Lean Consultant – diary. Being a lean consultant is a simple profession and easy money? Nothing could be more wrong! Before starting each new project, I experience a lot of stress. It’s not only because I am afraid of difficult, practical questions, although that is one of the reasons. People from factories expect an immediate answer to such questions, because they have been thinking about them for hours. In most cases, I can answer correctly. I have been involved in consulting for almost 20 years, and in over 150 factories I have encountered many problems that I have been able to deal with. However, there is always something that requires deep thought. It is no coincidence that during my 8 years of working in one of the largest consulting companies in Poland, many new consultants from the industry have come and only lasted for a maximum of six months. There were various reasons for this. This profession, however, requires a lot of resistance to stress and flexibility. It is completely different to working in industry. I know this because now I spend most of my time working for one of the corporations from the automotive industry. When it comes to consulting, my biggest concerns are not so much about the substantive questions, but about the organization of the factory I am supposed to advise. I’m especially concerned before the first workshop day. In the morning, when I wake up a few minutes before my alarm clock, I lie in bed and figure out the entire schedule in my head. Today I’m running a workshop called “Instructing Employees” from the Training Within Industry program. It makes no difference to me that I’ve already done it five hundred times. There are always emotions. That’s what I love about this job. In my mind I repeat to myself like a mantra: “Let it be a well-organized factory …” Yes, only in good factories can Lean methods be instilled, and it is only there where workshops are really successful. In bad factories, the implementation usually fails, and my job is a waste of time. In the case of the workshop entitled “Instructing Employees”, organization is especially important because the main workshop activities take place in the production hall.
Table of Contents
ToggleA lean consultant and a bad factory
I drive up in my car. It’s 7:00 in the morning. I came an hour before the start of the workshop. In practice, I need 15 minutes to prepare the materials. A Lean consultant needs to be organized. The factory looks new. I’m go to the gate. There are no marked places for guests. I park on the pavement. I go to the security booth and inform them that I have a training workshop today. I can see the surprise on their faces. I ask if I can drive behind the gate. I have heavy materials. Unfortunately, it requires a special pass. I leave it. They ask me who I have an appointment with. I check on my phone and give them the name. They call, but no one is answers. I ask what number they are calling. The security guard replies that the stationary phone. I know from experience that people in production rarely sit at their desks. I tell them that I have a mobile number for this person and I can make a call. I hear that it is impossible because their duty is to inform my guide. I’m wait 10 minutes. There are only 50 minutes left until the workshop starts. After several unsuccessful attempts to connect, they leave it and I hear: “Call him.” – so I call. My guide shows up. It’s 7:20 a.m.
Preparation for the workshop
We go to the room. People in offices are drinking coffee. It feels like morning. Here work starts at 7:00 a.m. Everyone is looking over their coffee cups at me. I know that feeling. This is always the case when you enter a completely new place. A Lean consultant does this at least twice a week. I understand their interest. Eventually someone new shows up. We slowly move to the training room. In the room I look around. I can’t see the projector. The flipcharts are all written on. I can only see one marker. I ask the guide about the projector. This is what I hear as the reply: “Hmm. It should be somewhere here. Please give me a moment.” I sense the end of this action. Fortunately, I always have a spare projector in my boot. I don’t hang around for too long and start to unpack. Textbooks and pens are arranged. The guide comes back and informs me that unfortunately there will be a board meeting in this room at 2 p.m. and we have to change the place of the workshop. It’s 7:40 a.m. I collect all my things nervously and move quickly with all my stuff. Fortunately, there is a projector in the new room. Just those written on fipcharts again… I get the new ones after 10 minutes. I lay out my materials once more. It is 7:55. We are about to start. I’m nervous.
