I would like to share with You some thoughts about standardized work. I have been working with Training Within Industry TWI since 2007 and many times I have seen a lack of understanding of what work standardization is. In 2016, I included some of my observations in the book Standardized Work with TWI – Eliminating Human Errors in Production and Service processes.
Table of Contents
ToggleImportance of Standardized Work
Standardized work is not only about working according to a standard, it is mainly about building the awareness of employees. Awareness means that everyone involved knows why they are doing a given action.
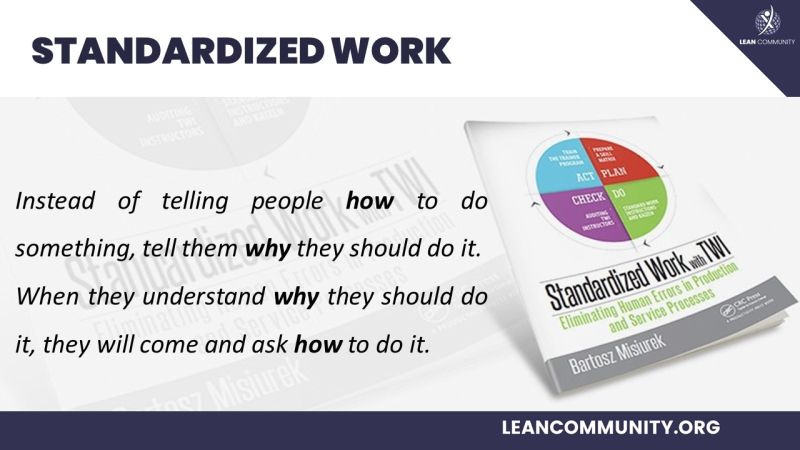
Standardized Work
When you tell a little child not to touch a hot oven, you don’t raise their awareness. Likely, the child will still go and touch the oven. Only in this way do they learn why not to do it. Telling him is not enough. Why not? People learn by experience and by understanding reasons. So, instead of telling them how to do something, tell them why they should do it. When they understand why they should do it, they will come and ask how to do it. That’s how it works when raising awareness during the implementation of Lean tools and methods.
Work standardization implementation won’t be successful when you don’t involve workers. Focus on reasons, not just on the job.
Standardized Work with TWI
Training Within Industry (TWI) has been a cornerstone in shaping effective work environments. However, its true essence often gets overlooked. Standardized Work with TWI isn’t just about following protocols; it’s about cultivating a deep understanding and awareness among employees. This chapter delves into how we can transform standard work from a set of instructions to a culture of conscious action.
The Awareness Paradigm
Awareness in the workplace transcends mere knowledge of tasks. It’s about comprehending the ‘why’ behind each action. This chapter discusses the importance of shifting focus from the ‘how’ to the ‘why’. By doing so, we enable employees to appreciate the reasoning behind their work, leading to a more engaged and effective workforce.
Lessons from Everyday Life
Drawing parallels from simple life lessons, such as teaching a child about danger, this chapter illustrates the limitations of instruction without understanding. It emphasizes experiential learning and reasoning as key components in standardizing work processes. We explore how explaining the purpose behind tasks can lead to a more intuitive and proactive approach to learning and working.
Implementing TWI with a Focus on Awareness
The implementation of TWI, when combined to raise awareness, can revolutionize the workplace. This chapter provides practical strategies for integrating awareness into standard work practices. We discuss how to encourage employees to seek understanding and how this approach can enhance the effectiveness of Lean tools and methods.
Building a Culture of Conscious Competence
Ultimately, standardized work within the framework of TWI should aim to create a culture of conscious competence. This chapter concludes by outlining steps to build this culture, where every employee is not just skilled but also deeply aware of the importance and impact of their work. This shift is crucial for creating a resilient, adaptive, and highly efficient work environment.
Meaning of SOP in Standardized Work
SOP in the context of Standardized Work stands for “Standard Operating Procedure.” This term is crucial in both industrial and business environments, representing a set of step-by-step instructions compiled by an organization to help workers carry out routine operations. SOPs aim to achieve efficiency, quality output, and uniformity of performance while reducing miscommunication and failure to comply with industry regulations.
In the realm of Standardized Work, SOPs play a vital role. They provide a detailed, written guide that explains how to perform a task correctly and consistently. This is especially important in environments where precision and safety are paramount, such as manufacturing, healthcare, and laboratory settings. SOPs in Standardized Work ensure that processes are performed consistently, leading to reliable and predictable results. They also serve as a training tool for new employees and as a reference for existing staff to ensure ongoing adherence to best practices.
Standardized Work and Kata
Standardized Work and Kata are both concepts deeply rooted in Lean manufacturing and continuous improvement philosophies. Understanding the relationship between them can help an organization optimize its processes and foster a culture of ongoing development.
- Standardized Work:
- Definition: Standardized Work refers to the documentation and implementation of the best and most efficient method to perform a task or process. This method is based on current best practices and is expected to be followed until an improved method is developed.
- Purpose: The main goal is to ensure consistency, efficiency, quality, and safety in operations. It helps in reducing variability in processes and provides a baseline for improvement.
- Components: Typically includes detailed descriptions of work tasks, sequences, timing, and the materials needed.
- Kata:
- Definition: Kata in a business context, particularly in Lean thinking, refers to structured routines practiced to master skills and ways of thinking. The two primary types of Kata are the Improvement Kata and the Coaching Kata.
- Improvement Kata: It’s a systematic, scientific routine that helps individuals and teams navigate from their current condition to a new desired condition in a creative, directed, meaningful way.
- Coaching Kata: A pattern of teaching the Improvement Kata to others, thus embedding a culture of continuous learning and improvement in the organization.
Interplay between Standardized Work and Kata:
- Foundation for Improvement: Standardized Work provides a stable baseline from which improvements can be made. Without standardized processes, it’s challenging to measure the effectiveness of any changes or improvements.
- Kata as a Vehicle for Evolution: While Standardized Work ensures consistency, Kata offers a structured approach to evolve these standards. Through the Improvement Kata, employees learn to identify opportunities for improvement within the standardized processes and experiment with solutions.
- Continuous Learning and Adaptation: Kata encourages a mindset of continuous learning and adaptation. It complements Standardized Work by ensuring that processes don’t become stagnant and are constantly evaluated and improved upon.
- Cultural Transformation: Together, they can transform the culture of an organization. Standardized Work ensures operational excellence, while Kata fosters a mindset of continuous improvement and problem-solving among employees.
Conclusions
The integration of Standardized Work, SOPs, and Kata within organizational practices underscores a fundamental synergy between theory and practical application. Standardized Work and SOPs provide a structured, consistent foundation for processes, ensuring efficiency and reliability. Meanwhile, the principles of Kata infuse a dynamic, continuous improvement mindset, fostering a culture of perpetual learning and adaptation. This harmonious blend of stability and flexibility is key to achieving operational excellence and driving sustainable growth in a rapidly evolving business landscape.
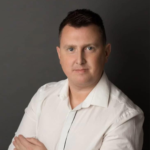
Dr. Bartosz Misiurek is a co-founder of a few start-ups like Leantrix, Lean Community, Leancoin, etwi, Lean Global Consulting, Sallar. He is a CEO at LeanTrix Ltd., Leancoin Ltd, Do Lean IT OU, and a Member of the Board at Astral Hodling OU. Author of the book “Standardized Work with TWI: Eliminating Human Errors in Production and Service Processes.” He works as Sr Manager and TWI Global Coach at Automotive Company.