TWI Job Methods in SMED – Synergy of actions
Changeovers in factories are not unusual in today’s times. Everyone in an organization would like to have as few of them as possible, but the customer has a decisive influence on their number. Customer needs are varied which is why more and more products, with different specifications, are created, with the consequence of this being a growing number of changeovers. Thus, the competitiveness of producers is influenced by their flexibility with regards to changes in production. Those who can efficiently adapt production lines and cells to customer requirements will have an advantage. This article shows the synergy of activities between the TWI Job Methods and SMED.
Introduction
There is a lot of talk about the culture of continuous improvement in companies. The managerial staff want every employee to get involved in Kaizen activities, in turn increasing the quality, safety, and efficiency of work at their positions. However, the reality turns out to be different. Employees are reluctant to communicate and implement their ideas. Due to their reluctance to go ahead with their ideas, as well as their fear of criticism, they hide their ideas in a drawer. In rare cases, they implement them in their work without passing on information to others. These issues apply to almost all departments and operations in the company – from maintenance to production. Changeover processes are particularly sensitive to a lack of improvement.
Due to the requirements of the conversion market, changeovers will not disappear from our companies, but we can work to optimize them. The tool used in this area is SMED ( Single Minute Exchange of Die). SMED involves bringing the changeover to a state where it is possible to perform it in a single-digit number of minutes. SMED workshops are very popular, but the most difficult thing is to unleash the creativity of employees. Based on several projects in various companies, we have found that the most effective method of solving this problem is the use of TWI Job Methods in activities related to SMED.
TWI Job Methods – a tool for continuous improvement
TWI Job Methods is one of the three elements of the TWI program, alongside TWI Job Instructions and TWI Job Relations. TWI JM was created as a result of the need to optimize the heavy physical work carried out by men in armaments plants. In the 1940s, in the United States, women were employed in large numbers in the industry, replacing the men who were sent to the war fronts in Asia and Europe. TWI Job Methods proved to be the most effective tool for improving processes for delivering equipment to the battlefields quickly enough.
TWI Job Methods consist of four steps that lead through the entire improvement process. Like all methods of TWI programs, it is based on the PDCA cycle, which makes it a simple and effective tool.
1. BREAKDOWN the Job
The first step is to analyze the current state by listing all details in a given operation. Details are elements of work performed by humans. It takes into account all issues related to the movement, material collection, manual work, and machine work in which the operator is involved. We do this step directly at the analyzed position. A key element of this step is also the collecting of observations such as safety hazards, and difficulties in the job or
distance traveled. People at this stage are very often willing to provide ready-made solutions to improve, instead of just observing. However, this is a mistake that can lead to the greatest waste – trying to improve on things that shouldn’t be done at all. To prevent this, go to step two of the method right after the Breakdown of the job.
2. Question every detail
This step is a brainstorm generator and is key to triggering creativity among employees. At this stage, ideas emerge that are not subject to criticism, which ensures that creativity is not blocked. A brainstorming session is conducted with six questions for each detail. By following the order of the questions, the improvement of the process can be successfully carried out. Table 1 contains questions (with explanations) that enable a systemic approach to optimization.
Question | Explanation | |
1. Why is it necessary? | Why? | The question why is most often directed to the person who knows the process best. This question aims to check if a given operation can be performed without this detail, or If it is possible to implement changes that will make it possible NOT to perform this detail while maintaining the safety of quality, efficiency, etc. |
2. What is the purpose of this detail | What? | The question What is the control question for the previous question. The key is to check If a given detail is not a waste. We ask this question ourselves, searching for the 8 types of waste.
If we manage to find a solution to eliminate the detail, we do not move on to the next questions. |
3. Where should it be done? | Where? | At this stage, we verify the legitimacy of the detail in the place where it is currently taking place. Perhaps the collection material could take place closer to the workplace? Thanks to this, we can better arrange the workplace. |
4. When should it be done? | When? | In this question, we check If a given detail is positioned at the right time during the process. In other words, we are looking for ideas that allow for the longest possible uninterrupted sequence of value-adding details. For example, preparation activities can often be excluded beyond the machine’s working time. |
5. Who is best qualified to do it? | Who? | This question checks if the person who is currently performing the detail is suitable. People who do not have sufficient qualifications often perform procedures that they should not perform. On the other hand, it happens that highly qualified people do jobs that could be performed by people with lower qualifications. |
6. How is “the best way” to do it? | How? | The last question on this list is the question of improvements. Only at the very end do we look for ideas that will allow us to perform a given detail in a safer, more efficient, and easier way. |
The 5W1H method used in the second step prevents the improvement of details that should not be performed at all. This is a fundamental mistake, which leads to a serious loss which is an improvement of waste. In addition, a number of questions are asked in this step, which ultimately allows the place and time of details to be determined. Thanks to this, Kaizen ideas are dedicated to the ultimately defined process in the current situation.
It is very important to write down all ideas, and not to judge them.