The beginning of the workshop
It’s 8:00 o’clock. I’m prepared. I already wrote down the training agenda for the participants. I know where the light switches are. This is very important when I show training videos. A Lean consultant must pay attention to details. There are suspiciously few people in the room. I nervously look at the list of participants. Half are missing. It turned out that they were waiting in front of the other room. I go to get them and bring them to the right place. I introduce myself because there is no one from the factory who cansay a few words of introduction. I ask the participants if any of them know what the workshop will be about. Neither of them has any clue. Five people found out about the training yesterday. Three were working overnight and are barely conscious. So I explain what we will talk about. I present the method and try to interest them by telling them how it can help them in their daily work. The only question after my introduction is “What time will we finish?” With disgust, I point my finger at the agenda and I begin.
Work in progress
Lean Consultant – diary. When conducting workshops, I always give my best. This is my nature. As a Lean consultant, I have to like performing. And this is how it is! It makes no difference to me if there are 15 or 400 people in the room. I try to connect with each of the participants. My goal is clear. I want to encourage them to practice the method I am presenting. I want them to understand it and like it the way I do. I can see in the eyes of the participants that what I am presenting is understandable. They laugh at instructional videos. Their real amusement is caused by an excerpt from the series “Friends”, in which Ross goes to the solarium. He is there only trained orally. However, when I move on to the hardest part of the workshop – the development of the TWI Manual – I see people shutting down. As if they wanted to say to me, “Finish it now, because we have more important things to do.” I am so tired. The worst thing is that so are the participants … When it comes to choosing an operation for practical activities, I hear: “It’s best not to go into production, because nobody will let us close to the machines.” I calm things down, and choose some production-related operations so that we don’t disturb anyone…
The end of the workshop
Being a Lean consultant is a very intensive job. When I was auditing the workshops of less experienced consultants and we were driving home together, they sometimes fell asleep on the way like little children. I’m not exaggerating. I have completed many marathons and half marathons in my life, so I have a high threshold for fatigue. It is now 4:00 p.m. It’s getting dark outside. Nobody has been in the room for over 30 minutes. There were no questions. No summaries either. The survey grades are very good. They liked the training. However, to my question of: “What now?” I heard they were going home. Of course, I meant, “What about the TWI program now?” But I didn’t take it any further. At 4:10 p.m. a lady from HR came to me. I told her that I want to speak to someone from the management. I heard the reply that the 2:00 p.m. meeting was overdue and the director would call me the next day. I left her the surveys. She was very pleased with the results. I waited for a call from the director the next day without any result…
A lean consultant and a good factory
I drive up in my car. It’s 7:00 in the morning. I showed up an hour before the start of the workshop. In practice, I need 15 minutes to prepare my materials. A Lean consultant needs to be organized. The factory looks new. I go to the gate. Clearly marked parking. I leave my car and go to the security booth. I give my last name. The security guard gives me a previously prepared pass and indicates the place where I should go. He also invites me to park on a specially prepared parking space for me. I informed the factory people that I had heavy materials. The security guard instructs me that an SMS has been sent to my guide saying that he is meant to pick me up from the reception desk. I park my car, pick up my materials, and enter the building. I can see the sign: “Reception”. My guide is waiting for me. We welcome each other. It is 7:05.
Preparation for the workshop
We go to the room. People in offices are drinking coffee. It feels like morning. Here work starts at 7:00 a.m. Everyone is looking over their coffee cups at me. I know that feeling. This is always the case when you enter a completely new place. A Lean consultant does this at least twice a week. I understand their interest. Eventually someone new shows up. We slowly move to the training room. On the door to the room there is a note with the inscription: Practical Workshop Training Within Industry (8:00 – 16:00). Everything is prepared in the room. Water for the participants and fresh flipchart cards. Markers in their places. Four colors. I can see immediately that the room is prepared according to the 5S rules. In such situations I always realize why I like Lean Management tools so much. I received information from my supervisor that each participant had received an invitation letter informing him about the place of the workshop and the agenda. I lay out my materials. The title slide of the presentation lights up on the white canvas. It’s 7:20 a.m. I have plenty of time to drink coffee and talk to people in the factory about selected practical operations for the TWI workshop. I am prepared and full of enthusiasm. I wait impatiently for the start of the workshop.
