Implementing the PDCA. Are you wondering how to strengthen your organization in the areas of production and production-supporting services? How to increase engagement in solving the daily problems we face? How to reduce the number of recurring issues and use emerging weaknesses to reinforce the organization?
Table of Contents
ToggleExploring Improvement Strategies for PDCA
There are probably many ways, and each company should find the most suitable one for its situation. I would like to suggest a tool that could be one of the elements on your path of development: the A3 Report. It works great in production areas and beyond. It provides a better understanding of the PDCA methodology. It enables development and raises awareness of defining goals well – SMART goals. It teaches how to define root causes of problems.
Guiding Thoughtful Solutions
It helps avoid rushing into solutions too quickly. It focuses the team on evaluating achieved results and conclusions from the conducted improvement – a new standard.
Summary – PDCA
Utilizing the PDCA methodology through A3 reports offers a comprehensive approach to strengthening your organization. By analyzing and addressing challenges methodically, fostering deeper understanding, and promoting thoughtful problem-solving, your team can work towards achieving improved outcomes and sustainable progress.
Delving into the PDCA cycle—Plan, Do, Check, Act—empowers you to continually assess and enhance your processes. The A3 report, serving as a versatile tool, aids in devising strategic plans, executing them, and systematically evaluating results. Emphasizing a culture of continuous improvement, this methodology facilitates proactive decision-making and cultivates a resilient, agile organization ready to navigate evolving landscapes.
Implementing the PDCA
To enhance both production and production-supporting services, it’s imperative to actively engage in solving everyday challenges and reduce the recurrence of issues. Implementing the PDCA (Plan, Do, Check, Act) cycle can be a significant step in this direction. This approach helps in identifying emerging weaknesses and using them as opportunities to reinforce the organization.
The Role of A3 Reports
A3 Reports serve as an excellent tool in this context. They are not just effective in production areas but are versatile enough for broader applications. A3 Reports promote a deeper understanding of the PDCA methodology. They emphasize the importance of setting SMART (Specific, Measurable, Achievable, Relevant, Time-bound) goals. This tool is instrumental in accurately identifying the root causes of problems and encourages a methodical approach to problem-solving.
Exploring Improvement Strategies in PDCA
Using A3 Reports within the PDCA framework prevents the rush towards immediate solutions. It encourages a team to focus on the evaluation of results and the lessons learned from each improvement initiative. This approach leads to the establishment of new standards and practices.
Cultivating Continuous Improvement
The core of the PDCA cycle — Plan, Do, Check, Act — is continuous improvement. It involves planning strategies, executing them, checking the outcomes, and acting on the insights gained. The A3 report is pivotal in this process, serving as a guide for strategic planning and systematic evaluation of outcomes.
Building a Resilient Organization
Adopting the PDCA methodology with A3 Reports promotes a culture of continuous improvement and proactive decision-making. It helps create a resilient and agile organization capable of adapting to changes and staying competitive. As you embark on implementing these strategies, it’s essential to recognize the transformative potential they hold in problem-solving and organizational growth. This journey towards improvement is marked by shared insights, collaborative efforts, and a relentless pursuit of refining processes and methodologies.
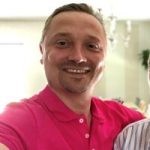
Boguslaw is certified Lean Six Sigma Black Belt. Responsible for implementing Lean Culture in the organizations, starting from 5S program, changes in the Operating System, and growth in Problem Solving Tools. He is a Lean Practitioner with over 20 years of experience in different industries.