3. Develop a new method
This step is largely based on the selection of brainstorming ideas in step two. We decide which details will be eliminated, combined, and reorganized, and we decide what ideas for improvement should be implemented. For this purpose, we put all ideas on the matrix that allow us to determine the sequence of their implementation. Each of the improvements should be assessed in terms of implementation difficulties and expected benefits. The solutions are then selected and written on the TWI instruction.
4. Apply the new method
The last step of the method focuses on gaining the support of the management and operators in the workplace. We should check with other departments in the company for issues related to safety, quality, and costs. After obtaining the final approval and implementing the ideas, it is necessary to use the TWI IP method to train the staff. Thanks to this, we can be sure that the standard will not only be effectively communicated, but also understood by operators.
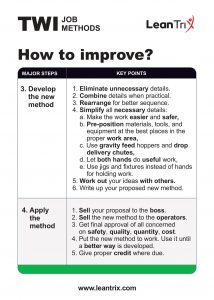
Figure 1 TWI Cards
The use of TWI JM in SMED
SMED is a four-step method that allows the changeover time to be reduced. In the first stage, the process is analyzed. A video is recorded in order to help you see all the essential elements of the setup. The analysis is the basis for the next step of dividing the process into internal and external operations. The third stage is responsible for rearranging the current internal operations so that they can be carried out beyond the duration of the changeover. At the very end, in the fourth step, internal processes are streamlined in order to shorten their execution time.
TWI Job Methods are helpful at every stage of changeover improvements. The steps and directions of the method allow for a structured approach to SMED. The 5W1H questions guide you through all 3 steps following the changeover analysis. TWI JM paves the way by specifying what, and in what order, things should be done. For this purpose, an improvement sheet is used. Figure 2 shows which SMED stage corresponds to which stage in TWI JM. The SMED Analysis stage is consistent with the entire first step of the method, which extends its scope to include the need to record observations. Observations help pinpoint improvement solutions for changeover to be more accurate. The second step of the method refers to the first two questions which help to eliminate operations that do not bring value. The third stage is the change of internal into external elements thanks to three key questions, where, when, who, we find ideas for reorganizing the process more effectively. The last element is the improvement of internal operations, where thanks to TWI we not only limit ourselves to reducing time, but also look at other aspects such as safety and quality.
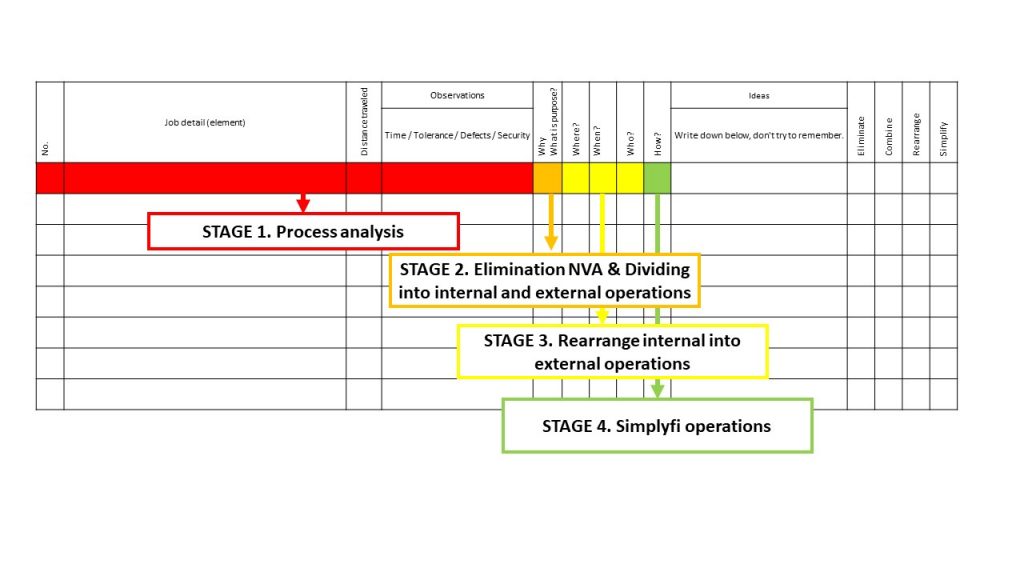
Figure 2 Application of TWI JM in SMED
Summary
TWI Job Methods and SMED are very effective tools used for process optimization purposes. The use of two of them at the same time is a combination that gives enormous possibilities. SMED is supplemented by TWI with a brainstorming generator in the form of 5W1H questions. On the other hand, TWI JM is supplemented by SMED with a methodical approach dedicated to changeovers, e.g. a division into internal and external activities. Thanks to this, we get a duo that allows us to unleash the creativity of employees with regards to optimizing changeovers.
You can buy PDF version of this article on the Lean Global Marketplace
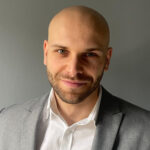
He is a Senior Consultant of the TWI program and Lean Management at LeanTrix. He is also a leader in the startup project - etwi system. He was a member of a global team that implemented the TPM system for several automotive plants in Europe, Asia, South America and North America.