The beginning of the workshop
It’s 8:00 o’clock. I’m prepared. I already wrote down the training agenda for the participants. I know where the light switches are. This is very important when I show training videos. A Lean consultant must pay attention to details. All the participants are sitting in the room from 7:55 a.m. Punctually at 8:00 a.m, the factory manager comes in and reminds us for 10 minutes why this training is important. He motivates them. I’m telling you that “he reminds us” on purpose, because a week earlier he had a meeting with the participants, during which he introduced each of them to the purpose of the workshop and explained what the TWI program is all about. The director attended a management training course, where a pilot area was established and people were assigned to participate in the practical workshop. The company decided to implement the TWI program through the LeanTrix system, and therefore each participant had already been given at least one TWI instruction to prepare. Even people from the HR department, who are present at the workshop, were given their tasks. One of them, for example, was to develop a TWI Instruction for the process of filling in foreign delegations. Apparently, employees make many mistakes while performing this operation. After the introduction of the director, I start the training.
Work in progress
I can see a lot of interest. The participants write down the most important things. A special excitement occurs when I present the topic of creating the TWI Instruction. I even hear requests for very thorough and slow explanations. It turned out that by the end of the week most of the participants are meant to create their own TWI Instructions. At the beginning, I mentioned that this is one of the most difficult parts of the training. While leading it, I spent most of my time answering many substantive questions. Time flew very fast and, most importantly, the training was constructive. When it was time for practical activities, I was given a list of participants assigned to the operations. Everyone knew exactly where to go and what to do.
The end of the workshop
Being a Lean consultant is a very intensive job. When I was auditing the workshops of less experienced consultants and we were driving home together, they sometimes fell asleep on the way like little children. I’m not exaggerating. I have completed many marathons and half marathons in my life, so I have a high threshold for fatigue. It is now 4:00 p.m. It’s getting dark outside. Half of the participants are still in the room. They shout over each other asking questions. I try my best not to leave them unanswered. 10 minutes before the end, the factory director summed up the workshops and shook hands with each individual. I am very tired, but also fulfilled. This is a feeling very similar to the feeling when I finish a long distance run. Exhaustion, but also great joy.
Thoughts
As a Lean consultant and industry practitioner, I visit many Lean Management conferences. I am often bothered by people from industry. I already have some achievements and reputation. I have implemented this program in many countries and in different cultures, which always arouses curiosity. Sometimes I hear that the TWI method is really cool, but it cannot be used everywhere due to the specificity of production. I always remember the image of a good factory and a bad factory. I wonder which one my interlocutor is working in. The answer is obvious. I always perversely tell such a person that I would like to visit them, because I have never seen a factory where there are no people at all in production. I cause consternation: “But our factory employs 150 direct production workers…”. I ask ironically: “So why can’t their work be standardized? Are they any special people? ”. My interlocutor senses sarcasm. He answers hesitantly: “But we have such specificity that…”. I answer with the question: “Such specificity or such organizational culture…?”
A gradual change of cultures
Implementing Lean methods and tools is like losing weight. The key is to diagnose the problem. Later, you need to realize that your body is not very special and that any person who is not sick can lose weight. You then need to establish an action plan. Set a goal using the SMART approach, and move forward in small steps. You need to change some habits, because the most difficult thing about losing weight is to appreciate small successes and not go back to old habits. When you lose weight – you change the culture of eating, and when you implement Lean – you change the culture of work organization. This is a huge challenge. Your body must be like a good machine, whereas your plant must be like a good factory.
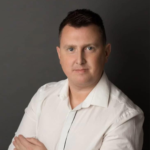
Dr. Bartosz Misiurek is a co-founder of a few start-ups like Leantrix, Lean Community, Leancoin, etwi, Lean Global Consulting, Sallar. He is a CEO at LeanTrix Ltd., Leancoin Ltd, Do Lean IT OU, and a Member of the Board at Astral Hodling OU. Author of the book “Standardized Work with TWI: Eliminating Human Errors in Production and Service Processes.” He works as Sr Manager and TWI Global Coach at Automotive Company.