A “learning” organization as a means of maximizing the potential hidden in its resources
Problem solving – article available to download in PDF at the bottom.
In every organization, we deal with problems at every level of its structure. The way in which a given organization deals with them may contribute to the ease of achieving its business goals, or, unfortunately, to failure. There can be many approaches to problems. From hiding problems and sweeping them under the carpet, through reacting to difficulties (the so-called firefighting) and searching for the root causes of the problem, to finally implementing a methodical approach to problem solving into the culture of the organization while at the same time involving every employee of the given company.
In the dissertation below, I would like to answer the question:
“Why should every company, or every venture, aim to become a learning organization?”
Well, if I want to answer the question of why we should strive to make our organization a learning one, why do I start by deliberating about problems? A snowball can be a good comparison here. At the beginning, I mentioned how companies face problems. Now imagine an organization that “sweeps problems under the carpet”. The result of this approach can be catastrophic, problems pile up, and the snowball grows larger and is more difficult to control and stop. As a consequence, it may even lead to the bankruptcy of the organization. Now imagine that we are able to change the direction of this snowball, and instead use its growth to achieve goals and, what is more important, have a positive impact on operational results in a continuous manner. In order to achieve this, it is necessary to build the culture of a learning organization, where every small cog is involved in solving problems, and each problem is an opportunity for the organization to develop. It is associated positively, because it allows for the transformation of the organization.
Definition of the problem
Before we move on to specific tips on how to change the trajectory of a snowball, we need to define what the problem is. According to the definition of lean management, a problem is a discrepancy between the standard and the actual situation, in other words the difference between how something works and how it actually should work.
Therefore, as in many cases in the philosophy of Lean Management, the first and key thing is to implement standardization of work. It is not without reason that Taichi Ohno once said that there are no improvements without a standard. The standardization of processes is a necessary condition for the implementation of a problem-solving system and the striving to build a learning organization. The topic of implementing standardization of work is very extensive, and if you do not have standardized processes in your organization, I encourage you to read the numerous materials regarding this issue.
Now let’s consider what we get by standardizing work in the context of problem solving. Of course, there are many benefits. The most important, resulting from the very definition of problems, is the ability to perceive them. In the context of what was written in the introduction to this article, namely that problems for the organization should be perceived as an opportunity to develop and an opportunity to learn and develop employee competences, this benefit is certainly very large, but is not the only one.
There are several types of problems in any organization.
- Obvious problems – where the standardization of processes does not occur, with an example of such a problem being e.g. a broken machine that prevents work. I don’t need standardization to know that if I can’t continue working, it’s a problem (of course such a problem can be hidden by the material backfilling the machine during the previous process). The open question is whether (if all processes are doing work) this means that these problems are not occurring. Of course not! And here we come to the next type of problem.
- Problems arising from a deviation from the standard – which directly arise from the definition of the problem. They occur when the work deviates from what has been defined in the standard. It should be added that the standardization of work itself solves many problems. As we know, the definition of the standardization of work is the fact that it is the currently agreed best method of performing work. Consequently, when agreeing on the best method, many problems have to be eliminated. Standardization itself gives us the opportunity to understand how the process should work, and helps us to find differences when it does not work properly.
- Problems to improve existing standards – if our process is working properly and the results we set for ourselves are achieved, we can move on to generating problems that will aim to improve our processes. The easiest way to define problems for improvement is to set higher goals than those that are achieved by the process. Thanks to this, we are able to constantly improve.
- Problems that require a change of approach – in the goal-raising phase, we will come to a stage where we will need to change our way of thinking. Thanks to a systematic approach to solving problems, we can facilitate the process of implementing innovations and breaking paradigms.
As we can see in the above definitions, a comprehensive approach to problem solving leads us to the full range of needs that the organization is facing. From establishing processes, through keeping them within a specific framework, to improving them and implementing innovative thinking, we can build a competitive advantage for our company. Therefore, building a culture of a learning organization through problem solving and involving every employee of the company in it can be crucial in terms of improvement, and is synonymous with spreading a culture of continuous improvement.
What approaches to problems and their solutions do we know
The easiest way to deal with process difficulties is … to pretend the problems don’t exist. This may seem impossible, but there are still companies that claim that there are no problems within their organization. Unfortunately, this brings a missed opportunity for learning and development.
Once we learn not to hide problems, we must face them. At the beginning of the journey in looking for the elimination of problems, it is natural to jump to solutions that will supposedly eliminate them. Unfortunately, this is an illusory approach to solving them. According to statistics, over 90% of solutions that are imposed in the first place do not eliminate the root cause of the problem, and thus it will appear again in the future. We should avoid this approach and try to find the root cause that generates it. Therefore, after the first unsuccessful attempts, many organizations try to implement a standardized approach to problem solving that helps to systematically carry out root cause analysis.
Unfortunately, when introducing such an approach, it often happens that human nature wins and we jump to solutions (in the case of analysis). Therefore, it is important to identify and develop problem solving session leaders. Thanks to this, we can come to a situation where given issues will actually be removed by eliminating the root cause.
The ability to find the right solutions is just the beginning of the road on which many organizations end their adventure with the issue. This is natural, but does not use the full power of the approach. Let us remind you that the goal is to involve every employee of the organization to change the course of the snowball in order to lead to continuous development and improvement, as well as to learn and develop by solving and eliminating new issues – also those that will be defined by ever higher goals.
How to spread a problem-solving culture and strive for a learning organization.
