PDCA DMAIC A3 8D. As we all know, it is unavoidable that within any kind of industry, there will always be problems, but we cannot negatively face this reality, the approach should be the opposite, as expressed by Taiichi Ohno in the quote: “Having no problem is the biggest problem of all”.
Can be defined as problems everything that hampers the business from achieving its strategic targets. The most common problems are Customer complaints, quality, productivity, downtime, safety incidents, and financial losses. All these kinds of problems must be solved as fast as possible, or the business results and strategy will be strongly affected.
As if the problems are not solved business will be fated to fail, when problems are correctly addressed, the opposite happens. That’s why one of the main goals of Lean management is to make the problems visible so that it can quickly be solved. For a better performance against the problems, there are in the market some great tools to be used, the most famous are: PDCA, DMAIC, A3, and 8D.
Regardless of the tools available to be used, there is a mental model to be followed when addressing problem-solving:
1- Protect the customer
2- Problem understanding
3- Cause identification
4- Corrective action definition
5- Implement corrective actions
6- Validate corrective actions
In the company I work, we use an 8D process combined with a daily fast-response meeting aiming a better control of the problem-solving process.
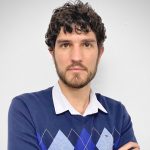
Mechanical Engineer with the emphasis on manufacturing industry, highly organized, with good communication and project management skills. Always focused on reducing costs, and delivering results by using the resources I've learned in my studies, along with the experience gained from the companies I worked. Key strengths: Project Management, TWI - Training Within Industry, Lean Manufacturing, Process Standardization, Leadership of multi-functional teams, Strategic Planning, Continuous Improvement, Extrusion Tooling Design, Extrusion Process, CAE Analysis.