Ishikawa impact extended far beyond Japan. His methods and philosophies were adopted by industries worldwide, contributing to the rise of the quality movement in the West during the late 20th century. His work played a pivotal role in shaping the modern approaches to quality and manufacturing efficiency.
Ishikawa authored several books on quality control and management, further disseminating his ideas globally. His belief in the power of collective responsibility for quality, combined with practical tools like the Ishikawa Diagram, has left a lasting legacy in both theory and practice.
Table of Contents
ToggleHow to make Ishikawa Diagram?
Ishikawa diagram as a simple problem-solving tools can be done in 6 steps:
- DRAW THE FISHBONE – Draw the template on your whiteboard/flipchart. The idea is that “head“ shows the problem (effect) and “bones” indicate the impact of the causes.
- DEFINE THE PROBLEM – Agree on a problem statement (effect). Write it at the center right of the whiteboard or flipchart. This ensures that everyone have the same understanding of problem you’re addressing.
- CHOOSE THE MAJOR CATEGORIES – Brainstorm the major (specific) categories of causes of the problem. If this is difficult use generic (4M/6M) categories: MEN, METHOD, MACHINE, MATERIAL, MEASURE, MOTHER NATURE. Write the categories of causes as branches from the main arrow. See here: 4M Checklist
- IDENTIFY CAUSES WITHIN EACH CATEGORY – Team should brainstorm all possible causes that fit into each category. Ask “Why does this happen?” As each idea is given, the facilitator writes it as a branch from the appropriate category.
- GO DEEPER TO IDENTIFY SUB-CAUSES – If you determine that you can break something down to smaller points, create branches from the main point. Again ask “Why does this happen?” about each cause. Write sub-causes branching off the causes. Continue to ask “Why?” and generate deeper levels of causes.
- ANALYZE YOUR DIAGRAM – In this stage you should have a diagram showing all of the possible causes that team identified. Depending on the importance of the problem, you can now investigate the most likely causes further. During investigation team should test which of these possible causes is contributing the most to the problem.
Conclusion
Kaoru Ishikawa passed away in 1989, but his influence remains evident in today’s quality management practices. He was not just a theorist but a visionary who saw the potential for quality control to transform not just businesses but the very way people work and think about their roles within organizations. As industries continue to evolve in the 21st century, Ishikawa’s principles remain as relevant as ever, underlining the importance of quality, continuous improvement, and collective responsibility in achieving excellence.
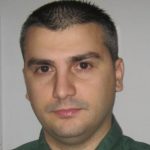
Nenad Marcetic is CIO at Lean Community. He has over 15 years of experience in Lean Management. He is a graduate of Quality Management. He has conducted more than 250 management system audits in various companies and industries (manufacturing, food and beverage, agriculture, IT services, finance, retail, mining). Since 2015 in a global automotive company, where he is responsible for process standardization and the implementation of the IATF standard.