Don’t hide your problems
The first thing, and probably one of the most difficult, is to make sure that, at any level of the organization, the problems we are struggling with are not hidden. Hiding is a natural defense process, against the fear of superiors or the fear of having some responsibilities being added. In our learning organization, we should cultivate a culture where problems are welcomed and are an opportunity for development. This message should be heard by employees at all levels. It is also important not to leave an employee alone with the problem at the beginning of the road. This will lead to a situation where, after a few deaf “calls for help”, the employee will cease to highlight the inconsistencies at his workstation.
Structure the approach
As mentioned earlier, it can be helpful to structure the approach and standardize the analysis to more easily progress through such analysis in order to capture root causes. In addition, such an analysis is carried out on special sheets, which are also used for reporting and sharing solutions between areas. There are many worksheets that you can readily find in troubleshooting studies. The most popular is the A3 sheet, which is described in more detail in the book “Understanding A3 Thinking” by Durward K Sobek and Art Smalley. This is a great approach that I personally recommend. It is also worth adjusting the data of reports to your own needs, and creating a simplified sheet for small things, as it is not worth creating bureaucracy for solutions that take only a moment.
Promote leaders
Find in your organization willing people who will spread the culture of the learning organization. It is important that these people have leadership skills. One of the tasks of the leaders will be to train other employees, and then to provide feedback to them.
Train staff. If you already know who will be the leader, tell the rest of the staff about the approach. The first step will be training, but do not ask them to solve problems immediately after it. First, invite trained people to the team, thanks to which they will see how leaders solve real inconveniences. Only after gaining experience can you allow them to solve your problems. Don’t forget to provide feedback – positive things and things that need improving. Use the leaders that you promoted earlier. It is a long and continuous process of developing employees – they will not be able to properly control problems immediately. Once they achieve the desired effect, set the bar higher and ask them to solve more complicated things. A challenge is the foundation of development, and also a factor that keeps you motivated.
Make problems visible.
If we can no longer hide problems, the next step is to make them visible. Visualize the desired state in accordance with the standard that you implemented. Make such a visualization that any deviation can be seen at a glance. Each deviation is caused by something, and it is a potential problem that can be used for the development of the organization.
Another thing that can be implemented in order to find more and more difficulties is the ANDON system. In a nutshell, ANDON allows a process to be stopped immediately in the event of a mismatch. This not only allows you to immediately deal with the problem, but also to gather information about all non-conformities that occur in a given process. Stopping a process in the ANDON system can be automated, but it should also be possible for an employee to stop a process if they notice a non-compliance. The role of production leaders in the entire system is very important, and they should encourage employees to use the system. This may not be so obvious. At the initial stage of implementing the ANDON system, we may notice a temporary drop in productivity indicators, but bearing in mind the goal of the entire organization, i.e. developing people by solving problems and changing the direction of the snowball, we should abandon short-term indicators in favor of long-term ones.
Suggestion system
A tool that can encourage employees to eliminate problems in their workplace through improvements are employee suggestion systems. This tool seems to be a simple solution, but it is worth being prepared before implementing it. One of the most important challenges will be the implementation of the submitted ideas, as well as their fair evaluation, so before implementing the suggestion system, make sure that you have adequate resources to maintain it.
Celebrate success
In a comprehensive approach to problem solving, it is preferable to reward the best examples and the most committed employees, rather than look for blame and to punish the employees for their imperfections. Therefore, create a reward system or a system of celebrating success. Adapt the system to the culture in your organization. The prizes do not have to be in cash or in kind, because sometimes the best driving force are simple solutions and awards.
Visualization – show the benefits
Create visualizations through problem-solving boards. Present the set goals of the system and the currently achieved results so that you can see at a glance whether the results are satisfactory. It is also important to visualize the best examples of solutions that have so far been implemented. It’s also a good idea to share the best practices that can be used in other processes.
Set goals
An important factor that can generate problems, with which we can deal with, is setting goals for a given process. Of course, when they are not achieved, we should undertake an analysis and designate actions that will help us eliminate inconsistencies and achieve the specified levels of indicators. It is also a good idea to increase the requirements if the previous ones have been fulfilled for a long time. This will lead to the improvement of our process.
Avoid IT systems, at least at the start.
Systems and IT solutions are undoubtedly useful and can facilitate work or the collection of data about the process. However, when our problem-solving process is just at the beginning, it is worth considering moving away from computer improvements. This will improve the learning process of employees, which we care about a lot, because thanks to better learning, we will achieve the goal of engaging each employee faster. As the processes gain awareness and maturity, they can be supported with IT solutions.
Summary
Let us recall the question asked at the beginning of the text:
“Why should every company, or every venture, aim to become a learning organization?” I hope that after reading this article, you have learned how important it is to involve every employee in solving problems, and how powerful a tool for improving your processes this is. By striving for a learning organization, we maximize the speed of improvement. Problems themselves are an opportunity for us, and not a cause of failure. Therefore, the well-known saying “a lack of problems is a problem” is important.
Problems are always there, so let’s take advantage of them. If we don’t see them, it can lead to stagnation in our organization’s performance.
If you have any questions or concerns, I will be happy to answer them. Contact me via Lean Community discord – Marek | Lean practitioner.
You can buy this article in PDF form on the Lean Global Marketplace
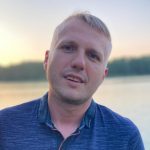
Over 15 years of experience in Lean Management. An expert in continuous improvement and production management in the automotive, aviation and consulting industries. An enthusiast of building a real lean organization by engaging people in problem solving instead of picking the tools from the lean toolbox. He is a certified by Toyota Way Academy as the Lean Transformation Leader and the Lean Expert.