Standard work audit is the key element of improving culture and a great way to collect observations on the shop floor. The direct supervisors (leaders and foremen) are mainly responsible for auditing processes related to work standardization. Work standardization refers to the process of establishing and maintaining consistent, documented, and well-defined procedures, methods, and practices for performing tasks or activities within an organization. The primary goal of work standardization is to ensure that work processes are carried out efficiently, accurately, and consistently by all employees.
Table of Contents
ToggleStandard Work Audit – Example
The table in the picture below gives an example of the Standard Work Audit sheet. It should include closed YES/NO questions. YES means that an auditor has no comments on the area or process subject to the audit. Based on workplace observations, instructions, and the operator’s performance, auditors make decisions by themselves, marking their answers on the audit sheet. Each inconsistency on a work standard has to be written down on the audit sheet, and changes should be implemented, preferably before the end of the operator’s work on the same day. Such an auditing process is called the co-shift audit.
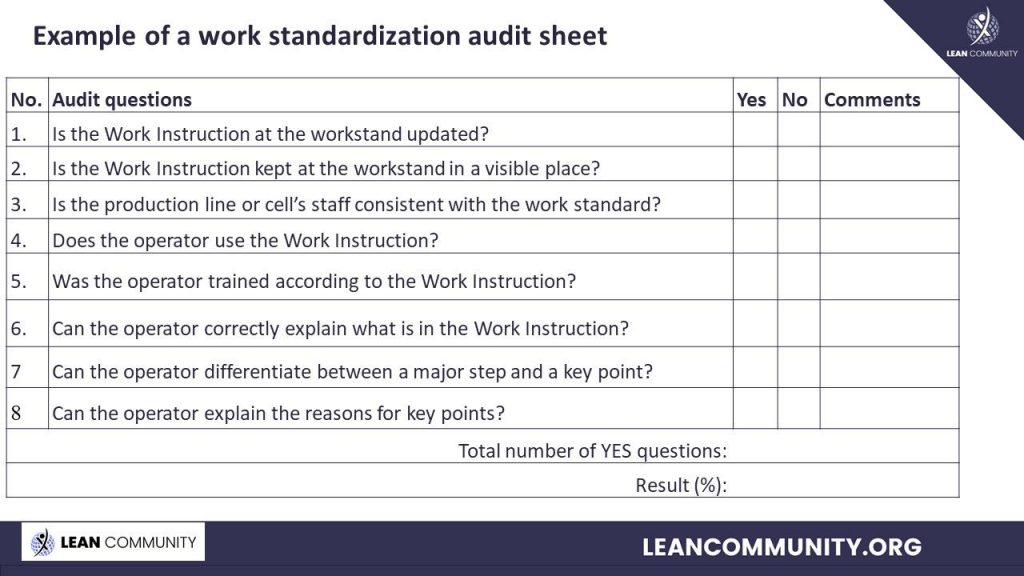
Standard Work Audit – example
Consistent and regular auditing is one of the most effective tools for work standardization observation. Moreover, a correct audit is a tool for identifying problems in an audited area, which can lead to improvement. Based on inconsistencies, countermeasures would next be defined to improve the area.
Standard Work Audit – Usage
Standard work forms the backbone of efficient and productive operations in various industries. To ensure the effectiveness and sustainability of standardized work, consistent auditing becomes a vital tool for observation and improvement. In this article, we will explore the significance of standardized work audits, their role in identifying potential issues within audited areas, and the subsequent implementation of targeted countermeasures. By conducting thorough audits and taking corrective actions, organizations can drive continuous improvement and enhance overall operational performance.
The Importance of Standard Work Audits
Standardized work audits serve as a systematic approach to assess the adherence and effectiveness of established work standards. By conducting regular audits, organizations can ensure that work processes are being followed consistently, leading to enhanced efficiency, quality, and safety. Audits also provide valuable insights into areas that require improvement or adjustments to meet desired performance levels.
Identifying Problems and Inconsistencies
During a standardized work audit, auditors closely observe the audited area, evaluating the extent to which work standards are being followed. This includes assessing the sequence of tasks, standard operating procedures, work instructions, and overall compliance with established protocols. Auditors meticulously identify inconsistencies, variations, or deviations from the prescribed standards, allowing them to pinpoint potential problem areas.
