuitive interface, customizable templates, and step-by-step guides. It integrates smoothly with existing systems and collaboration tools, improving usability. Additionally, mobile accessibility allows users to manage SOPs while on the move. Adequate support and training resources are typically provided, making these platforms accessible to users with varying levels of technical expertise.
How should SOP Software be connected to the Competency Matrix and Kaizen modules?
SOP Software should be closely integrated with both the Competency Matrix and Kaizen modules to maximize its effectiveness. These modules are essentially tools for utilizing the SOPs in practice.
- Competency Matrix Integration:
SOPs should link to the Competency Matrix to align employee training and skill development with defined work standards. For instance, methods like TWI Job Instructions can train employees, and their competencies can be tracked and updated in the matrix as they master the procedures. This allows managers to ensure that employees are fully competent in the necessary skills to maintain operational efficiency. - Kaizen Integration:
The Kaizen module should leverage the SOPs to drive continuous improvement. SOPs outline the current state of work processes, providing a clear baseline for identifying areas of improvement. By integrating Kaizen with SOP Software, employees can use the standard procedures as a reference point to suggest enhancements, solve problems, and seek efficiencies, ensuring that improvements are based on the existing standards. This way, Kaizen becomes a structured approach to improving work processes, fully aligned with the current SOP framework.
What has changed in SOP Software between 2024 and 2025?
Between 2024 and 2025, one of the most notable shifts in SOP software for manufacturing has been the deeper integration with eTWi (electronic Training Within Industry) systems. More vendors now recognize that SOPs should not just document tasks, but also serve as active training tools linked to structured methods such as TWI Job Instructions.
Systems like etwi have led the way by enabling:
-
Direct connection between SOP content and TWI-based training modules.
-
Real-time tracking of employee competency development through an integrated Competency Matrix.
-
Streamlined update cycles where changes in SOPs automatically inform training materials and requalification needs.
This evolution means SOP software is no longer only about documenting “what” to do—it’s about embedding the “how” and “why” into the work process, ensuring that standards are learned, applied, and continuously improved.
How is Artificial Intelligence (AI) changing SOP creation and management?
In 2025, SOP software increasingly uses AI-assisted authoring to accelerate the creation, updating, and translation of work instructions. AI tools can:
-
Suggest SOP structures based on industry best practices (e.g., Lean, TWI).
-
Automatically generate step descriptions from process videos or operator actions.
-
Provide multilingual translations in seconds, ensuring consistent communication across global teams.
-
Highlight gaps or inconsistencies in existing SOPs by comparing them to previous revisions or similar procedures.
This allows manufacturing companies to reduce administrative workload, ensure accuracy, and update standards faster in response to changes on the shop floor.
Can SOP Software predict training needs and process risks?
The newest generation of SOP software integrates predictive analytics with SOP usage data. By tracking:
-
How often an SOP is accessed.
-
Which steps generate the most operator errors.
-
Which competencies in the matrix show gaps or declining scores.
The system can automatically flag areas needing refresher training or process review. Combined with Kaizen and eTWi, this predictive capability turns SOPs into proactive tools for preventing quality issues, safety incidents, and productivity losses before they occur.
Final Thoughts about SOP Software
Standard Operating Procedure (SOP) software has significantly transformed how organizations handle process documentation and management. It offers a centralized platform for teams to collaborate, monitor progress, and ensure that tasks are completed with precision and accuracy. The adoption of SOP software leads to greater consistency in processes, enhanced efficiency, and improved collaboration across different sectors.
When choosing an SOP software solution, it’s important to consider how well it integrates with existing workflows and meets the specific needs of the organization. The right choice of software can lead to increased productivity and employee satisfaction by streamlining routine operations and making information readily accessible.
Embracing SOP software recommended by the Lean Community is a step towards a future of consistent, efficient, and error-free operations, marking a significant advancement in the way organizations approach their process management and documentation needs.
I am highly experienced marketing professional with over 4 years of experience in the industry. With a strong background in marketing strategies for both B2C and B2B companies. I am skilled in well-versed in the latest digital marketing trends and technologies.
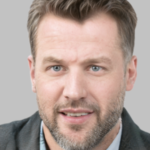
An experienced lean manager with a deep understanding of lean management principles and techniques. I have strong leadership skills, and I am able to motivate and lead teams to achieve results. I am able to communicate effectively, and are skilled at building consensus and working with cross-functional teams. In addition to my experience and expertise, I am also committed to continuous learning and improvement. I am always looking for ways to learn and grow, and I am willing to try new approaches and techniques in order to achieve success.