TPM in Lean is the cyclical and preventive replacement of parts and subsystems that is carried out with the help of a CMMS class program. Not at all. Replacing components is only the result of a certain type of work culture – a technical work culture in which one of the most important driving elements is an operator and the Daily Inspection carried out by him. How long should this inspection take? 8 hours. This is how long an effective inspection, as part of Autonomous Maintenance, should take. Should a machine be stopped during this time, and should this time be unproductive? No!!! This is the time when the machine is working and the production process is carried out. How can this be done? Using your 5 senses as part of TPM – Autonomous Maintenance. Below is my interpretation of the 5 senses in TPM.
5 Senses in TPM Lean
Total Productive Maintenance (TPM) in Lean Manufacturing is a holistic approach aimed at maximizing the effectiveness of equipment and processes in a manufacturing setup. At the core of this approach lies the concept of the ‘5 Senses in TPM Lean’, a unique framework that encourages a sensory-driven perspective towards maintenance and efficiency. This introduction aims to shed light on how these five senses – Sight, Sound, Smell, Touch, and Taste – play a crucial role in identifying and addressing potential issues in the manufacturing environment. By tuning into these senses, workers can proactively detect anomalies, ensure safety, and maintain a high standard of quality in operations. This sensory approach enhances the overall TPM strategy, leading to more effective maintenance practices and a deeper understanding of the intricacies of manufacturing processes.
Sense of Sight
Probably the most popular and most used sense within the AUR. In addition to standard inspection lists, which include, e.g. checking the level of oil or other key elements, eyesight is an invaluable ally when cleaning machines. Remember the golden rule for cleaning: CLEANING IS AN INSPECTION! During cleaning, we can detect many anomalies that are not visible during normal operation – the damaged wiring of sensors, cracks, damaged cylinder seals, a damaged V-belt, or non-lubricated dry plate gearing.
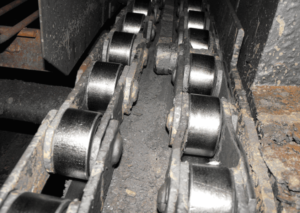
Sense of Sight
Nevertheless, some things can be “seen” while the machine is running – whether the machine is in operation, whether we like it or not, we watch it all the time. Therefore, without the need to spend any extra time, we can spot many anomalies. Broken switches, broken safety switches, oil leaks, missing equipment. All this can be seen during standard, serial production. Damaged extraction ventilation systems for gases in a machine, shortages, damaged and worn covers that protect elements against dirt, loose sensors – all these anomalies are visible, with our eyesight. All we have to do is try to see them, even though we are looking at them all the time.
Sense of Hearing
Can you not see anything? So maybe you can hear something? Of course, you can hear something. Machines make a lot of noise. And not only the “process” machines but also those that confirm the poor condition of the machine park. It is enough to stop for a moment and stand for a few minutes by a machine, and various and previously inaudible sounds will start flowing to our ears. Perhaps it will be a hissing. Don’t worry, it’s not a snake. Although it might be a pneumatic hose. Air leaks are a very common malfunction. Apart from consequences in the form of failure, there are also financial losses. Some sources say that each loud hissing point is a loss of about PLN 1,000 a year! Think, you have a specialist on a machine who can detect this leak for you after appropriately building his awareness. Does nothing hiss? Maybe something squeaks? Dry and non-lubricated linear guides are often loud. They don’t squeak, but instead even scream for some grease!!! If we do not hear this scream, the consequence will be the failure of these components. Even if we fail to restore the full functionality of these elements, this sound, which is picked up by an operator and reported to the Maintenance Service, will be an impulse for Corrective Maintenance. And that’s a lot. These are not the only sounds that can come from our machines. Various kinds of knocks, rubbing, and the shooting of loose chain gears – these is only some of the noises that can reach our ears if we listen to the work of a machine for a moment.
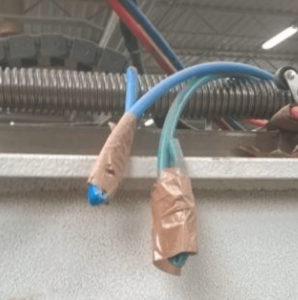
Lean TPM Sense of Hearing
Sense of Touch
The deteriorating condition of a machine can also be felt. Often, a quick touch is enough to know that we have a “pre-infarction state”. The deteriorating condition of the bearings, apart from their loud work (hearing), usually also causes vibrations. It is enough to touch the machine casing, or its subsystem (following safety rules, of course), to know – without the use of a vibrometer – that something is not as it should be. Such a simple diagnosis, and the obtained information, are enough for the technical services to start more in-depth diagnostics. Speaking of bearings, when they are worn and not lubricated, heat is often generated, which can also be felt through the sense of touch (heat radiation). Touch will also support us during the periodic cleaning of machines (read inspections). Loose parts, cracks, and worn surfaces can be spotted using this sense.
