Guidelines for creating work instructions are essential for effective process management in both production and service sectors. A well-written instruction supports the instructor during training sessions. It also serves as a valuable reference for employees after training. This article discusses the most important guidelines for creating work instructions. These guidelines will help you develop documentation that facilitates training and improves employee efficiency.
Table of Contents
ToggleThe Main Rule of Creating Work Instructions
The key rule for creating work instructions is not to give instructions to employees before training. When an employee receives instructions without prior training, misunderstandings may occur. The text may not always clearly convey the author’s intentions. As a result, this can lead to serious errors such as machine failures, accidents, or other problems. Therefore, it is crucial that employees undergo training before they start using the instructions on their own.
5 Key Rules for Creating SOPs
1. Use a Maximum of 5 Words for Steps and Guidelines
First, use no more than 5 words to describe the main steps and guidelines. This makes it easier for the instructor to reference the SOP during training. Remember, the instruction is primarily for the instructor. It becomes useful to the learner only after the training.
2. At Least 5 Words to Describe Reasons for Guidelines
Be very precise when describing reasons. The explanations are mainly for the learner after the training. During the training, when you state the guideline, the reason will come naturally. This simplifies the process of passing on knowledge.
3. Start Each Step with a Key Verb
A key verb represents the specific action. Start each main step with this verb. This will help you quickly understand the step when conducting the training.
4. Avoid Verbs in the Guidelines
Guidelines should answer the question, “How to do it?” and not “What are you doing?”. Describe the guidelines briefly. Include only information that highlights potential human errors, injuries, or ways to simplify the task.
5. Ask “What Happens If…?” When Searching for the Cause
Ask, “What happens if…?” to find the true cause. Avoid general phrases like “operator error” or “quality assurance.” The cause should explain what happens if the task is done differently than the standard.
The Importance of Guidelines for Creating Work Instructions in Process Improvement
Well-prepared work instructions support process efficiency. They also contribute to continuous improvement in the organization. Applying the guidelines properly helps train new employees. It also enables standardization of activities. This leads to effective implementation of improvements. Taiichi Ohno once said, “There can be no Kaizen without standards.” Well-prepared instructions are crucial for optimizing production processes.
Conclusion
In summary, guidelines for creating work instructions are essential for effective team management and process quality improvement. A well-designed instruction helps instructors conduct training and reduces employee mistakes. It also enhances the quality of tasks. I hope these guidelines will assist in creating effective instructions. These instructions will help your team develop their competencies and improve your organization’s processes.
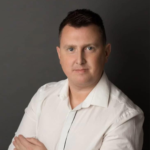
Dr. Bartosz Misiurek is a co-founder of a few start-ups like Leantrix, Lean Community, Leancoin, etwi, Lean Global Consulting, Sallar. He is a CEO at LeanTrix Ltd., Leancoin Ltd, Do Lean IT OU, and a Member of the Board at Astral Hodling OU. Author of the book “Standardized Work with TWI: Eliminating Human Errors in Production and Service Processes.” He works as Sr Manager and TWI Global Coach at Automotive Company.