Few words about San Gen Shugi. I recently came across a profound statement that resonated deeply, promptly earning a spot on my “memory board”. It reads:
“The strength of the organization to survive lies not in pre-determined SOLUTIONS, but instead in the ability of the people of our organization to understand the complex dynamics of the situation and to collectively find innovative and adaptable solutions.”
This insight is anchored in the philosophy of San Gen Shugi, a principle that emphasizes real places, real things, and real situations. It underscores that the vitality of an organization is not entrenched in its ability to provide instant answers but is woven into the fabric of its people’s capabilities to discern, analyze, and respond to scenarios with agility and insight. A further reflection expands the horizon of this perspective. In the competitive landscapes of business and organizational dynamics, the focal point isn’t merely on clinching victories but is strategically positioned on nurturing an environment of continual learning, enhancement, and adaptability.
“The goal is not to win in a static moment, but to cultivate an ecosystem where the skills of constant improvement, dynamic adaptation, and unwavering commitment to meeting customer needs are the bedrocks of organizational culture: EVOLUTION, NOT REVOLUTION.”
Yet, it is integral to appreciate that evolution is a precursor to revolution. It is through the intricate dance of iterative advancements and refinements that monumental shifts and transformations are birthed. Each stride in evolution sows the seeds for ensuing revolutions, where the collective competencies of an organization transcend conventional boundaries, ushering in eras of unprecedented innovation, adaptability, and value creation.
In the grand tapestry of organizational development, San Gen Shugi illuminates pathways where the convergence of individual insights, collective intelligence, and adaptive capabilities forge an organization that is not just resilient but is perpetually evolving, marked by an unyielding quest for excellence and a capacity to turn challenges into stepping stones for future triumphs.
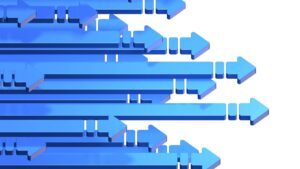
Pic. 1
I don’t know what stage your organization is at.
- Do standards exist and are they maintained?
- Do employees commit to continuous improvement?
- Does your management support improvement activities and actively participate in solving production problems on a daily basis – not remotely, not from the office, but in production?
- How much knowledge do your teams have?
- What is their knowledge regarding improvement tools?
Data Power: San Gen Shugi. One thing I am sure is that in order to operate effectively, we must rely on real data: where the problem arises – genba compare a good process/good parts with a bad process/bad parts – genbutsu facts describing the problem – where the problem occurs -genjitsu.
Whatever tool you use – whatever the method (PDCA, QRQC, A3, DMAIC, FTA, Cause and Effect Diagrams etc), the SAN Gen Shugi is the foundation – a logical approach to all methods – so go and see. Maybe it is only so little, and yet so much, but it is enough to solve the problems.
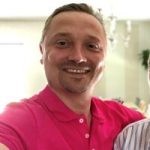
Boguslaw is certified Lean Six Sigma Black Belt. Responsible for implementing Lean Culture in the organizations, starting from 5S program, changes in the Operating System, and growth in Problem Solving Tools. He is a Lean Practitioner with over 20 years of experience in different industries.