Defining Countermeasures for Improvement
Once problem areas have been identified through the audit process, the next crucial step is to define and implement appropriate countermeasures. Countermeasures are targeted actions or interventions aimed at resolving the identified issues and improving the audited area’s performance. This could involve revising or updating work instructions, providing additional training or support, or implementing process modifications to enhance efficiency.
Driving Continuous Improvement
Standardized work audits play a pivotal role in driving a culture of continuous improvement within an organization. By consistently monitoring and auditing work processes, organizations can identify recurring issues, track improvement progress, and ensure sustained adherence to established standards. This iterative approach allows for ongoing refinement and optimization of work processes, ultimately leading to enhanced productivity, quality, and customer satisfaction.
Standardized Work with TWI
In this chapter, we delve into the powerful combination of Standardized Work and Training Within Industry (TWI). The synergy between these two approaches forms the foundation for improved productivity, consistency, and employee skill development.
Understanding Standardized Work
Standardized Work, as previously discussed, involves creating well-documented and consistently followed procedures for tasks or processes within an organization. It aims to eliminate variations, reduce errors, and enhance efficiency.
The Role of TWI
Training Within Industry (TWI) complements Standardized Work by focusing on developing and improving the skills of the workforce. It consists of three essential components:
Job Instruction (JI)
JI ensures that employees can quickly and effectively learn how to perform tasks following Standardized Work instructions. It emphasizes breaking down tasks into key steps, training employees, and providing them with the necessary knowledge and skills.
Job Methods (JM)
JM focuses on improving work processes by encouraging employees to suggest and implement better methods. This aligns with the continuous improvement aspect of Standardized Work, where employees are empowered to identify inefficiencies and propose solutions.
Job Relations (JR)
JR emphasizes building positive relationships and effective communication within the organization. It ensures that the human aspect of work is considered, as motivated and engaged employees are more likely to adhere to Standardized Work procedures.
The TWI and Standard Work Audit Integration
The integration of TWI with Standardized Work is a dynamic approach. While Standardized Work provides the framework for consistent processes, TWI equips employees with the skills, knowledge, and motivation to adhere to these standards.
- Through JI, employees are trained to follow Standardized Work instructions accurately and consistently.
- JM encourages employees to identify opportunities for process improvement, enhancing the Standardized Work itself.
- JR fosters a positive work culture where employees are engaged, motivated, and committed to maintaining Standardized Work practices.
Benefits of the Combination
The synergy between Standardized Work and TWI leads to several significant benefits:
- Reduced errors and defects due to well-trained employees following standardized procedures.
- Improved efficiency and productivity through the elimination of wasteful steps and the continuous pursuit of better methods.
- Enhanced employee engagement and job satisfaction, resulting in higher morale and better adherence to Standardized Work.
Implementing Standardized Work with TWI
Implementing this combination involves a structured approach, starting with the identification of processes or tasks that would benefit from Standardized Work. Once the standardization is established, TWI components, such as JI and JM, can be introduced to train and empower employees effectively.
Conclusions
Standard work audits are an essential component of work standardization and continuous improvement. By conducting regular audits, organizations can identify inconsistencies and problem areas, paving the way for targeted countermeasures that improve performance and efficiency. Embracing a culture of auditing and continuous improvement ensures that work processes remain aligned with established standards, leading to enhanced operational excellence. By harnessing the power of standardized work audits, organizations can drive sustainable growth, maximize productivity, and achieve their desired business outcomes.
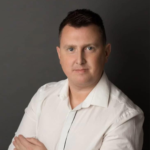
Dr. Bartosz Misiurek is a co-founder of a few start-ups like Leantrix, Lean Community, Leancoin, etwi, Lean Global Consulting, Sallar. He is a CEO at LeanTrix Ltd., Leancoin Ltd, Do Lean IT OU, and a Member of the Board at Astral Hodling OU. Author of the book “Standardized Work with TWI: Eliminating Human Errors in Production and Service Processes.” He works as Sr Manager and TWI Global Coach at Automotive Company.