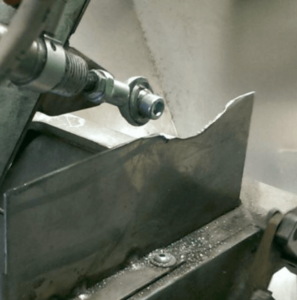
Sense of Touch
Sense of Smell
Sometimes it is possible to have a “nose to failure”. Literally. Maybe the sense of smell is not the main sense we can use to prevent failures within TPM, but it is sometimes useful. The characteristic smell of fused electrical insulation is well-known to most of us. Therefore, a conscious operator, plus a good nose, can protect a plant from a serious breakdown. You might also smell oil or lubricants burning somewhere on a machine. Leaks of certain technical gases that are used in the process are also detectable using the sense of smell. One of my greatest authorities, my dad, was able to diagnose the inevitable end of a clutch in a car of his clients by the characteristic smell of burning. Without even disassembling it!
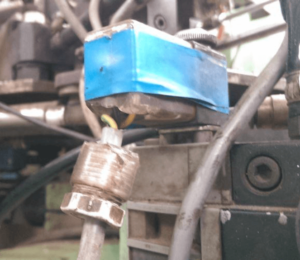
Sense of Smell
Sense of Taste
Finally, perhaps the least used sense in TPM – taste. Of course, no one talks about “tasting” grease, oil or other components. “Some gases, like acetylene which leaves a sweet aftertaste, can activate the sense of taste. Depending on the nature of the production process, this sense can play a more or less significant role in Total Productive Maintenance (TPM). In environments where specific gas emissions are a part of the process, operators can leverage their sense of taste as a tool for detecting anomalies or changes in the production line.
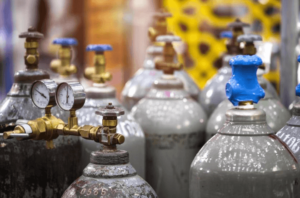
Lean TPM Sense of Taste
I have briefly tried to introduce you to the topic of the 5 senses we have, as well as their use in TPM. Their strength does not lie in sophistication, precision or complexity. So why is it worth using them every day and all the time? I can only think of one reason.
5 Senses in TPM Lean – Real Examples
The ‘5 Senses in TPM Lean’ framework is a cornerstone of modern Total Productive Maintenance, redefining traditional maintenance practices. This sensory-driven approach enhances operators’ perception and interaction with the machinery, offering a more intuitive and effective method for maintaining and improving production processes. Let’s delve deeper into how each sense contributes to this innovative framework. Let`s use real examples:
- Sight: An operator notices a slight discoloration on a conveyor belt, indicating excessive wear in a specific area. This visual cue prompts an immediate inspection, revealing a misalignment in the belt rollers. Early detection and correction of this issue prevent a potential breakdown, ensuring continuous operation.
- Sound: During a routine operation, an operator hears an irregular clanking sound coming from a hydraulic press. Familiar with the machine’s normal operating sounds, the operator quickly identifies this as abnormal. The investigation reveals a loose component that, if left unchecked, could have led to significant damage or operational downtime.
- Smell: While walking through the production floor, an operator detects a faint burning odor near an electric motor. Recognizing that this smell is unusual and could indicate overheating or an electrical issue, they immediately report it. The maintenance team discovers a wiring problem, averting a potential fire hazard.
- Touch: An operator, while handling a piece of machinery, feels an unusual vibration that wasn’t present before. Trusting their tactile experience, they report this change. A subsequent examination finds an imbalance in the machine’s moving parts, which is promptly corrected to prevent further mechanical stress.
- Taste: While taste is less commonly used in industrial settings due to safety concerns, it can be relevant in certain industries like food and beverage manufacturing. For instance, an operator notices an off-taste in a sample product from a production line. This alerts them to a possible contamination or process deviation, triggering a quality control check to ensure product integrity.
These examples demonstrate the practical application of the ‘5 Senses in TPM Lean’ approach, showcasing how empowering operators with sensory awareness can lead to proactive maintenance, enhanced safety, and improved operational efficiency.
Conlusions – TPM Lean
Total Productive Maintenance (TPM) in Lean Manufacturing transcends the traditional view of maintenance as merely a cyclical and preventive replacement of parts. It represents a profound shift towards a technical work culture where the operator, empowered by the practice of Daily Inspection, plays a pivotal role. This inspection, far from being an eight-hour interruption, is seamlessly integrated into the regular working hours. It exemplifies how maintenance can be proactive and productive without halting the machinery or the production process.
By leveraging these senses, TPM in Lean Manufacturing enables workers to proactively ensure safety, quality, and efficiency. It’s not just about maintenance; it’s about creating a symbiotic relationship between the operator and the machine, where each is attuned to the needs and signals of the other. This approach cultivates a culture of continuous improvement, where each member of the team is an active participant in the maintenance process.
I was lucky that everything I learned about Lean, Kaizen, or production optimization started in a Japanese company. There, under the supervision of Japanese staff and during training in Japan, I learned how to approach the Continuous Improvement process. Over time, I also learned about other practices in other companies.