Machine downtime – how to reduce? Some time ago, I had a very interesting conversation about whether it is possible to reduce the time of downtime. Of course, it would be best if there were no failures at all, but that is impossible to achieve (although one can be very close). What needs to be noted is that downtime is a composite of various activities that ultimately affect the duration of the downtime. Since failures will occur, is it worth taking certain actions to reduce the downtime itself? There is even one magical KPI that tells us about the average machine downtime. It’s MTTR (Mean Time to Repair). You can read about managing through KPIs here: https://corazlepszaprodukcja.pl/2021/08/07/7-krokow-do-zarzadzania-przez-kpi/
Let’s look at 10 activities where there is potential to reduce downtime and improve the efficiency of our production processes.
Table of Contents
Toggle1. Quality of information.
The quality of information we provide to the maintenance duty officer is incredibly important. Each of us makes decisions based on the information we have. The more detailed information, the easier it is to make the right decision. Detailed information about what the symptoms of a fault are, under what circumstances the failure occurred, or information about the machine’s condition, alarms, errors will allow for quick reallocation of appropriate resources and equipment. This is definitely one of the greatest potentials in the topic of optimizing downtime.
2. Machine Downtime – Time to reach the failure.
The time it takes for a maintenance technician to reach the place where the problem occurred is also downtime. And while in the case of a small production hall this time can be counted in single minutes, with a larger machinery park this time can unnecessarily extend. A clever solution is to equip maintenance technicians with three-wheeled bicycles (or other means of transport). This shortens the time to reach the machine as well as the journey to the warehouse for spare parts or other necessary tools. The rear basket is an excellent place for the most commonly used tools or even a laptop for diagnostics.
3. Determining the working time of “setters”.
In many companies, there are specially delegated people often called “setters” as maintenance support for minor failures, defects, or the necessity of adjustments. This is a good approach supporting the maintenance department provided that we define the time after which our setter escalates the problem to the technical department. Of course, this value is arbitrary and can vary depending on the department, process, or company. For example, let it be 30 minutes. After this time, if the actions of the setter or other people on behalf of the production department do not bring effects, the problem should be escalated to the technical department. After solving the problem, feedback on how to deal with this type of situation in the future can return to the “setter” in the form of a single-topic lesson or OPL.
4. On the front line.
In point No. 3, I mentioned faster transport. But in my career, I have also visited factories where the maintenance department was located in a separate building! It was a nightmare! An incredible loss and waiting for technical support to arrive. Relocating technicians closer to the front line, i.e., closer to the production lines, nests will definitely save precious time. I’m not talking about moving the entire workshop but about relocating maintenance technicians closer to the production lines equipped with the most commonly used tools.
5. Creating OPL – One Point Lesson as part of TPM-AM.
If we have decided to embark on the TPM path and activate TPM AM activities, one of the options is the transfer of knowledge from the maintenance department to PROD on how to deal with simple failures. We’re not talking about replacing parts or more serious repairs here. Developing awareness of how to adjust a sensor, refill oil in the machine, or replace some filters will allow for an immediate response in case of a fault and increase OEE.
6. Equipping maintenance technicians.
Sounds funny? But it’s not at all. Honestly, when I see how maintenance technicians “make” the necessary wrenches, pullers, or other equipment, it drives me crazy. I’m not even talking about manual wrenches from the PRL era pulled out of the “Fix it yourself Wigry 3” set. Good equipment, quick ratchets, or wrenches that can be used at different angles will allow us to steal precious minutes from downtime.
7. Availability of spare parts.
I’m reminded of a certain TPM project. Meeting with the Head of Maintenance and the factory owner. Discussion of yesterday’s failures and a belt failure on the machine. But it’s already working. The mechanic quickly got in the car, drove to the store where they sell such belts (the city next door), and we had the belt at the company in 2 hours. Lucky in misfortune, that the belt was available within 2 hours. And if we had to wait for it for days or weeks? I understand that we are not able to keep all parts in stock but maybe at least for machines critical to our process (ABC machine criticality analysis).
8. Work Standardization for Maintenance, i.e., instructions for Maintenance
Although it seems to be a daunting task, work instructions in Maintenance are a great solution that improves the quality of work and shortens the duration of failures. How does it happen? No one, not even the most experienced mechanic, remembers all methods of assembly, disassembly, or diagnostics of machine subassemblies. Introducing instructions that tell us how to step by step replace certain elements (especially the complicated ones) will save time spent on reviewing the DTR documentation or deducing how it is assembled. Such an approach will save us from guessing what the next step should be in solving a failure.
9. Check List for multi-causal failures
I think everyone who works with machines has encountered a situation where a given fault may be influenced by many causes. What extends the diagnosis time is searching for potential causes and “guessing” which other elements may affect the occurrence of a particular failure. Creating a check list based on previous failures, what to check, thereby excluding subsequent points will allow the person removing the fault to diagnose faster and reach the root cause.
10. 5S.
The last point on our list is 5S both on the machine and around the machine. Dirty machines or production waste mean that technical services, upon arriving at the site of the failure, must first prepare their workspace. The same situation occurs when production material accumulates around the machine or there are “temporary” buffer fields. The lack of clear 5S rules at the workplace can also extend the time to remove a failure and reduce the OEE of our machine.
Machine downtime – how to reduce? Above, I have shared with you 10 ways to shorten machine downtime and thus raise certain KPIs like OEE, Productivity. What I can definitely recommend is observing the process of removing failures, talking to operators, maintenance, and drawing your own conclusions based on observations from Genba. And of course, to share your experience in the comments, how do you deal with shortening downtime…
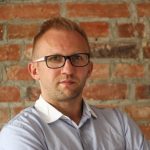
I was lucky that everything I learned about Lean, Kaizen, or production optimization started in a Japanese company. There, under the supervision of Japanese staff and during training in Japan, I learned how to approach the Continuous Improvement process. Over time, I also learned about other practices in other companies.